文:上海乾通汽车附件有限公司 严炎祥
摘要 阐述了机床关系式P=Pj-K1Q2和模具关系式P=K1Q2的使用条件和方法,为使用计算机Excel软件制作电子表格及图像创造了条件;介绍了使用Excel软件建立P=K1Q2和P=Pj-K1Q2的电子表格及图像的方法。p-Q 图像是抛物线,p与Q 相对应,反映p-Q 函数的关系清晰明了。因此舍弃了传统的P-Q2直线图像,使用P-Q抛物线图像,称之为P-Q技术。还介绍了在图像上添加Vmax、Vmin和tmax、tmin 4条直线,组成工艺方框图,在P-Q图上模拟试模的方法;最后阐述了在试模或生产时,如何从机床显示屏上的时间-行程、时间-压力曲线图上寻找或求出实时的P与Q值,并把P、Q值作为边界条件,求出实时P=Pj-K1Q2机床关系式与实时P=K1Q2模具关系式的方法。
关键词 压铸;P-Q技术;Excel图表;模拟试模;正式生产
1 P-Q关系式与图像
1.1 P-Q关系式与图像
高速填充过程中,冲头在金属液中产生的填充压力P与流量Q 存在如下关系:
P =Pb(A0/A)-Pb(A0/A)(Q2/ Qmax2) (1)
设静态填充压力为Pj,且Pj=Pb(A0/A) (2)
设机床填充系数为K1,且K1 =Pb(A0/A)/ Qmax2=Pj/ Qmax2(3)
则式(1)可改写成P=Pj-K1Q2 (4)
式(4)称为机床P-Q 关系式。
金属液填充到型腔中,需要的填充压力P和流量Q,也存在如下关系:
以上式中,
Pb为蓄能器压力,Mpa;A为压射冲头面积,mm
2;A
0为压射液压缸活塞面积,mm
2;Qmax
2为料缸内最大空压射时金属液流量,L/s;Qmax= A V
0 /1000;V
0为最大空压射速度,m/s;

为金属液密度,kg/m
3(见表1);C为 流 量 系 数 (见 表 1);A
n为内浇口截 面 积,mm
2。
图1为机床线与模具线。如以 Q2为横坐标,P为纵坐标,机床P-Q2关系式相对应的是直线图像,叫做P-Q2机床线,见图1b;模具P-Q2关系式相对应的直线图像,叫做P-Q2模具线,见图1d。横坐标是Q2,数值大,间隔小,P与Q对应关系不清晰,不能真实反映P-Q的函数关系。
由于图像是直线,手工绘图方便。以前压铸专业技术资料中均采用P-Q2直线图像,并称为P-Q2技术。如以Q为横坐标,P为纵坐标,机床P-Q关系式相对应的是抛物线图像,叫做P-Q机床线,见图1a;模具P-Q关系式相对应的抛物线图像,叫做P-Q模具线,见图1c。横坐标是Q,数值小,间隔大,P与Q相对应,反映P-Q 的函数关系清晰明了。
虽然抛物线图像手工绘图不方便,但用了Excel软件后,得到很好的解决。笔者舍弃了传统P-Q2直线图像(见图1b、图1d),而使用了P-Q 抛物线图像,并称之为P-Q技术。
1.2 22000kN压铸机P-Q关系式
布勒22000kN压铸机压射液压缸直径为210mm,面积A0=34626mm2,蓄能器压力Pb=16 Mpa,压射冲头直径为130mm,面积A=13273mm2,最快空压射速度 V0=8m/s,则Qmax=A V0/1000=106.18L/s。机床静态填充压力 Pj=Pb(A0/A)=41.75。机床填充系数K1 =Pj/ Qmax2=0.003703。把Pj、K1数值代入式(4)得机床的P-Q关系式:
P =41.75-0.003703Q
2 (7)
1.3 气缸体压铸模P-Q关系式
气缸体压铸模浇注系统内浇口面积A
n=1500mm
2,压铸合金为铝合金。根据表1查得C 为0.5,

D_Dd__________áðϨϨ________________ D_Dd__________áðϨϨ________
