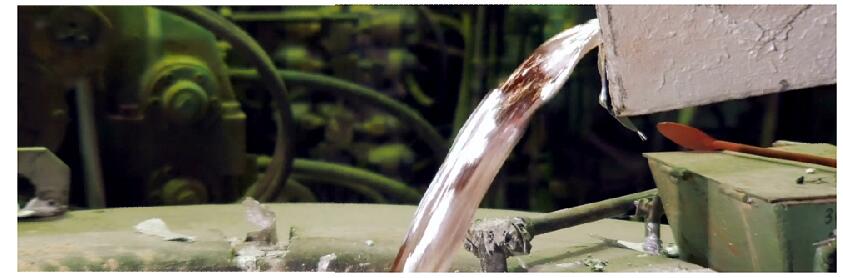
文:山东盟威集团有限责任公司 朱利民
摘要 纯铝接供液直接应铸造厂用于生产铸件(铝活塞、铝轮勃。与传统的二次熔化工艺、一次熔化工艺,相比、节约了能源,减少了材料烧损,提高了生产劳率.且利用纯铝液直接生产的零件质量优、性能好。
为了更大地节能降耗,我集团公司近年来开发了一项提高效益的实用新技术—纯铝液直接供应铸造厂用于生产铸件(铝活塞、铝轮毅),经集团下属企业—滨州渤海活塞股份有限公司、滨州盟威BBS轮毅有限公司三年多的实践,证明该技术节约了能源,减少了材料烧损及对环境的污染,生产的铸件质量优、性能好,具有良好的经济和社会效益。
一、传统熔化工艺技术
传统的铝合金铸件的铸造工艺过程是:熔化铝合金锭-铝液精炼变质处理-铸造。此工艺在熔化过程中的优点在于,企业只需购买合格的铝合金锭,生产时投料熔化即可,无需再添加其他合金成分,生产过程简单且容易控制,但购买铝合金锭的价格要高于购买纯铝锭的价格约800一1200元八(根据合金元素的配比不同而变)。出于节约的目的,部分企业对熔化过程进行了改进,将直接熔化铝合金锭这种“二次熔化工艺”改为“一次熔化工艺”,即直接熔化纯铝锭及合金配比中各个单一的金属材料,虽然配料和质量控制较烦琐,操作也较辛苦,但是换来的却是可观的经济效益。
根据实际测算,与“二次熔化工艺”相比,采用相同的熔化设备和处理技术,“一次熔化工艺”熔化铝合金可节省资金200一300元/t。我公司应用“一次熔化工艺”生产发动机铝活塞近30年,累计生产约1.2亿只铝活塞,配料熔化量约30万t,与“二次熔化工艺”相比,节约资金至少6000万元。
尽管“二次熔化工艺”和“一次熔化工艺”有所差别,但是均要对铝锭(合金或纯铝)进行重熔,因此两者均属于传统的熔化工艺技术。可采用的主要熔化设备有熔池式炉、塔式炉或感应炉,这要根据熔化的材料合理选用设备;处理时多采用以六氯乙烷或四氯化碳为主要成分的精炼剂、钠盐、惚盐、蹄盐或磷盐类变质剂等化学熔剂对铝液进行精炼和变质处理。为保护环境,熔炼过程需采取废气收集处理方法治理污染,后来出现了污染较低的精炼和变质化学熔剂,以及气体精炼方法,近年来又出现了合金型变质剂,较好地解决了合金处理时的环境污染问题,但是熔化时的能耗仍然较高。
二、新工艺技术
1.开发背景
提高企业经济效益和社会效益是大家共同的追求。为进一步扩大产能,2002年我公司进行了盟威集团工业园的规划,设计时充分考虑了节能和环保问题。工业园的总体规划是将已有的发动机铸造铝活塞项目整体迁人及扩产作为主体(规划产能为3000万件/年)。新建了铸造汽车铝轮毅产品项目(规划产能为900万件/年、一期工程为150万件/年)。由于这两个产品均是以铝合金作为原料,且用量较大(一期工程合计用铝合金至少6万t),通过充分的方案论证,在工业园的总体规划设计中决定发展铝材料产业,将产业链向上游延伸,拓宽企业的产业链,建设了年产5万t的纯铝生产厂。这样在工业园内便可以优化工艺路线,缩短工艺流程,直接从纯铝厂向铝活塞、铝轮毅产品生产的铸造现场运送合格的铝合金液,省去电解铝厂将铝液铸造成铝锭的工序,也即省去后续产品在铸造生产中将铝锭再次熔化为铝液的能耗,减少熔化时的环境污染和铝的烧损,节约能源和材料消耗,降低生产成本,提高生产效率,同时也减轻了工人的劳动强度。
2.新工艺技术方案
(1)熔化技术及质量控制方案由于铝活塞是发动机的心脏零件,铝轮毅是汽车的安全部件,因此对其质量的要求非常高。为确保产品的质量,我们先期进行了工艺试验,并在试验的基础上制订了详细的工艺技术方案和质量控制方案。具体的技术方案是:采用真空保温浇包,将纯铝厂生产的铝液(约950℃),用专用汽车转运到其铸造车间的熔池式保温炉内(容量至少12t以上),利用纯铝液自身的高温(必要时采用少量加热的方式辅助熔化或保温),熔化合金配比中各个单一的金属材料;熔化后采用合金型铝液处理技术进行初步的铝液处理(添加部分长效细化剂和变质剂),消除了化学熔剂对铝液进行处理时产生的废气污染。为提高熔化速度和材料的均匀性,炉底设置电磁搅拌器,在熔化阶段对铝液进行搅拌(熔化速度至少提高一倍)。均匀的搅拌,特别是电磁搅拌,对确保铝合金液的质量和处理效果是十分有利的。
