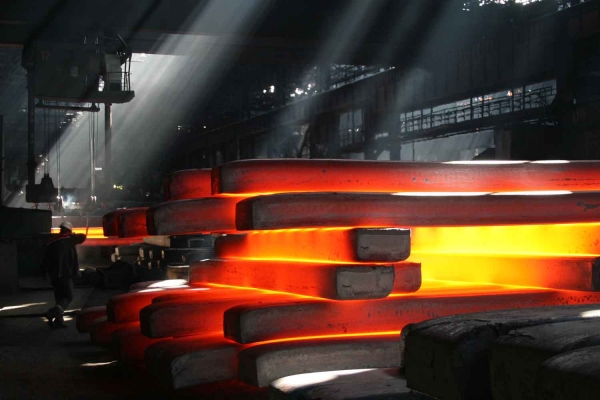
文:剑涛铝业 袁晓东
前言
这些年,铸造铝合金零部件的原材料用料已从以原生铝为基体的合金锭逐步转向了以再生铝为基体的合金锭的变化。铝合金铸造行业与再生铝生产行业成了产品与原料密不可分的关系。在产品铸造过程中出现的种种问题,常常成为铸造企业与再生铝企业相互扯皮不清的事实,零部件铸造企业首先质疑原材料,而再生铝生产企业则举例证明不是原材料问题,公说公有理,婆说婆有理。究其双方矛盾的根本原因在于:如何根据本企业零部件产品来确定使用再生铝铸造铝合金锭和相应的理化指标及检验标准还缺乏认知。目前再生铝生产企业原料的各项理化指标及检测标准是由各零部件铸造企业提出的,而零部件铸造企业对于再生铝合金材料的认知却是陌生的,对再生铝铸造企业提出适合自身产品的技术要求对于铸造企业来讲是个难题,因为在所有的合金牌号中的合金元素和物理性能都只是一个范围,怎样根据自身产品来取舍,或者改性等等,对于一般铸造企业来说不仅仅是挑战,更需要走出对再生铝原料的认知误区。
1 铸造产品与原材料牌号及成分的关系
原生铝合金锭与再生铝合金锭的最大区别在于再生铝合金锭是合金化后的废铝为原料,元素合金化后的熔点都低于其作为单一元素的熔点,因此再生铝熔化时的熔点低于原生铝,这为以后材料遗传埋下了伏笔,且再生铝中的成分及含量十分复杂,纯度大大低于原生铝,其杂质相虽能使合金的强度硬度性能大幅提高,但有害杂质的过多并不适用于有一定综合性能性能要求的压铸件。
目前压铸(造)行业所遵循的工艺、牌号及成分等,都是以原生铝合金为基础制定的工艺、牌号及成分。当再生铝合金替代原生铝成为压铸件的原料后,压铸(造)工艺、合金牌号及成分,包括模具设计等等却仍然沿用原生铝的工艺、牌号和成分和设计要求,很显然已经违背了再生铝的特性。沿袭以原生铝为基础的工艺、牌号及成分,势必将给铸造企业及再生铝企业带来误区和影响。
原生铝合金锭是根据成分要求在纯铝中添加一定比例的其他合金元素,如铁、硅、铜、镁、锰、锌等等。原生铝与再生铝最大的不同在于,原生铝为纯铝,其基底组织柔软性强、连续性好,呈现的是连续相,延展性强,添加的合金元素被铝包裹,完全合金化后获得强度与延展性均佳的整体性能。
再生铝的基底包含了很多金属间化合物和非金属杂质,如二相铁、钙、锰铁化合物等等元素,使其杂质(溶质)原子浓度大增,其基底的连续性被破坏,分散相强化的铝硅系合金中,铝如果完全包裹住硅,且连续相完整,达到完全合金化,则可获得强度和延展性均好的整体性能。反之如果连续相不完整,硅、铜等作为单一元素析出,与其他元素形成电子化合物硬质点,虽有了强度,但延展性差,不能获得好的整体性能。一旦偏聚还会使产品加工中出现“打刀”现象。大量的体积很小的分散相,在微观结构中阻碍了位错的运动,因此提高了材料的强度。在简单的分散相强化材料中,只有两相。强而硬的一相被引入到强度低但延展性较好的另一相中。强度低的这一相,通常是连续的,被称作基底(如纯铝);强度高的一相被称作分散相(如硅)。相图中,连续的部分就是连续相,不连续的就是分散相。因此,强而硬的相也可以作为连续相,这时强度低的一相就是分散相。但这起不到分散相强化的作用。分散相强化的关键就在于要使强度低、延展性好的一相(纯铝)包裹住大量小颗粒的强而硬的第二相(硅)。在大部分合金中,分散相强化是通过相转变过程完成的。如共晶和共析反应。共晶反应是固溶转变,是一种液相降低到某一温度时同时转变成两种固相。共析反应是一种固相降低到某一温度时同时转变成另两种不同的固相。基底应是强度低的、可延展的、连续的。分散相应是硬的、强度高的、不连续的、尽可能体积小、数量大、呈球状而非针状或带有棱边的。
要得到好的分散相强化效果,就要合理控制分散相。通常铝硅系合金要想获得综合机械性能,并非硅的含量越高越好。各项成分指标不能硬搬牌号成分,而应根据压铸产品本身的性能要求,对再生铝原料基底;(即 A00)的加入量提出要求。特别是浇铸和薄壁件产品,更应该注意再生铝合金锭中杂质。