P=0.002222Q
2 (8)
2 通过在P-Q图上模拟试模说明电子表格和图像的制作方法
模拟时,把机床线和模具线表示在同一张图中,其有一交点,观察交点位置可以知道模具和机床是否匹配,可作为评价机床能力和设定压铸工艺参数的依据(见图2)。
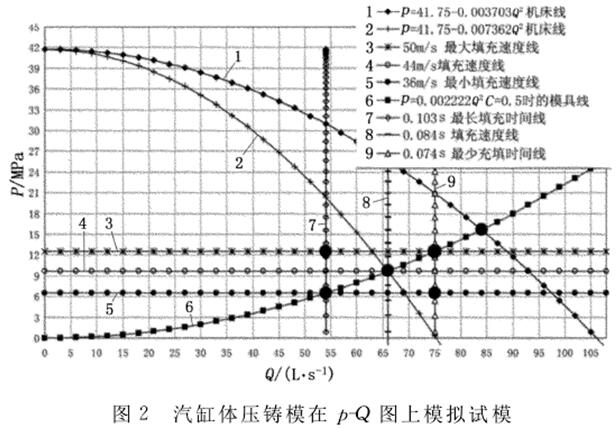
在该图上添加工艺规定的Vmax、Vmin和tmax、tmin4条直线,组成工艺方框图,观察方框图位置,可评判机床对模具的适应能力。
2.1 准备工作
2.1.1 汽缸体压铸模模拟
对象是汽缸体压铸模。P-Q关系式P=0.002222Q2 。模拟用机床是布勒公司 22000kN 压铸机,P-Q关系式是P =41.75-0.003703Q2 。
2.1.2 压铸工艺
内浇口面积An=1500mm2。流过内浇口的金属液体 积 V=5.56L。
料缸直径为130mm,面积为13273mm2ng=EN-US>5.56L。填充速度为44m/s,范围为36-50 m/s。填充时间为0.084s,范围为.0.074-0.103s。
2.2 创建一个工作簿(电子表格)
(1)启动 Excel,创建一个新工作簿,取名为“P-Q 函数与图像”。
(2)在“A”列输入 Q 值,单位是 L/s,从0开始,间隔3个单位,最大值应大于A V0/1000=106。其中,A是冲头面积 mm2;V0是空压射速度 m/s;“A”列数值是横坐标。
(3) 在“B”列输入关于机床的P =41.75-0.003703Q2关系式,计算机会计算出与“A”列的 Q 值相对应的全部P数值。“B”列数值是纵坐标。
(4)在“C”列输入模具的P=0.002222Q2关系式,计算机会计算出与“A”列的Q 值相对应的全部P数值。“C”列数值是纵坐标。
(5)在“D”列输入关于填充时间t与Q 关系式t=V/Q=5.56/Q,计算机会算出与“A”列的Q 值相对应的全部t值。
(6)在“D”列中找到工艺规定的最小填充时间tmin=0.074s和最大填充时间tmax=0.103s、填充时间t=0.084s数值。循着这3个数值所在行中 (有阴影处)找到“A”列对应的值 Qtmax=75L/s和 Qtmin=54L/s、Q=66L/s的数值。
(7)在“E”列的整列中输入Qtmax=75L/s同一个值。“E”列数值是横坐标。
(8)在“F”列的整列中输入Qtmin=54L/s同一个值。“F”列数值是横坐标。
(9)在“G”列的整列中输入 Q=66L/s同一个值。“G”列数值是横坐标。
(10)在“H”列中输入关于填充速度V与Q 关系式V=1000Q/An=1000Q/1500=Q/1.5,计算机会计算出与“A”列 的 Q 值 相 对 应 的 全 部V值。V的 单 位 是m/s。
(11)在“H”列中找到工艺规定的最小填充速度Vmin=36m/s和最大填充速度Vmax=50m/s、填充速度V=44m/s的数值。循着这3个数值所在行中(有阴影处)找到“C”列对应P Vmin=6.48和Pmax=12.5、P=9.68的值。
(12)在“I”列 的 整 列 中 输 入P Vmax=12.5 同 一 个值。“I”列数值是纵坐标。
(13)在“J”列 的 整 列 中 输 入P Vmin=6.48 同 一 个值。“J”列数值是纵坐标。
(14)在“K”列的整列中输入P=9.68同一个值。“K”列数值是纵坐标。通过上述步骤作出了P与Q、V与Q、t与Q 一一对应的电子表格,见表2(只列出表头和部分数值)。
2.3 在工作簿中插入平滑线散点图(函数的图像)
