文:广州市鑫煜铸造设备材料制造有限公司 修毓平
湖南鑫煜金属材料有限公司
一.对再生铝的再认识
废杂铝再生是21世纪铝工业生产发展中的一个热点。它是随着铝工业的诞生逐步壮大起来的。西方国家在上世纪30年代中期开始形成一个独立的行业,中国则是在上世纪70年代初期开始受到关注。再生铝本身是自然资源的再利用,具有很强的生命力。再生铝在铝生产总量中的比例越来越高,如日本达99.5%,压铸行业用再生铝已是一种必然的趋势。与生产原铝相比,用废铝料生产再生铝,可节约95%的能源,二氧化碳排放量比用水电生产原铝减少91%,比用燃油发电生产原铝减少97%以上。每生产1吨再生铝节约用水10.5吨、少排放二氧化碳0.8吨、少排放二氧化硫等有害气体0.06吨。在产量相同条件下,生产再生铝的建厂投资仅仅为生产原生铝的十分之一。显然具有重大节能、环保和经济优势。
由于再生铝的原材料主要是废杂铝料,废杂铝中有废铝铸件(以Al-Si合金为主)、废铝锻件(Al-Mg-Mn、Al-Cu-Mn等合金)、型材(Al-Mn、Al-Mg等合金)废电缆线(以纯铝为主)等各种各样废料,有时甚至混杂入一些非铝合金的废零件(如Zn、Pb合金等),这就给再生铝的配制带来了很多隐患。如何把多种成分复杂的废铝料配制成成分与性能均合格的再生铝锭,既是再生铝生产的核心问题,也是作为使用再生铝材料的压铸厂家必需关注的问题。事实证明,对再生铝的了解越深入,我们对再生铝的使用和控制就越科学。
1) 废铝料的来源
国外进口的混杂废铝料成分复杂,除废杂铝外,还含有一定数量的废钢铁、废铅、废锌等金属和废橡胶、废木料、废塑料、石子等,有时部分废铝和废钢铁机械结合在一起。还有一些是焚烧后的含铝碎铝料,档次较低,主要是各种报废家用电器等的粉碎物,分选出一部分废钢后再经焚烧形成的物料。这类含铝废料一般铝含量在40%~60%左右,其余主要是垃圾(砖块石块)、废钢铁、极少量的铜(铜线)等有色金属。铝的块度一般在10厘米以下,在焚烧的过程中,一些铝和熔点低的物质如锌、铅、锡等都熔化,与其他物料形成表面玻璃状的物料,难以辨别和分选。
国内回收的废杂铝大多较纯净,即常说的废熟铝,废生铝和废合金铝。废生铝主要是废铸造铝和废合金铝。多以废机器零件(如废汽车零件、废模具、废铸铝锅盆、内燃机活塞等)。废熟铝一般指铝含量在99%以上的废铝(如废电缆、废家用餐具、水壶等)。废合金铝如废飞机铝、铝框架等。
生产企业产生的废铝料一般称为新废料,主要包括铝合金在生产及加工过程中产生的浇冒口,边角料、废次材、铝屑末及废品等。这些新废料除粘有油污及屑末外,都是档次较高的废铝料,如果在企业产生废料时能清晰的分类保存,利用价值极高。熔炼铝过程中必然产生浮渣,即常说的铝灰。废杂铝的成分复杂,杂质越多,表面污染越严重,铝灰就越多。铝灰的含铝量与所选用的覆盖剂和熔炼技术有关,一般含铝量在10%-20%。
总之,废杂铝的组成相对比较复杂,含有较多外来杂质,包括各种有机质如塑料类物质、水分等,熔炼之前如不清理干净,会造成合金熔体严重吸气,在随后的凝固过程中产生气孔、疏松等缺陷。此外一些非铝金属的混入,导致材料成分不合格,性能恶化。各种非金属矿物的混入造成的非金属夹杂,也会使材料的性能品质下降。因此,再生铝生产流程第一重要环节就是废杂铝的预处理,以尽可能地净化原料,把不利于再生铝质量的因素减少到最低程度。只有这样,压铸厂才能用上放心铝锭。
2) 废杂铝的预处理
