文:集美大学机械工程学院 沈江南
压铸机、压铸模具及压铸合金是压铸生产的三大要素,压铸工艺则是将这三大要素进行有机组合和综合运用,并规定其具体的工作方式。因此,合理的压铸模具设计(主要指浇注系统和排溢系统设计)和正确选择与控制压铸工艺参数对压铸件的成形质量及压铸模的使用寿命至关重要。
1.1 锌合金压铸盖板件
结合某型号锌合金盖板件(其三维造型如图 3.1 所示),对锌合金压铸过程进行研究,包括压铸工艺参数的选择、压铸浇注系统和排溢系统设计等内容。
该盖板件外形轮廓尺寸长为 166mm,宽为 55mm,高为 4mm,壁厚较为均匀,包括内侧加强筋厚度在内,最大壁厚为 3.75mm,最小壁厚为 1.75mm,平均壁厚约为 2.5mm。材料为 ZA8 号锌合金。由于该产品为外观件,表面需要进行电镀处理,要求表面光洁。
1.2 压铸工艺参数
压铸生产过程中,压铸工艺参数的选择极大影响着压铸件的机械性质和品质,一般来说,压铸工艺的基本参数包括四个方面,即压力、速度、时间及温度。
1.2.1 压力
压力是压铸工艺的基本特征,也是获得铸件组织致密和轮廓清晰的保障因素。在压铸过程中,熔融金属液的流动和压实都在压力的作用下完成,但压力通常不是一个常量,其表现形式有压射力和压射比压两种。
1)压射力
压射力是指压铸机压射机构中推动压射活塞运动的力,其大小根据压铸机的规格来确
定,通过调整油缸的压强在一定范围内调整压射力,其关系如公式(1.1)所示:
式中:

为填充压力(N);

为液压系统的管路工作压力(MPa);

为压铸机压射缸活塞的截面积(mm2)。
2)压射比压
压射比压是指压室内熔融金属液单位面积所受压力的大小,即压射力通过压射冲头对熔融金属液所施加的压力,其计算公式如下:
式中:

为压射比压(Pa);

