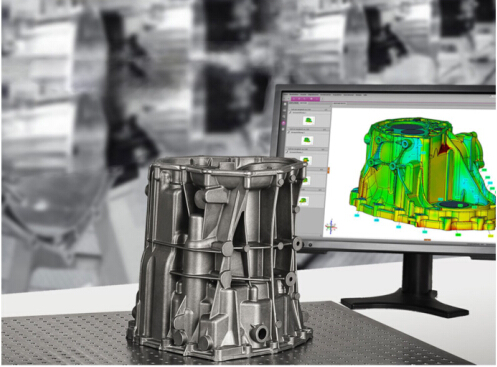
文:广州希鹏计算机科技有限公司
摘要
在批量生产中,生产周期是压铸工艺的关键参数。它不但直接影响生产率,也关乎铸件品质。长期以来,人们一直在寻找行之有效的方法优化这些工艺参数,但进展非常缓慢。本文以Cast-Designer的产品优化模块为例,介绍一种将数字模拟、专家库技术和数学优化高度复合的新的计算机自动优化技术。通过该技术,可以自动控制和优化模具的冷却系统与生产工艺参数,减少冷却等待时间,缩短生产周期,并获得均匀的模具温度。而均匀的模具温度分布,可以减少铸件的翘曲和变形;减少烧模、冷隔等生产缺陷,并有效地延长模具的使用寿命。
概述
模具开合模的生产周期(或循环周期)是高压铸造和金属型重力铸造在批量生产过程中必不可少的工艺参数。采用合适的生产周期,不仅能提高生产效率,而且有益于获得均匀的模具温度,在增加生产稳定性的同时,获得更高精度和更少变形量的产品。
然而,众所周知,在铸造热循环的不同阶段,涉及到许多复杂的物理量。在金属液充型过程中,金属液经过模具各部位的速度是变化的;热传导和对流在金属液与模具的接触中同时存在,液体金属热传导率的测定又非常复杂。此外,要把一个生产周期,清晰地细描述为不同的阶段,并赋予相应的物理特性,也并非一件简单的事情。
采用数值模拟,如Cast-Designer 的循环模温分析,能提供铸造生产过程中的稳态模温分布结果。该结果精确地描述了模具在完整的生产周期中的温度变化过程,包括充型与凝固过程中的温度上升,喷涂与吹气,冷却管道和镶块等对温度的影响。
优化生产周期的目的,并非仅仅为了缩短生产周期,提高生产效率;更重要的是为了提高铸件的品质和延长模具的寿命。目前,压铸厂均结合自身的经验,在实际投入大批量生产之前,通过多次的试模反复调试各种制程条件和生产工艺参数,获得较好的生产周期。然而,这并非是个简单的事情,在浪费大量的时间和成本的同时,要找到最优的生产工艺参数始终是相当困难的。这正是本文讨论的重点。
现有的主要优化方法与面临的挑战
数值模拟方法(hard computing硬计算)和主要问题
越来越多的商业铸造模拟软件,都相继拥有模具循环分析能力,可以预测每个周期的模具温度分布,也可以预测冷却管道对模具温度影响。然而,数值模拟的方法仍属于“您给定条件,并获得相应结果”的过程。这只能回答了在当前给定的条件下,会有怎样的结果,却无法提供优化的结果。简单而言就是在计算机环境下进行虚拟试模,仍然需要一次一次的不断尝试,而无法自动优化。
此外,传统数值模拟在模温循环与工艺优化上的主要缺点如下:
• 建立CAE分析模型比较困难。根据分析的目的,需要建立完整的模具,以及所有会影响温度的部件,如水管、油管等;
• 非常长的分析时间,由于至少需要分析5~10个周期才能获得稳态的模具温度;
• 仍处于用户给定条件,获取相应结果的阶段,换句话说,用户需要在计算机虚拟环境下,不断地测试各种条件。
• 结果分析困难,甚至对于方案改善,没有太大的意义。比如,用户只能获得整体的模具温度,但具体到某个点的温度是由于那条冷却管道的影响,影响的幅度,就不好确定了。
因此,虽然有不少关于该领域的研究,却没有真正的工业成功报告。
软计算(Soft computing)