废杂铝预处理的目的一是去除废杂铝中夹杂的其他金属和杂质,二是把废杂铝按其成分分类,使其中的合金成分得到最大程度的利用。三是将废杂铝表面的油污、氧化物及涂料等处理掉。预处理最终的结果是将废铝处理成符合入炉条件的炉料,四是使含铝废料中的铝(含氧化铝)得到最经济最合理的利用。
目前发达国家已形成完善的废杂铝收集、管理、分检系统,适应不断扩大的市场需求,
实现了废杂铝分选的机械化和自动化,最大限度地去除金属杂质和非金属杂质,并按主合金成分把废铝分成几大类,如合金铝,铝镁合金、铝铜合金、铝锌合金、铝硅合金等。这样可以减轻熔炼过程中的除杂技术和调整成分的难度,并可综合利用废铝中的合金成分,尤其是含锌,铜,镁高的废铝,都要单独存放,可作为熔炼铝合金调整成分的中间合金原料。目前先进的废杂铝预处理技术主要有:A。风选法分离废纸、废塑料和尘土。B。采用磁选设备分选出废钢等磁性废料C。以水为介质的浮选法分选轻质杂质D。用抛物选矿法从废铝中分选铜等重有色金属E。溶剂浸泡废铝或回转窑焙烧法处理废铝表面涂层。F。对报废汽车等大型设备采用机械拆解的高效率流水线。由于采用先进技术对废铝进行有效的分选,在资源的最佳配置上获取了利润的最大化。
我国对废杂铝的回收预处理在观念及认识程度上,与发达国家相比,差距比较明显。再生铝企业数量虽然庞大,但生产高质量再生铝的厂家不多,还有许多作坊式的家庭企业;采用混炼的方式生产,技术水平低,依靠手工分拣,预处理水平可想而知,能源与资源浪费大;环境污染严重;回收与最终销售价格扭曲,处于粗放经营管理的水平上。如对表面有涂层或油污的废料一般不作任何预处理就直接熔炼,使部分铝氧化,并增加了铝中的杂质和气泡,其后患无穷。因此压铸厂家在选择再生铝料时,不光要比价格,还需要对供应商知己知彼,既看“前店”,也要看“后厂”。
3)废杂铝的熔炼
废杂铝合金熔炼的基本任务是获得符合规定成分(包括主要组元或杂质元素含量)和性能要求的铝合金液。并在熔炼过程中采取相应的措施控制气体及氧化夹杂物的含量,保证铸锭得到适当的晶粒细化的组织。铝合金熔炼过程一般如下:
装炉→熔化(同时按需加铜、锌、硅等)→扒渣→取样→调整成分→搅拌→精炼→扒渣→铸锭。
由于铝元素的特性,铝合金有强烈的产生气孔的倾向,同时也极易产生氧化夹杂。因此,防止和去除气体和氧化夹杂就成为铝合金熔炼过程中最突出的问题。发达国家在生产中不断推出新的技术创新举措,如低成本的连续熔炼和处理工艺,使低品位废杂铝升级,用废杂铝已能大量制造供压铸、轧制及作母合金用的再生铝锭。在铝熔炼技术上,开发了高效、节能并且符合环境保护要求的侧井反射炉和双室反射炉、用于铝屑回收的多室熔炼炉;处理铝渣的倾斜式回转炉;类似LARS技术(Liquid Aluminum Refining System—是目前国际最先进铝液精炼系统之一)的除杂除气装置。推广并应用了一些高效的精炼净化技术,现代化自动控制的铸造结晶技术,高效燃烧技术和根据铝合金的成分要求电脑自动控制的物料配比系统软硬件。有的大型汽车公司还计划和铝业公司建立闭环铝废料回收再生系统。我国曾相继引进SNIF,MINT,ALPUR,RDU等先进铝熔体在线净化技术,并自主研制了DDF等技术,但除氢水平仍有较大差距。目前我们已是世界第一再生铝生产大国,面对再生铝行业的快速发展和诸多不成熟,从现实应用的角度,我们更应重视再生铝的产品质量问题;品种结构问题;质量检验问题;市场无序竞争问题等,压铸工作者对进一步提高再生铝质量充满着期待。