我们常常见到压铸企业与再生铝企业关于原材料成分的争论,双方争论的焦点往往聚集在成分的范围值上,对原材料是否成分超标或不达标十分看重,依据的成分标准往往是牌号规定的元素的成分,却对再生铝作为原材料的特性缺乏认知。再生铝本身就已经包含了太多已知和未知的元素,这些元素在液态固化过程中对强度、延展性等等起到什么作用,用完全废料再生铝锭作为原料是否满足该企业压铸(造)零部件件的性能要求,压铸(造)企业是否针对自身产品的性能要求对再生铝原料供应企业提出哪些性能要求等等,都是值得压铸(造)企业认真思考的。
如果压铸产品要求不高,对塑性没有要求,一般的结构件,那么原料可以全部用废铝。如果压铸产品对整体性能要求较高,既要有延展性又要有强度、硬度还要耐腐蚀性好,那么压铸企业就必须对再生铝企业原料的材料基底提出符合自身产品要求的理化指标要求。
如上所述,目前压铸行业和再生铝行业遵循的工艺、牌号、成分及标准,不完全适用于再生铝合金原材料,也不完全适用于再生铝为原料的零部件铸件。压铸企业在选择以再生铝合金锭为原材料时,重点在于根据自身产品的特性和使用要求,有针对性的对再生铝铸造企业提出符合自身产品特性(强度、硬度、塑性、耐腐蚀性等)的技术标准和要求。
2 材料遗传性与材料组织结构
经常听到的话题是;成分合格,压铸工艺又没变化,但是压铸件就是有问题。这不单是成分出了问题,也许是材料的内部组织结构的问题。材料缺陷是可以遗传的,材料的遗传性是指原材料的组织状态对压铸(造)产品的组织和性能的影响。原材料熔化变成液态后还存留多少固态组织特性,在未来的固态组织中起什么作用及影响,是压铸行业对再生铝行业认知的一个盲区。
再生铝合金锭是由废料熔化加工制成,除了废料作为主料外根据成分需要还将添加辅料及变质剂等,一些废铝中原始的缺陷固态组织或化合物残存有可能在再生铝硅系合金锭中遗传下去,对后续压铸(造)产品的组织和性能势必形成影响。
消除组织遗传性与再生铝的熔炼的工艺及条件,如:温度、时间、精炼、搅拌、熔体净化、作业方式等密切相关。改变熔炼时的工艺条件可增大或减小甚至消除原材料组织遗传性对再生铝合金锭显微组织和性能的影响。
目前行业内的再生铝熔炼工艺沿袭的是原生铝的工艺条件,原生铝为纯铝,再生铝为合金化后的废铝,纯铝与废铝的基底组织有着很大的区别,很显然原生铝的熔炼工艺不能完全适用于再生铝。
众所周知,当合金熔化接近液相线温度时,熔体呈现显微分层现象,此时铝液并非呈真正的熔融状态,而是悬浮着富集组元的微细弥散胶状颗粒,这种显微分层可称为亚稳定乳化或一种组元富集胶状悬浮粒子。这种亚稳定胶状粒子保存原料的组织特征,成为材料组织遗传的载体。而这些显微富集的胶状悬浮粒子所占的体积比及其大小、弥散性与熔体过热温度、熔化过程的控制、工艺的选择、熔体净化或处理等密切相关,就再生铝硅系合金而言,要过热到液相线之上较大的一个温度区间,富集胶状悬浮粒子才可能消失。因而,熔化工艺、处理手段和条件对材料组织遗传性的影响很大,可明显改变结晶条件,随之改变凝固后的铸锭或铸件的组织和性能。
当合金原材料已经形成材料遗传性后,在后期的压铸阶段是无法消除的。例如;共晶型铝硅合金中,硅作为单一金属的熔点是 1400℃左右,一般反射炉中与铝完全合金化状态约 800℃左右,而后期压铸的温度不可能达到或超过,如果有块状初晶硅存在,是无法克服的,如前所述,要改变原材料的遗传性,只能在原材料的熔化过程中采取相应的处理条件才能改变,所以,在压铸阶段想改变原材料的材料组织缺陷几乎是不可能的。
综上所述,当压铸(造)零部件产品原材料发生变化时,所遵循的原材料标准及压铸工艺条件包括模具也应随之改变。全废料的 ADC12 并不能适用于所有的压铸(造)产品。不同的产品必须根据产品的性能要求来选择原材料,并非一味的唯成分论或成本最低来选择,需根据产品本身(强度、硬度,塑性、耐腐蚀等等)性能的需要,有针对性地对原材料基底或理化指标提出具体要求。