软计算,是相对于数值模拟的硬计算而言的。软计算是利用非精确裕度和非确定裕度来获得易控性、鲁棒性以及低成本的方法集合。传统计算(硬计算)的主要特征是严格、确定和精确。但是硬计算并不适合处理现实生活中的许多问题,例如多少的房间温度让人体感觉最舒服。因此,软计算与硬计算最大的区别是基于宽容性的概念,宽容不精确,不确定性,局部和近似。#p#分页标题#e#
软计算不是一种单一的方法,而是多种方法的结合与协作,构成软计算的三个主要元素是模糊逻辑、神经元网络和进化算法,这三者分别提供不同方面的能力,其中模糊逻辑主要处理非精确性和进行近似推理,神经元网络使系统获得学习和适应的能力,进化算法则提供进行随机搜索和优化的能力。
运用软计算来进行铸造工艺过程的优化,一个最大的问题就是没有足够的数据样本进行优化,特别是对于复杂的模型。在进行优化之前,用户必须通过反复迭代计算,准备大量的样本数据,一旦铸件或者制程发生改变,样本数据又要重新准备,这是一个巨大的工作量。
数学优化(Mathematic optimization)
所谓数学优化,是指从一组可选项中,按照一定的标准,选择出最适配的元素。举个最简单的例子,优化问题通常包含:最大化或者最小化一个实际方程模型、在许可范围内的参数中系统化选择合适的输入参数,以及方程求解。优化理论的诞生以及其他方程技术,涵盖了大量应用数学的领域。一般说来,“优化”包含了寻找某些目标函数在指定域中的“最佳可用”数值,包括大量不同类型的目标方程,与不同的域类型。目前已经存在许多数学优化的方法,并在产品设计和其他领域得到成功应用。然而,对于铸造工艺过程的优化,最大的问题仍然是样本数据不足和收集困难的难题。
数学优化可以与生产周期数值的模拟结果结合在一起,但由于数值模拟的时间太长,所以仍然无法满足工业需求。例如,对于一个铸件,您需要10到20天去准备样本数据,然后才能启动数学优化计算。
结合工程知识库方法的数值模拟
为了解决铸造生产工艺过程优化的问题,C3P公司开发了一套全新的优化方法, 将工程知识库(KBE)和数值模拟的方法巧妙地结合在一起。这样,不但能实现全自动优化的目标,而且相比于传统的优化方式,收敛要更加快速,不受问题类型的限制,因为该优化过程并不需要准备样本数据。
KBE可以定义为:数字知识模型的工程化处理。这类知识模型通过知识重现技术而生成的计算机可控模型。知识模型可以输入或者存储在特定的工程应用软件上,可以让工程师确认要求,或基于这类知识模型去创建新的设计。目前在知识模型的开发上,有很多不同的方法,这通常取决于实际系统。
KBE 的另一个作用是作为知识管理和自动设计的桥梁。知识处理是当前计算机应用的最新进展,它将在工程应用中扮演重要角色。
Cast-Designer CPI 是基于有限元技术的数值模拟工具,拥有强大的网格划分和整体模具网格自动装配技术,同时得益于有限元技术,Cast-Designer可以同时使用四面体和六面体的混合网格。
事实证明,在流动结果上,六面体元素比四面体元素更加优秀,但凝固结果却几乎一样。同时,四面体元素应用于模具上,有许多的优点,例如:
a) 节省模型大小。四面体元素的大小比例比六面体元素的更大。由于模具的体积比铸件的大得多,如果完全使用高密度的六面体,将会在模具上耗费大量的元素,使计算模型非常巨大。
b) 四面体元素的几何表面特征描述更精细。冷却管道的直径与整体模具尺寸相比通常都比较小,表面使用三角形元素的四面体可以在高曲率区域有更良好的几何描述。
c) 良好的热分析能力和结果
d) 节省CPU时间,由于模型元素量的大量减少,缩短计算时间。这对于循环模拟非常有帮助,因为通常要获得稳态的模具温度,需要模拟5~10个生产周期。