二、 再生铝的质量管理
由于压铸业的利润率越来越低,一些压铸厂的管理者囿于成本的制约,加之对劣质再生铝危害性认识不足,缺乏检测手段,在再生铝锭质量和价格的天平上偏向了后者,导致出现一系列压铸质量问题,甚至造成直接经济损失。因此,严格再生铝锭的质量管理已被越来越多的有识之士所重视。
1) 再生铝质量分析
A. 再生铝原料来源复杂,成分控制难是保证质量的关键问题。回收废铝料中有20余
种元素(Cu,Mg,Mn,Si,Ag,Ti,Be,Zn,Sn,Ni,Cr,Pb,Bi,V,Zr,Co,O)。对某些牌号的合金是重要添加元素,对另一些牌号合金则是有害物质。因此再生铝一般要降级使用。
B. 非金属夹杂是导致废品的最主要缺陷。由此原因报废的再生铝锭达废品总量的
10-25%。这些夹渣来源于高温熔体表面氧化膜破裂形成的碎片和炉渣,废料本身含大量氧化物及未处理干净的杂物等随铝液进入铸锭,来自一次合金处理的钛,硼聚集夹渣物,来自炉衬的耐火尖晶石颗粒,多元化合沉积物Al-Fe-Mn-Cu等。来自油和水的氢化物杂质,阳极化和表面涂层造成的夹杂物等。其中以氧化物夹渣最普遍。氧化夹渣在断口上呈暗褐色或灰色和金黄色等斑状。一般要求铸锭低倍试片不得多于两点夹渣,且单个面积小于0.5mm2。
C. 在熔炼和转注时因湍流,翻滚,飞溅引起的氧化膜。它很薄,与基体金属结合紧密,
在低倍组织观察中不易被发现。
D.用废料重熔会带入较多气体。有资料报导:从重量15KG的铝锭表面析出的水蒸气
和氢气有373cm3,而15KG废铝板(2mm厚)表面析出量达6000cm3,而且,铝合金表面的氧化膜厚度室温下约为2.5-5.0µm;潮湿环境下,成复式氧化膜,内层为氧化物,外层含羟基化合物。在熔铝过程中,这些氧化夹杂物是部分气体的载体,残存于铝液中。对于长时间在潮湿环境中的铝废料,其表面有较厚一层Al(OH)3,内含的化合态水加热到300—400ºC也不能除掉。在400ºC以上才开始分解为γ-Al2O3和 H2O。这样的炉料即使预热,熔化后的再生铝锭中氢含量也大为增加。大约是原铝的10倍。
E. 再生铝锭中出现气孔,起皮,起层,表面夹杂,裂纹,力学性能不合格的现象,主
要源于铝锭中的偏析,热脆,气体,氧化物夹杂,缩松,裂纹,晶粒组织不良及化学成分不合规范要求等因素。
2) 再生铝的质量检验
目前对再生铝的检验可分为化学成分检验,金相组织检验,表面检验和性能检验。金属中含气量分析主要以液态金属测氢为主。
A.化学成分检验:限定在相应牌号的标准成分范围内。此为外限标准或工业标准。由于大量废料回炉势必增加再生铝锭中的杂质成分,为了确保外限标准所必需的限度,根据工厂的具体情况应自行制定内限标准,并按此来验收。早期用化学分析,其结果精确,但操作繁杂,目前多用于校验其它分析方法。现在大都采用光谱分析,其灵敏度高,速度快,选择性好,成为检验的主流。
B.组织检验:分为宏观和微观检验。
宏观检验是借助肉眼或低倍放大镜(小于30倍)观察和判断再生铝锭内部是否有裂纹,夹杂,气孔,成分偏析及不良晶粒组织等缺陷。由于铝锭内部缺陷多集中在近表层,或表皮上,因此特别要对铝锭的表面从形状,缩孔,气孔,氧化物夹杂和表面裂纹等方面检验。一般不允许有拉裂,气泡,腐蚀斑点,缩孔,高出表面的金属瘤等。
