文:杨宪章
摘要:对压铸模工作温度控制;模具加热和冷却装置的热量计算;冷却水流道的布置形
式、选择进行了论述,阐明了压铸模加热和冷却装置设计方法与优化。为提高模具的使用寿命和保证压铸件的成品率,模具设计人员应重视压铸模加热和冷却装置的设计。
压铸过程中,温度对填充过程的热状态,以及操作的效率等方面起着重要的作用。在压铸生产前压铸模应预热到一定温度,生产过程中要始终保持在稳定的温度范围内,这一温度范围就是压铸模的工作温度,通过加热和冷却装置控制。合理的模具工作温度可以提高压铸件的内部组织和表面质量,稳定压铸件的尺寸精度,提高压铸机生产效率,降低模具热应力,提高模具使用寿命。为了保证压铸生产的持续进行,在每一个压铸循环周期中,合金液传给模具的热量与模具自然散热及冷却水带走的热量应保持平衡。
1. 压铸模的工作温度
压铸模的工作温度可以按经验公式计算或由推荐的模具预热温度及工作温度由表1查得。
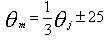
式中

——压铸模的工作温度(℃);

——金属液浇注温度(℃)。
2. 压铸模的预热
预热压铸模能防止因金属液激冷而流动性降低,使铸件成形困难或产生冷隔、裂纹等缺陷;减少金属液对低温压铸模的热作用,延长压铸模的使用寿命。压铸模常用的加热方法有以下几种。
(1)煤气、天然气加热 该加热方法方便,成本低,加热时间长。
(2)低熔点合金加热 在常温状态压铸模中直接浇入金属液,用金属液热量加热模具。
(3)电加热 电加热器有电阻加热器、电感应加热器和红外线加热器。其中最常用的是电热管加热,电加热清洁方便、操作安全,但成本较高。
电加热装置预热所需总功率可通过下式计算:
根据预热总功率选择电热棒(见图1)的型号和数量;设计电热棒的安装孔和测温孔位置,加热孔一般设置在动(定)模套板(也可以通过镶块)、支承板和定模座板上。布置时应避免与活动型芯或推杆发生干涉;在动、定模套板上可布置供安装热电偶的测温孔,以便控制模具工作温度温,尽量避免将电热棒和热电偶的连线布置在模具操作者的一侧。
(4)循环油加热 利用油泵将温度为150~200℃液压油对模具循环加热。在压铸开始时预热模具。工作中,循环油则对模具进行冷却。这种方法可以使模具在相对恒温范围内工作。但模具结构较复杂,需要一套密封较好且耐高温的循环油系统。
3. 压铸模的冷却
压铸模吸收金属液的热量若大于向周围散失的热量和冷却水带走的热量,其温度会不断升高,尤其压铸高熔点合金时,压铸模升温很快。压铸模温度过高,使压铸件因冷却缓慢而晶粒粗大,并且带来金属粘模;压铸件因顶出温度过高而变形,压铸模局部卡死或损坏,延长开模时间,降低生产率等问题。应采取冷却措施,使模具保持热平衡。
压铸模的冷却方式主要有风冷和水冷两种。
(1)风冷 用于散热量要求较小的模具,风力来自鼓风机或压缩空气,模具内不设冷却装置,结构简单。冷却速度慢,生产效率低,图2为型芯风冷的结构。
(2)水冷 在大批量生产大中型铸件或厚壁铸件时,为保持压铸模热平衡,多用冷却水冷却。在压铸模内设置冷却水流道,使热量随冷却水流动而迅速排出,保持压铸模获得热平衡。
4. 压铸模冷却热量的计算
在设置模具冷却水装置时,首先要考虑模具总体的热平衡,如何确定模具总体的热平衡,可以用传热学的公式进行计算。
(1) 模具吸收的热量
式中

——单位时间浇入模具的合金总质量

;

——合金液的比热容

;

——合金液浇注温度(℃);

——合开模时的温度(℃)。
(2)单位时间内冷却水从压铸模带走的热量
式中

——合金液质量

;

——模具工作温度(℃);

——合金的熔化潜热

;

——冷却水带走的总热量

。
(3)所需冷却水量 由于热量通过辐射和对流的方法带走的热量相对较少,约占Q吸的5%,而压铸模具通过传导传给压铸机而被压铸机冷却水带走的热量约占Q吸的40%,在压铸模冷却装置设计时可作为不变的因素来考虑,把剩余的热量都看作压铸模冷却水从冷却水流道带出,则单位时间内需要的冷却水量为:
(4)冷却水流量
式中

——水的密度

;
(5)冷却水管直径
式中

——冷却水流量

;

——临界雷诺系数,取2000~2300;

——水的运动黏度(m2/s)。
(6)冷却水道的总传热面积
式中

——常取0.95;

——热传导系数;

——冷却水的温差,取200℃;

——冷却时间

。
(7)冷却水道的总长s
式中

——冷却水道的总传热面积

;

——冷却水道直径

。
(8)冷却水道的个数
式中

——冷却水流道的总传热面积

;

——冷却水流道直径

;

——冷却水流道工作有效长度,(即在型腔的投影长度)。
5. 冷却水流道的设计
冷却水流道设计要注意:
(1)冷却水流道要布置在型腔内温度最高,热量比较集中的区域,通畅,无堵塞现象。
(2)模具镶拼结构上有冷却水流道通过时,要采取密封措施,防止泄漏。
(3)冷却水流道至型腔表面的距离应尽量相等,冷却水流道孔直径一般为8~16mm,其孔壁距离浇口或型腔壁面10~15mm。
(4)冷却水流道间的中心距,应为冷却流道直径的3~5倍。
(5)冷却水流道出口接头规格应统一,以便于连接管路,并尽可能设置在压铸模模具下方或操作者对面一侧,以便于操作。
(6)冷却水流道外连接冷却水管的尺寸一定要大于或等于压铸模内冷却水流道的直径。
(7)冷却水的流动方向与熔融金属流动的方向应一致,有利于散热和熔融金属充填型腔。
(8)为了能自动控制平衡点温度,对要求比较高的压铸模,型腔内应设置利用热电偶来控制冷却水管电磁阀开关的温度自动控制装置。
6. 冷却水流道的布置形式
为了更好地起到冷却作用,冷却水流道要合理地布置和选择形式,与铸件的大小、形状和压铸模的结构有关,设计时可参考图3、图4常用的几种型腔、型芯冷却水流道布置形式。分流锥冷却如图5所示,浇口套冷却如图6所示。
1. 定模套板 2. 定模板 3. 浇口套
4. 耐高温密封圈 5. 镶块
7. 结语
压铸模工作温度与压铸周期长短、冷却水流量有直接关系,一般来说,周期时间长,压铸模工作温度低;周期时间短,压铸模工作温度高。冷却水流量大,压铸模工作温度低;冷却水流量小,压铸模工作温度高。因此,在压铸模设计中要合理地计算,确定冷却装置的参数,选择冷却水流道的布置形式,使压铸模的热平衡达到理想状态,从而提高压铸件的成品率,延长压铸模的寿命。实际生产中,压铸模的加热冷却装置合理化设计应引起压铸模设计人员的重视。