整体模具网格装配技术,解决了多年来有限元网格模型建立的瓶颈问题,Cast-Designer 研发了多项网格核心技术,一键式完成了整体模具网格的自动建立与装配。如下图所示,节点的有效率高达38.2%,这是传统的FDM/FVM软件不可思议的,因为后者的有效率往往低于10%甚至5%, 从而使得整个系统高达上千万网格。
图1:Cast-Designer 中的网格技术与网格装配能力#p#分页标题#e#
Cast-Designer Production自动优化模块的工作原理
Cast-Designer Production 生产过程自动优化模块,是专门为批量生产中过程参数的优化而设计的。以达到最佳的生产效率和成本,并获得更高的产品质量。在此过程中,有许多实际的工业问题需要工程师解决,例如:
• 热平衡:获取均匀的模具温度,防止热节,过热区域和烧模等缺陷。
• 防止模具局部过冷,在整个产品生产周期中,维持合理的模具温度。
• 保持模具表面温度的均匀性,将对产品平面度有影响。
• 在保证产品品质以及模具温度的前提下,缩短生产周期。
• 监控模具温度和冷却管道的冷却性能
• 记录每次压射与生产循环,模具温度曲线
生产过程自动优化包括了冷却系统的优化设计、产品生产周期优化和获得合理的模具温度。该优化过程是完全自动的而且使用非常容易,不需要专门的知识。
热平衡和生产周期计算向导
生产周期计算向导,会帮助用户在热平衡的基础上,计算最佳的生产周期。也就是说系统从液态金属的带进来的热量将等于通过冷却管道和模具表面带走的热量。
用户需要定义一些基本的信息,包括铸件重量、模具尺寸和冷却介质的温度、速度等,然后,系统会自动根据以上的信息,计算出生产周期和长产率。冷却系统信息包括了媒介的温度、速度、冷却管道长度和直径。请注意,该数值仅基于热平衡的计算,并未考虑任何其他的工况条件,所以通常会短于实际的数值。用户还可以通过调整热影响率来平衡循环时间。
生产工艺制程设计
一个完整的热循环周期,包括了生产铸件的整个过程。这个周期可以再细分为几个阶段,工业上的排程也就是生产工艺制程的设计过程。越准确的阶段设定,会得到越准确的模拟结果。根据经验,热循环周期将细分为以下几个阶段:
阶段一,循环周期开始,充型、凝固和冷却过程
阶段二,开模和顶出铸件
阶段三,喷涂和冷却
阶段四,合模等待下一周期
以上各阶段定义,都包含在生产工艺排程(Process layout)页面中。用户可以自行定义,就像现在定义生产工艺指导书一样,在定义过程,如有疑问,可以打开软件内置的提示与向导,获取基于工程经验的参考值。该页面是针对高压铸造过程而设计,但同样也可以应用于其他的铸造工艺,例如低压铸造和金属型重力铸造。
模具喷涂
模具喷涂是生产过程中一个必须的步骤,主要目的是型腔的冷却和润滑。如果模具在局部出现高温区,将有可能导致烧伤、扣模的缺陷。涂层的均匀性也会导致铸件顶出是否顺利。
喷涂的时间与强度是根据不同的产品要求而选定。如果模具的型腔与表面积的比值较大,喷涂的时间也相对较长。
模具冷却与干燥
干燥冷却这一过程,主要是尽可能地减少型腔内的水分含量。水分会导致孔洞缺陷。这个过程通常会比喷涂的时间长,冷却时间可长达6~8秒。
铸造生产周期的总时间
铸造生产周期可以大约从30秒到1分30秒。这当中,最有影响力的几个因数包括:
− 铸件本身的最大壁厚
− 喷涂效率和喷涂的困难程度
− 型芯运动装置的效率
− 机器本身或者机器手的运动效率#p#分页标题#e#