微观组织检验是利用光学金相显微镜或电子显微镜等从毫米,微米乃至纳米尺度来观察,鉴别和分析各种相的形貌,晶体结构和化学组成等。其检验标准在参考国家标准的同时,应结合自身对压铸件的要求调整。
C.力学性能检验。铝合金力学性能包括强度,塑性,韧度和硬度,它们与化学成分,
组织结构有密切关系,是压铸前必须确认的。用材料实验机和各种标准的静,动态硬度测试仪可以完成对力学性能的检验。
D.断口检验。常用冷、热酸、碱浸蚀后对再生铝锭的断口观察。常有缺陷为裂纹、夹渣、气孔、疏松、白斑等。也可以根据断口形状用肉眼初步判断质量。质量好的再生铝锭晶粒较细,断口呈白色丝绒状,没有硅晶粒亮点。质量差的铝锭则晶粒粗大,断口呈灰暗色或蓝灰色,并有发亮光的硅晶粒可见。
三.再生铝熔炼工艺特点分析
由于再生铝锭有许多先天不足的缺陷,加重了压铸厂重熔铝锭时的冶金负担。因此必
须在传统熔炼工艺的基础上,做必要的调整和给予更多的关注。
1)熔炼温度控制要合理
一般压铸铝合金熔化温度应控制在比浇铸温度高出20-50ºC或750ºC以下。若再提高10-40ºC,氧化物含量会增加2-3%,这无疑使本来氧化物含量就高的再生铝液雪上加霜。若提高80ºC,铝液中的氧化物含量增加20%;提高120ºC ,则增加200%。当温度达到800-900ºC时,铝液表面密度为3.5g/cm3的γ-Al2O3向密度4.0g/cm3的α-Al2O3转变,使表面体积发生约13%的收缩,原来连续致密的氧化膜收缩出现龟裂,使铝液向深层氧化。同时大量吸气,造成晶粒粗大。此外,铝的氧化物对于氢处于“活性状态”,容易吸附铝液中的氢气,构成(Al2O3)XH型络合物,使铝液越来越不干净。还要注意大熔池中铝液沿高度方向存在明显的温差。一般操作条件下每10mm厚度的温差为1.5—2.0ºC,其影响铝液的质量稳定。
2)铝锭入炉前要干燥
铝锭入炉前要干燥,其作业并不复杂,但是若不了解这样做的深层次原因,往往不被重视,亦可能不被坚持。其实它对于再生铝液的净化和去气非常重要。被水分侵蚀的炉料熔炼时污染金属最严重,有必要对此做较详细的讨论。
研究表明,铝合金液溶解的气体中氢气占85%以上。而氢含量与水蒸汽直接相关。氢原子半径0.046nm,故易溶于铝液中。氮原子半径0.070nm,结构复杂的多元化合气体如CO2,CO,CH4等原子半径更大,因此比氢难溶。气体一般以三种形态存在于铝合金液中:
A。以分子态吸附在金属裂纹表面和显微疏松处,或形成气泡。100克铝液中含氢超过0.61cm3就会形成气孔,即以分子态残留。
B。在铝合金晶体点阵间隙处形成间隙式固溶体。
C。以氧化物,氮化物和氢化物等金属化合物弥散于晶粒内或晶界上。
氢在铝液中的溶解度符合Sievert定律:
S=mPH2O1/2e-Es/2RT
其中:S---氢在铝液中的溶解度cm3/(100gAl); m---常数; T--- 铝液温度K
R---气体常数; PH2O----铝液面上水蒸气分压Pa; Es---氢的溶解热J/mol
氢在铝液中溶解是吸热反应,Es>0, 故PH2O越大,T越高,则氢的溶解度就越大。
再生铝的表面和内部的氧化铝含量较原铝高。在3万倍电镜下γ-Al2O3膜内层致密,外
表疏松,有大量5-10nm小孔,很易吸附水气,以Al2O3•nH2O形态存在。如下图所示