为压射力(N); A 为压室面积(mm2);B 为压室直径(mm)。
压铸生产中,通常将充填时的比压称为压射比压,用于克服金属液在浇道及模腔中的流动阻力,特别是内浇口处阻力,一般热室压铸机提供的压射比压可达到 20-50MPa。
由公式(1.2)可知,使用压铸机提供的最小压射冲头方能获得最大的压射比压。在选择压射比压时,应充分考虑压铸机能够提供的压射力及所使用的压射冲头,在保证压铸件质量要求的前提下,宜使用较低的压射比压,避免高压射比压对压铸模具和机器的磨损。
1.2.2 速度
在压铸过程中,速度与压力共同影响着压铸件的内部组织和表面质量,压铸速度一般分为压射速度(也称冲头速度)和充型速度(也称内浇口速度)。
1)压射速度
压室内压射冲头推动熔融金属液移动的速度,称为压射速度。在热室锌合金压铸生产中,压射速度一般控制在 0.3-0.5m/s。
2)充型速度
充型速度是指金属液在压力作用下,通过内浇口进入模腔的线速度,它是重要的工艺参数,对充型模式和压铸件最终的质量有着重要影响。若充型速度太小,易造成铸件轮廓不清;若充型速度过高,容易引起紊流、卷气、氧化及粘模等现象,还会加速模具的冲蚀磨损。锌合金的推荐充型速度可见表 3.1。
其中,铸件平均壁厚 ,可按下式计算:
#p#分页标题#e#
为确定该盖板件的平均壁厚,通过在盖板件上分别取 3 个截面(如图 3.2 所示),并测得各截面对应的壁厚和截面积。
故可算得盖板件的平均壁厚:
由表 3.2 可得该盖板件压铸时充型速度在 40-48m/s 之间。
1.2.3 温度
压铸过程中,金属液的流动性受温度的影响较大,故控制和保持温度条件的稳定性对金属液的充型十分有利。该温度条件包括金属液的浇注温度和压铸模具的工作温度。
1)浇注温度
浇注温度是指金属液进入浇注系统时的温度,生产中一般通过控制坩埚内熔融金属液的温度来实现对浇注温度的控制。浇注温度一般高于合金液相线温度 20-30℃,若适当提高浇注温度,能够有效地
减少合金液在压射过程中的热损失,使金属液在充型时保持良好的流动性,但过高的浇注温度易导致金属液吸气氧化及粘模,使压铸件出现气孔,影响压铸模具寿命。另外,锌合金压铸的浇注温度的选择还需考虑到压铸件的壁厚及结构特征,具体可参考表 3.2。 ZA8 号锌合金的液固相线温度范围为 375-404℃,含铝量约为8.0-8.8%,故取该盖板件的浇注温度为 425℃。
2)模具工作温度
压铸模具工作温度影响到压铸件机械性能,尺寸精度和压铸模的寿命。压铸模具温度过高,容易导致粘模、压铸件顶出变形、开模时间延长等。一般情况下,压铸模具温度控制在浇注温度的 1/3 左右为宜,薄壁、结构复杂的压铸件可适当提高。通常,锌合金推荐的压铸模具工作温度为 150-200℃。本文中对该盖板件进行数值模拟时,压铸模具工作温度设置为 170℃。
1.2.4 时间
压铸工艺中的时间因素包括充型时间、持压时间和留模时间。
1)充型时间
金属液进入浇注系统到充满模腔的过程所用的时间称为充型时间。充型时间应该保证金属液在失去流动性之前完成充型。若充型时间过长,将使充型过程中金属液温度降低过多,金属液提前凝固,容易导致压铸件产生冷缺陷。
充型时间与合金特性、压铸件壁厚、浇注温度等诸因素有关,表 3.3 是基于铸件平均壁厚的充型时间推荐值,。由前面的计算可知,该盖板件的平均壁厚约为 2.5mm,由上表可得建议的充型时间范围为 22-32s。
2)持压时间
金属液完成充型后,压射系统继续保持压力的时间,称为持压时间。其目的是保证金属液在高压之下凝固,以获得致密的结晶组织,改善压铸件品质。金属液的凝固时间与压铸件的壁厚、合金凝固温度范围有关。锌合金压铸生产中,基于压铸件壁厚的持压时间推荐值见表 3.4。
3)留模时间
从持压结束到开模的这段时间称为留模时间,主要是使压铸件在型腔中冷却到一定温度,具备一定的强度,避免在顶出时发生压铸件变形。但留模时间过长,易因压铸件的冷却收缩量变大,包紧力增大,导致抽芯和顶出铸件的阻力变大。锌合金压铸生产中,基于压铸件壁厚的留模时间推荐值见表 3.5。
综上,该锌合金盖板压铸模拟仿真时推荐的压铸工艺参数为:充型速度为 40-48m/s
之间,充型时间范围为 0.022-0.032s,浇注温度和模具工作温度分别为 425℃和 170℃。
1.3 浇注系统设计
浇注系统是引导金属液进入模腔的通道,锌合金压铸浇注系统由内浇口、横浇道和直浇道三部分组成。浇注系统的设计直接影响着金属液进入型腔的位置和方向以及流动状态,对铸件的成形质量具有非常显著的影响。可以这样说,在任何情况下,由于浇注系统设计不当所造成的影响,是几乎不可能通过改善其它压铸参数进行补偿的,故浇注系统的设计是压铸工艺及压铸模具设计中的关键内容。#p#分页标题#e#
1)内浇口设计
内浇口设计是为实现将金属液以最佳的流动状态引入模腔,获得良好的充型模式。通过对大量压铸生产实例的分析,不难发现压铸模具的内浇口设计对于压铸模具“适应性”的影响很大,一个合理的内浇口设计是生产出优质产品、保证模具“适应性”的基础。
内浇口的设计首先应根据铸件的结构、形状确定浇口位置,然后确定内浇口的浇口截面积。选择内浇口位置时,应该注意以下三点:尽可能缩短金属液流程;尽量避免金属液正面冲击型芯或型壁,否则易造成型芯或型壁冲蚀、粘模及流动混乱现象;尽量使用单个内浇口,当采用多个内浇口时,要充分考虑金属液汇流时相互冲击,产生涡流、裹气等影响。鉴于以上三点的考虑,盖板件内浇口位置显然应取在边长较长的两侧,以实现金属液流程最短。
常用的内浇口与型腔的连接方式有侧向连接、直接搭接、端部搭接和侧向对接四种。其中,侧向连接方式适用于平板类压铸件和薄壁类压铸件,端部搭接方式和直接搭接方式都适用于深腔压铸件,而侧向对接方式则适用于筒类压铸件。由此可见,锌合金盖板适合采用侧向连接的方式,当金属液以一定的入射角度进入模腔后,将直接冲向对面型壁,确保金属液的流程最最短,且不正面冲击型芯。
综上所述,锌合金盖板的内浇口设计如图 3.3 所示。
内浇口截面积的计算原则是金属液尚未凝固而模腔充填完毕,可利用流量计算法(公
式 3.4)进行估算:
式中: G为通过内浇口的金属液质量(g); t为充型时间(s);