− 设备本身的整体效率
软件可优化的参数包括:T15:铸件凝固和冷却的时间;T33:开模后的等待时间;T44:合模后的等待时间。另外的一些参数,是根据机器和模具结构固定的,并不在优化范围内,例如型芯的运动,模具开合的运动时间等。
传感器定义
在运行优化之前,用户必须在模型上,先定义一些传感器。在优化计算的过程中,求解器会检查这些传感器的数据,自动优化调整生产工艺参数,以达到预定的优化目标。因此,传感器可以说是优化计算的鼻子。
定义传感器非常简单,只需要在模型上选择一个节点即可,传感器上的主要参数包括:
铸件顶出的最高温度:定义铸件顶出的最高温度。在此温度以上,金属液并未足够冷却,此时刚度不足,强行顶出将直接损坏铸件。例如,铝合金,大概400度左右可以考虑顶出。
铸件顶出的最低温度:相反,如果顶出时,铸件温度过低,则会对模具产生巨大的收缩抱紧力,导致顶出时,铸件变形等缺陷。因此,我们可以定义铸件顶出的最低温度,也就是说在此温度之前,就应该对铸件进行顶出。
合模最高温度:达到该指定温度时,合模准备下一周期的开始。模具温度过高会影响铸件的凝固,对于模具寿命也有较大的影响。
合模最低温度: 模具整体温度在我们定义的最高温度和最低温度范围内,就会做合模的动作,准备下一个循环的开始。一个平衡的模具温度,对于稳定产品质量很有帮助。
铸件顶出时,最小的固态分数(%):例如,我们可以在优化过程中,指定铸件整体凝固到85%时,做顶出动作。这是一个全局参数,可应用在整个铸件上。
关联冷却管道与传感器
此外,该传感器还可以关联到冷却管道,自动优化冷却管道的热交换系数(HTC)。该功能对于辅助调整拥有复杂的冷却系统的模具非常实用,因为用户难以通过模拟或者是试模,获得调整冷却管道的数值建议。
.简单而言,当传感器与冷却管道关联之后,优化计算启动,求解器就可以根据传感器获得温度,对比优化的温度范围,如果温度过热,则加强该位置冷却管道的相关参数,反之,则减少该位置的冷却管道参数。另外,传感器可以同时关联多条冷却管道,考虑多条管道的相互影响。
优化结果
整个优化过程是全自动的,且容易使用。所有的参数都会被保存到一个文件中,可重复使用。
优化求解器可以自动反复调用Cast-Designer CPI 的求解器,反复迭代计算并优化。用户只需要跟定义普通的热循环模拟过程一样,定义相应的边界条件即可。而且只需要定义一次。
在每一次的迭代计算中,系统会自动报告当前的优化结果,例如新的开、合模时间,和总的生产循环周期。
优化过程文件将会输出为Project_iter_i_Report.txt 文本文件。格式如下:
在以上的优化案例中,优化过程只用了三次的迭代,每次迭代计算3~5个热循环。生产周期从86秒缩短为66秒,更重要的是,模具有更好的热平衡,而且铸件质量更好。
以上是优化之前的铸件顶出时温度分布,局部区域温度达到480度,高温区域导致了烧伤,扣模缺陷。冷却系统设计有待改善。 通过系统自动优化冷却管道参数之后,铸件顶出时的最高温度为400度,解决了烧伤,扣模的缺陷。
#p#分页标题#e#
上图显示的是优化之前,模具的温度分布,在下一循环开始之前,温度过低,导致冷隔缺陷。同时,由于模具温度不平衡,也影响了铸件的性能。 在优化之后,模具平均温度为260度,解决了冷隔的缺陷问题。同时,模具的温度分布更加均匀,最高模具温度为300度。优化后,该模具寿命延长。
图7,Cast-Designer 针对某油底壳生产过程参数优化结果