在一般熔炼温度下常含1-2%的水。900ºC仍吸附有0.34%的水。温度高于900ºC时,转变为不密实的α-Al2O3 才能完全脱水。说明在通常熔炼温度下,铝熔体表面Al2O3膜层中,总是吸附一定量水。若入炉前未干燥,在250ºC 以下铝锭表面会有如下反应:
2Al + 6H2O=2Al(OH)3(系白色粉末)+3H2
温度高于400ºC时,
2Al(OH)3=Al2O3 +3H2O
使更多的水气吸附在γ-Al2O3膜上并带入铝液。熔炼时这些γ-Al2O3膜一旦搅入铝液中,
则吸附在膜外表面的水与铝液剧烈化学反应,生成氧化铝和氢。
2Al + 3H2O = Al2O3 + 6[H]
△GT = -78003 – 5.73TlogT + 32.95T
新生的氢[H]很易被铝吸收并向铝液内部扩散。在727ºC,反应自由能∆G=-785KJ/mol, K=4.64×1013, 反应向右进行,平衡常数很大。说明在铝液表面即使有微量水分,也会产生氧化物夹杂和单质的氢。当铝液凝固时,氢在铝液中的溶解度急剧下降,660ºC时,100克铝液中氢的溶解度0.68cm3, 而固态100克中为0.036cm3,溶解度下降18倍。来不及析出的氢最终导致压铸件气孔,针孔,渗漏等一系列问题发生。
使熔体氢含量增加最显著的元素是镁。镁有很高的吸氢能力,在658ºC,氢在镁中溶解度达100克镁60.1cm3, 比氢在铝中0.65cm3高92.5倍。同时,MgO与 Mg的体积比小于1,在熔体表面形成疏松氧化膜,使吸氢速度增加。因此要注意再生铝中镁含量的控制。
3)打渣精炼处理要得当
利用熔剂进行打渣精炼处理,是传统熔炼必不可少的工艺环节。其效果取决于熔剂的质量,处理温度,处理方法和加入量。熔剂的物理、化学性能(熔点、密度、粘度、挥发性、吸湿性以及与氧化物的界面作用等)对精炼效果起决定性作用。熔剂的普适作用大致有四个方面:
A。改变铝熔体对氧化物的润湿性,使氧化物(主要是氧化铝)易于与铝熔体分离,其大部分进入熔剂中而减少了熔体中的氧化物含量。
B。改变熔体表面氧化膜的状态。使熔体表面上那层坚固致密的氧化膜破碎成为细小颗粒,因而有利于熔体中的氢从氧化膜层的颗粒空隙中钻出,进入大气中。
C。熔剂层的存在能隔绝大气中水蒸气与铝熔体的接触,使氢难以进入铝熔体中,同时能防止熔体氧化烧损。
D。吸附铝熔体中的氧化物,使熔体得以净化。
总之,熔剂精炼主要是通过与熔体中的氧化膜及非金属夹杂物发生吸附,溶解和化学作用来实现的。
由于再生铝合金的净化处理负担较重,一般都要适当提高熔剂用量。其它工艺措施如除气精炼方法可以循旧,但最重要的是对熔剂品质的考量。当前国内生产铝熔剂的单位很多,良莠不齐,鱼龙混杂,加之使用厂家无系统验收及检验标准,使一些虽价廉但质次甚至无用或有害的产品进入熔炉。一旦铝液出问题,或产品出现与熔剂质量有关的黄斑,出汗,气孔等缺陷,往往无从分析是再生铝料质量的问题,还是熔剂问题,或是工艺问题,因此常出现互相推诿,不利于正确处理。因此严格把好熔剂质量关,使用有信誉的品牌产品至关重要。
从冶金物理化学的角度,我们希望熔剂应具备以下特点:
A.不和铝液发生化学反应或相互溶解。炉渣中只夹带少量铝。
B.熔剂熔点低于铝液温度,且流动性好,能在铝液表面形成连续覆盖层。
C.能有效融合氧化物,或生成易挥发的气体,在铝液内产生微小气泡,依靠气泡上升过程中与固态杂质点的惯性碰撞或与周围杂质点相接触并捕捉之,从而有效俘获铝液中的微米级夹杂物。
D.与铝液密度有明显差别,易于上浮和分离。