质量控制是此过程的关键。为准确地配料,真空保温浇包在运铝液前后均要称重,加人的合金也要准确地称重。铝合金液在熔化及处理完毕后,炉前取样采用热分析仪、光电光谱仪对材料进行化学成分、材料密度、晶粒度和变质效果分析,确认合格后再将铝合金液转运到产品铸造的生产现场。
(2)铝液运输方案在铝厂的铸造车间,采用纯铝液直接配制成合格的铝合金液后,通过物流路线,利用转运保温浇包和运输车辆,将液态铝合金直接运送到铝活塞铸造厂和铝轮毅铸造厂使用现场的保温炉内。此方法在国内铝活塞和铝轮毅行业属于首创,不但省去了铝厂将铝液铸造成铝锭的工序和该过程的热能浪费,还省去了在产品铸造车间将铝锭再次熔化为铝液的能耗,简化了工艺流程,缩短了工艺路线,减少了铝锭重熔时的二次环境污染和铝熔化时的烧损,节约了材料的熔化消耗费用,降低了生产成本,具有良好的经济和社会效益。工业园平面布置及运输路线示意见附图(铝厂到铝活塞铸造厂约l00m、到铝轮毅铸造厂约200m)。
3.应用效果
(l)铝液质量在利用纯铝液直接配制铝合金液的这项新技术中,由于配料时采用了大容量的炉型、先进的炉底电磁搅拌技术、合金型铝液变质细化处理技术,以及更先进的炉前质量过程控制手段,使每炉材料、炉与炉之间材料的均匀性和一致性更好,处理的效果稳定;同时铝液的合金化是在高温下完成的,经历过高温熔炼获得的铝合金液的质量更好;生产条件得到改善,工人的劳动强度大大降低。根据我公司三年多的生产实践,新工艺与传统的熔化工艺(特别是“一次熔化工艺”)熔化的合金相比,材料合金成分波动的离散度减少了约20%,经热分析仪检验及显微分析确认,材料的密度均匀,细化、变质处理的效果一致性好,处理的效果更加稳定。在合金的冶金质量方面,新工艺优于传统工艺,质量保证能力得到了提高,为确保材料的一致性、提高产品的力学性能和使用性能奠定了坚实的基础。
(2)铸造质量利用纯铝液直接配制铝合金液、直供铸造厂生产铸件(铝活塞、铝轮毅)的新工艺,由于材料合金成分波动的离散度小,材料的均匀性和一致性好,因此铝合金液体性能的一致性也好,从而保证了铝合金液铸造性能的一致性,减少了产品铸造质量的波动,铸造综合废品率有所降低,其中普通铝活塞废品率≤2%、镶圈盐芯铝活塞废品率≤5%、普通铝轮毂废品率≤5%、表面抛光铝轮毂废品率≤10%。综合指标处于国内领先水平,达到了国际先进水平。
(3)材料性能该项新工艺的应用,由于材料合金成分波动的离散度小,产品内在质量的波动小,因此产品材料的均匀性和一致性好,从而保证了产品的力学性能和使用性能。材料的力学性能与化学成分、熔炼工艺、铸造工艺及热处理工艺等均有关系,我们在同样的生产条件下对铝活塞和铝轮毅的本体材料进行了大量的抽样测试,结果显示,新工艺与传统工艺相比,材料的硬度、抗拉强度(室温、300℃)、伸长率、疲劳强度和抗冲击性能等力学性能指标基本上是一致的,其中硬度、抗拉强度、伸长率等指标的波动范围缩小了5%-10%,这一点有利于确保产品的使用性能。产品经过试验室试验和装车路试,以及三年来的大批量生产和应用,证明产品质量优异、性能可靠。
(4)效益采用该项新工艺,由于省去了电解铝厂将铝液铸造成铝锭的工序和该过程的热能浪费,又省去了在产品铸造车间将铝锭再熔化为铝液的能耗,简化了工艺流程,缩短了工艺路线,减少了铝锭重熔时的二次环境污染及铝锭熔化时的熔炼损耗和熔化能耗。另外,采用的炉底电磁搅拌技术,不但提高了材料的均匀性和一致性,且缩短了配料的熔化时间,节约了材料的熔化消耗费用,降低了生产成本。
目前,我公司铝活塞已达到的年产2500万件、铝轮毅已达到的年产120万件,每年使用约50{以〕t铝合金,按3%的烧损率计算,新工艺可减少约1500t铝的熔炼耗损及熔化能耗,价值约3100万元,与“一次熔化工艺”相比,减少铝锭重熔时的能耗价值约2000万元,合计年节约资金超过5100万元,大幅提高了企业的经济效益和社会效益。
三、结语
实践证明,利用纯铝液直接供应铸造厂生产铝活塞、铝轮毅等汽车关键件的新工艺是切实可行的,该工艺填补了国内行业中的生产技术空白,新工艺与传统工艺相比,节约了能源,减少了材料的熔炼损耗,合金质量好,铸件质量优,材料性能好,提高了生产效率,降低了生产成本,减少了环境污染,也减轻了工人的劳动强度,具有良好的经济效益和社会效益,值得有条件的企业尝试,同时也可尝试生产其他的铝铸件。