(1)打开 Excel主菜单“插入”的下拉式菜单,选取图表 XY 散点图中的平滑线散点图。
(2)在平滑线散点图中作关于机床的P =41.75-0.003703Q2关系式的曲线 在表2中选取“A”列的 Q值为横坐标,选取“B”列的P值为纵坐标,计算机会自动生成P =41.75-0.003703Q2曲线,这是机床(最大能力)线。
(3)在图2中添作关于模具的P=0.002222Q2关系式的曲线 在表2中选取“A”列的Q 值为横坐标,选取“C”列的P值为纵坐标,计算机会自动生成P=0.002222Q2曲线,这是模具线。
(4)在图2中再作最小填充时间tmin线,在表2中选取“E”列的Qtmax=75
的值为横坐标,选取“B”列的p值为纵坐标,计算机会自动生成最小填充时间tmin
线。其是一条与纵轴平行直线。
(5)在图2中再添加最大填充时间线tmax,在表2中选取“F”列的Qtmim=54的值为横坐标,选取“B”列的p值为纵坐标,计算机会自动生成最大填充时间tmax线。
其是一条与纵轴平行直线。
(6)在图2中再添加填充时间线t,在表2中选取“G”列的Q=66的值为横坐标,选取“B”列的P值为纵坐标,计算机会自动生成填充时间t线。其是一条与纵轴平行直线。
(7)在图2表中再作最大填充速度Vmax线,在表2中选取“A”列Q 值为横坐标,
选取“I”列P Vmax=12.5值为纵坐标,计算机会自动生成最大填充速度Vmax线。其是一条与横轴平行直线。
(8)在图2表中再作最小填充速度Vmin线,在表2中选取“A”列的Q 值为横坐标,
选取“J”列P Vmin=6.48值为纵坐标,计算机会自动生成最小填充速度Vmin
线。其是一条与横轴平行直线。
(9)在图2表中再作填充速度v 线,在表2中选取“A”列的Q 值为横坐标,选取“K”
列p=9.68值为纵坐标,计算机会自动生成填充速度V线。其是一条与横轴平行直线。
通过上述步骤,最终得到机床能力线、模具线和工艺窗口,见图2。
2.4 汽缸体压铸模在P-Q图上模拟试模
(1) 在P-Q图上评判机床能力。观察图2,P-Q 模具线和机床最大能力线相交于一点,该点表示压铸机最大能量下的压铸模所能获得的最大填充压力(15.65MPa)和最大填充流量(83.94L/s),也可以通过解式(7)、式(8)的联立方程得到。该点在工艺方框之外的右上方,且有较大距离,说明机床能力大于压铸工艺要求的能力。工艺窗口内的模具线长度已是最长形态,说明压铸工艺参数调整余度大,调整时有较高的灵活性,压铸系统柔性度好。
(2) 模拟试模时机床P-Q 关系式。
由表2查得填充速度Vn=44m/s时流量 Q=66L/s和填充压力P=9.68Mpa,坐标(66,9.68)可看作模具线与机床工作线交点,于是求得机床关系式中 的K1 =(Pj-P) /Q2=0.007362,则填充速度Vn=44m/s时模拟机床P-Q关系式为P=41.75-0.007362Q2,作此式电子表格 (见表2中的“L”列),再作图象,得到横穿工艺窗口的模拟机床工作线(见图2)。
3 汽缸体压铸模在22000kN 压铸机上正式试模
在模拟时,模具关系式的K值中的流量系数C是预先设定的。K=

D_Dd_____受制于模具温度、浇注温度、内浇口位置形状等众多因素,从而使实际试模时的 K值与预先设定的K值有差异。所以在实际试模时必须对填充系数 K、流量系数C进行验证,并在实践中加以修正。确认P-Q机床线是符合实际工况的,如有怀疑或要改变工作压力,需重新测定冲头的空压射速度并绘制新的P-Q机床能力线;冲头与料缸的配合和润滑必须良好,否则会使P-Q机床线失去正确性;在慢压射阶段时,必须把料缸中的空气全部排净,保持料缸内金属液的连续性,否则在填充过程中不会遵循流体力学的伯努利定律。当液压工作压力、冲头直径固定时,机床静态填充压力Pj是固定的;但机床填充系数K1是与调速阀的开度密切相关的。