E.熔融状态下的熔剂粘度要小,与铝液的界面张力要大,防止形成熔剂夹杂混入铝液中。
F.控制熔剂中结晶水含量,并保持物理干燥,防止熔剂中水气对铝液的二次污染。
H.不应含有或产生有害杂质及气体,要有利于保护熔炉和机械设备,有利于环保。
4)稀土型熔剂对提高再生铝熔炼净化水平影响深远
选用含稀土的除渣精炼熔剂,加入铝液后,除细化作用外,利用稀土与氢有较强亲和力形成稀土氢化物的特点,可以锁住固溶体中的氢。在铝熔炼温度范围内,(680--750︒C)稀土与氢化合物生成稳定的氢化物:
[RE]+2[H]= [REH2]
此反应系放热反应,随温度下降,该氢化物越加稳定,从而达到固氢的目的。若采取稀土—惰性气体联合去气,其效果更好。
稀土对氧的亲和力大于铝和氧的亲和力,故[RE]能从氧化夹杂中还原出铝,减少了氧化铝夹杂,消弱了氧化夹杂的吸氢作用。
2RE + Al2O3 = 2Al + RE2O3
研究发现,稀土熔剂在铝液净化中产生两层保护膜:内层:由条状纤维编织成致密保护网络,吸附夹杂及熔剂与夹杂的反应生成物质。外层:由结晶态物质构成,起隔绝空气保护熔体的作用。
我公司在获得两项稀土发明专利(ZL 2013 1 0228423.4 ZL 2016 1 0184371.9)的基础上,推出的含稀土绿色环保型铝、锌合金用除渣精炼系列熔剂,经实验和生产验证,其显著特点是
1) 操作基本上无烟尘、无毒、无气味,与环境友好。
2) 铝损耗率低,炉渣呈松散粉状干性,容易和铝液分离,渣中很少铝合金残留。熔铝损耗小,
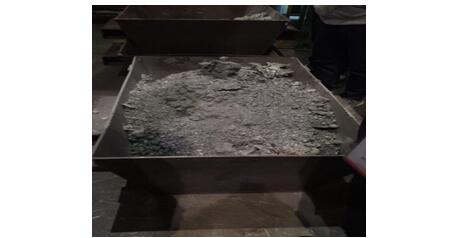
3).净化效率高。
对氧化铝等熔渣有高度浸润能力,有助于夹渣的上浮,能有效清除铝液内的氧化物夹渣,同时显著降低铝液含气量。工厂实验表明用氮气吸送混吹,净化处理时间:约15min-30min,其除氢率可达85%左右。
中信戴卡股份有限公司工程技术研究院材料研究所2015年10月关于该专利产品的试验报告中提供的重要结果如下:
1) 该熔剂在 700-760℃温度范围均可使用。
2) 稀土熔剂比例可在 0.2wt%-0.4wt%之间调节使用。
3) 使用过程中快速释放完少量刺激性气味的气体,烟雾几乎不可见。
4) 使用熔剂后,形成的渣为松散的灰白色渣,且渣铝分离效果良好。
5) K 模断口无可见夹杂物。
6) 稀土熔剂有除钠作用,对二次枝晶间距无影响。
该所研发车间试用情况报告进一步指出:
7) 稀土清渣剂如考虑 K 模夹渣 和铝回收率,添加比例为 0.25%效果最佳。
8) 与目前使用的清渣剂相比,添加等量的稀土清渣剂,对 Mg 的烧损率更低。
9) 密度当量结果表明,稀土清渣剂对除气有促进作用。
10) 添加稀土清渣剂对车轮轮缘的过程性能无明显影响。
两年多来,该产品在一些上市公司压铸企业、高新技术企业及知名压铸企业已正常批量使用,对于提升再生铝的净化处理水平、降低成本、改善作业环境、提高产品性能效果明显。
面对压铸结构件轻量化和功能化对材质越来越苛刻的要求,越来越多的有识之士从成功或失败的经验中,清醒地意识到,把好熔炼关,精工细作,严防“病从口入”对提升压铸技术水平是多么重要。中国是世界第一稀土资源大国,在稀土开发应用领域占据绝对优势,把稀土应用于提高铝合金的熔炼质量,既是创新,也是挑战,更是把优势转化为优质的一项实实在在的成果。稀土在熔炼净化技术方面应用的创新发展,无疑影响深远。