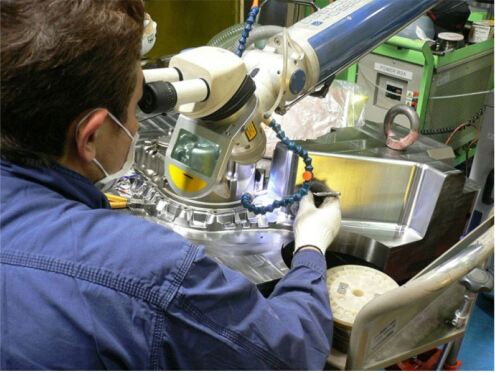
文:慕红英
重庆环泰机械制造有限责任公司
前言
模具好比锅,压铸机好比灶,怎样把饭煮熟就是压铸工艺了,如果锅漏了,饭还煮得熟吗?这是把压铸生产过程形象地比喻成做饭,同时也说出了模具在压铸生产中的重要性。
前期的模具设计、制作固然重要,但在压铸生产及产后维护保养过程中,模具使用及维护保养的好坏也是相当关键的,它直接影响到模具寿命、生产效率和坯件的质量等,这些都直接与压铸成本密切相关。要降低压铸成本,减少人为因素造成的不必要的浪费,我们就必须在模具的使用及维护保养等把工作切实做细、做到位,以提高产品市场竞争力。
1 为每套模具建立档案
模具档案的建立始于模具制作计划的开始,详细填写产品型号、模号、冲头直径、适用压铸机型、模具主型材料等,前期方案分析及模拟、更改、试模走样过程中存在的问题及解决,直至样件验收合格模具回厂移交使用部门,这部分可由负责前期模具开发的工程师填写。
模具回厂后验收,包含对模具制作厂家提供的资料及备件的验收,硬度检测及试模情况,模具回厂日期等都需详细记入模具档案里,如果是复制模具,还要关注如同一类型油缸及备件的互换性问题,做到通配以减少库存量。
模具投入量产后,详细记录模具生产数量,最近一次生产日期及维修、维护保养情况及备件更换情况等,这样就可以随时查阅某套模具的使用情况,啥时换过什么零件,修过那些部位等。
模具报废后,记录报废原因及时间,统计出总的压铸数量,模具档案随模具报废作封存处理。如遇模具报废改制或启用,需重新履行手续后,继续填写。
2 模具在使用过程中的管理
模具在使用过程中,压铸工的正确操作及压铸工艺参数的合理调节都直接决定了模具的命运。
1) 模具上压铸机后的调节。很多模具的损坏出现在模具上压铸机的时候操作不当,有的压铸企业对压铸工培训不足,忽视上模具过程中的正确操作,压板松紧不一、拉杆不平、随意操作手动按钮、开档调节不合适等都会导致模具受力不均衡、变形,或型芯及顶出机构顶断/弯等。
2) 模具产前预热。很多企业不注重模具产前预热,通常采用金属液慢压射预热模具,这种方式对模具损伤非常大,冷模具突然遇到温度非常高的金属液,导致模具成形表面龟裂纹的出现,直接影响产品的外观质量,如果采用的模具材料不是进口的,龟裂纹会扩散比较快,那就比较麻烦了。一般的模具可以用喷灯,液化气,天燃气预热;条件好及模具结构复杂的可用模温机。
3) 模具冷却水的使用。绝大多数模具都设有冷却水,整体冷却加点冷却,模具冷却水在正确使用的情况下不仅延长模具的使用寿命,而且提高生产效率。在实际生产中有的压铸工图省事、嫌麻烦,就直接不用冷却水,这样导致模温太高,脱模剂被迫多喷以降低模温,强冷热交替,使模具成型部分出现早期龟裂,给后序铸件表面处理带来困难,尤其是外观质量要求高的。另外,模温太高,产品容易变形、粘模拉伤、内部组织疏松等加剧。
4) 模具分型面的清理。模具分型面“跑水”在压铸过程中是比较常见的,也是比较令人头疼的,对模具配合间隙的掌握,配合部分的修配,这对模具制作师傅的技能要求比较高,在模具二三十万模具的压铸生产中,模具分型面及滑块配合部位难免会有飞皮毛刺、残渣屑、污垢的产生,操作工应该特别关注并清理这些部位,配备锉刀、刀等工具。一旦有了飞边没有及时清除,模具分型面很容易压塌,造成在生产过程中“跑水”,一旦造成这种后果,不管有多么好的模修专家,完全修复的可能性是很小的,不是他们没有本事。出现模具跑水所造成的后果,不但增加了压铸成本,白白的浪费掉铝液,产品质量也不稳定,特别是内部质量难保证,而且增加了工艺参数确定的难度,合格率会下降很多,另从安全考虑,也会增加了出现工伤的几率。要让员工养成一个良好的习惯,关注及清理分型面。
3 模具下场后的维护
1) 压铸中出现问题的修复。在压铸中出现的所有问题,由于要考虑生产效率及任务完成的周期等方方面面的影响,有时生产中出现的模具问题并不能得到及时而彻底的解决,如模具局部龟裂、小型芯断掉等。这些问题就需要模具下场后来解决,这时一般会有有更多的修模时间及手段,这就需要模修根据现场工艺及机加等多方反映存在的问题对模具进行逐一修复。#p#分页标题#e#
2)模具分型面的清理。前面说了压铸过程中操作者需要对分型面的飞边等进行清理,保持分型面的清洁,但对于压铸操作者来说,因为模具上在压铸机上,不可能得到彻底的清理。那么在模具下场后,应该有模修来对模具分型面、滑块配合面做一彻底清理,不仅清楚分型面飞边、铝屑,还需对残留的脱模剂、润滑油及污垢等进行清洗,确保模具无异物。若因模具配合不良导致模具“跑水”,还需对模具配合部分重新修配。
3)粘模部位的修复。模具粘铝,会造成产品拉伤,严重的会造成产品拉裂,这在压铸生产中也非常常见。因模具龟裂产生的粘模部位,根据情况进行更换或割镶等。因模具过高或喷涂不良等造成的粘模,多半进行抛光处理。
4)模具冷却水的疏通。冷却水道在使用过程中易因水垢变小甚至被堵塞,特别是插管的点冷却水道,从而直接影响模具冷却效果,故模具在压铸一万模次左右时,应采用钻花对冷却水道重新钻一次,对插管采用铁管的检查铁管是否生锈,及时更换。对本应该通的而因各种原因不通水的冷却水,及时修复。根据模具使用及产品出现的质量问题等需要对模具进行冷却,而设计中该部位没有考虑冷却水的部分,及时添加冷却水。
4 模具产前的准备工作
根据生产使用情况,对模具进行产前的准备验证工作,打开模具检查模具中所装的状态是否与所需状态一致,查看最后一次生产后的修模项次,加强对首件的走样、检测及解剖等工作,确保产品合格后进入批量生产。
5 定期组织模具专项会议
模具的使用、维护保养是很重要的了,但对模具的形式上的管理也不能不闻不问,应定期组织相关人员,如销售、生产、技术、压铸车间等参加,参与模具专项会议,由销售部介绍产品的市场装机情况,压铸车间介绍现有模具的使用情况,技术部介绍新模的制作及送样情况等,根据综合考虑,会议决定对模具进行补充投制新模,对不能继续使用的模具进行报废等。
模具占产品质量好坏的比重约 70%,由此可知,我们把模具从设计制作、使用、维护保养、管理等工作都做好后,再辅以需要的其它条件,就可以保证能够把产品做合格了。