(1)求机床线和模具线的公共交点。
按工艺,在机床操作屏幕上把压射冲头快压射速度设为Vz=4.97m/s(填充速度44m/s)。控制系统按设定要求能自动连续控制电液伺服调速阀的开度,实时控制冲头速度固定在4.97m/s这一点上。
压铸机每次工作循环后都会在显示屏上实时显示时间-行程、时间-压力曲线(见图3)。
在图上观察到填充压力 P=12.2 Mpa(显然不同于模拟的P-Q图上的P=9.68Mpa)。此时流量 Q=A0 Vz/1000=66L/s。坐标点(66,12.2)是机床线和模具线的公共交点。
(2)求模具填充系数 K、模具P-Q关系式和流量系数C。由坐标点(66,12.2)和式 P=KQ2可计算得到K=12.2/662=0.002801,此值大于模拟试模时的 K值 为 0.002222。 实时模具
P=KQ
2 关系式为 K=12.2/66
2=0.002801。 由 K=

/(2C
2A
n2)求 得 C = [

/(2KA
n2)]
1/2=0.4454,此值小于原来模拟试模时设定的C 值0.5。
(3)求机床静态填充压力 Pj,机床填充系数 K1和机床实时P-Q关系式。机床静态填充压力Pj=Pb(A0/A)=41.75;机床填充系数K1:把P=12.2,Q=66,Pj=41.75 代 入P=Pj-K1Q2,经计算,K1=0.006784。此值小于原来模拟值0.007362。说明在相同的流量下需要较大的填充压力。机床实时P-Q关系式为P=41.75-0.006784Q2。
(4)先 作P=0.002801Q
2和P=41.75-0.006784Q
2的电子表格(见表3),再作图像,并在图像上添加工艺方框图,见图4(过程略)。
在模拟试模的图2中,工艺方框图右上角远离机床最大能力线,说明机床能力富裕。在 正式试模的图 4中,由于模具线上挠,以模具线中的P作为变量的速度线也随之变动,工艺窗口也随之向右上方移动,工艺方框图右上角靠近机床能力线,说明机床能力富度减少,压铸工艺参数调整余度也变小 。如果修改模具浇注系统或调整冲头速度,模具线和机床线必然会有一个新的交点,须重新建立新的关系式和 Excel电子表格、图像及工艺窗口,重新审视工艺窗口在图像上位置、评判机床能力和压铸系统柔性度。当模具线包裹在窗口中的长度太小或工艺窗口的右上角越出了机床最大能力线,而铸件质量又不好时,则有必要修改模具或更换机床。
4结论
(1)模具P-Q关系式为
P= KQ
2,其 中

/(2C
2A
n2);机 床P-Q关 系 式 为
P=
Pj-K
1Q
2,其 中
Pj=
Pb(A
0/A),
K1 =
Pb(A
0/A)/ Qmax
2=
Pj/ Qmax
2。为使用 Excel软件制作
P=KQ
2和
P=
Pj-K
1Q
2的电子表格和图表创造了条件。
(2)使用 Excel软件建立P=KQ2和P=Pj-K1Q2的电子表格及图像的方法,在图上能方便地添加vmax、vmim和tmax、tmim4条直线,组成所谓的最佳工艺方案,实现通过P-Q图技术的模拟试模方法,从而为浇注系统设计进行事前评定,为机床能力与压铸模具的匹配提供了依据。
(3)每次冲头速度调整后,在压铸机操作屏上显示的时间-行程、时间-压力曲线图上寻找或计算出实际的机床-模具P-Q线新工作点(交点),以这一工作点为边界条件,求出机床 -模具P-Q实时关系式、电子表格和图像,重新审视 “工艺窗口”位置和压铸系统的 “柔 性度”。以此确定工艺调整的有效性。