为充型速度(m/s)。
应该注意的是,根据相关资料文献建议的充型时间和充型速度所计算得出的内浇口面积可能会有一定的差异,但在确定最终结果时,一般先选择较小的计算值,或根据经验在该计算范围内选择一个值,然后经试模后视具体情况再修大内浇口面积。利用 Pro/E 软件的“分析”指令,可获得该盖板件体积约为 22183.90mm3,在利用公式(1.4)进行内浇口面积计算时,通常将排溢系统体积按铸件体积的 30%进行计算。因此,结合前面得到的充型速度和充型时间,有:
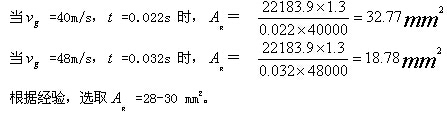
对于薄壁锌合金压铸件,内浇口厚度建议为 0.2-0.5mm,考虑锌合金盖板件的结构及尺寸特征,为达到均匀充填,获得良好的充填模式,对该产品采用内浇口厚度介于 0.2-0.35mm 之间的不均匀厚度设计,内浇口宽约为 100mm。
2)横浇道设计
横浇道是连接直浇道和内浇口的通道,其作用是将金属液以一定的温度、压力、速度平稳地传递到内浇口。同时,横浇道中的金属液还能改善模具热平衡,在压铸件冷却凝固时起到补缩与传递压力的作用。
横浇道设计首要考虑的原则是保证横浇道截面积逐渐减缩,即确保横浇道截面面积在任何情况下都不小于内浇口截面积,使金属液流动保持充满、连续状态,以减少涡流卷气。
横浇道的减缩率一般控制在出入口截面面积比为 1:1.1-1.3 之间为宜。根据经验公式,横浇道入口截面积通常取为内浇口面积的 3-4 倍。
锥形浇道能够使金属液快速而均匀填充模腔,且适用于可开设长浇口的铸件,故针对盖板件的特征而选用锥形浇道。目前在锌合金压铸中,最普遍采用的是梯形截面浇道,确定横浇道最小截面积后,可根据经验公式(1.5)确定横浇道的深度和宽度。
式中:A 为横浇道截面积(mm2);D 为横浇道深度(mm);W 为横浇道宽度(mm);

为拔模斜度。
取横浇道截面积 A 为 100mm2(约 3.5 倍于内口浇面积),横浇道深度 D 取为 10mm,出模斜度取为 10°,根据公式计算得宽度 W 约为 11.8mm。#p#分页标题#e#
综上,该锌合金盖板件的浇注系统如图 3.4 所示,其中,内浇口面积约为 28 mm2,主横浇道为截面积约 98 mm2的梯形截面。图 3.5 为内浇口宽度和厚度分布示意图。
3)直浇道设计
直浇道是传递压力的首要部分,其结构与所选用的压铸机类型有关。热室压铸机直浇道由压铸机喷嘴和模具上的浇口套及分流锥形成。有几种类型的直浇道可用于锌合金压铸,其中包括普通型、等面积型、横直浇道合并型等,在锌合金压铸生产中,广泛采用能获得平稳流动的横直浇道合并型直浇道,如图 3.6 所示,其中,浇道面积由 A 到 B 递减,以保证充填时浇道保持充满、连续的状态。
1.4 排溢系统设计
压铸模设计中,排溢系统不可缺少,其主要作用是排出和收集气体、涂料残余物、前端污冷金属,达到转移或减少压铸件中裹气、氧化夹杂等缺陷。其次,排溢系统亦能够改善金属液的流动状态。故排溢系统可以适当弥补由于浇注系统设计不合理而带来的一些铸造缺陷,在压铸模设计中通常将其与浇注系统作为一个整体来考虑。
1)溢流槽设计
溢流槽又称集渣包。它的作用是收集金属液的前端冷污金属、氧化夹杂物,提高压铸件的质量。此外,溢流槽常作为压铸件脱模时推杆推出的位置,能够防止压铸件变形及避免压铸件表面留有推杆痕迹。
溢流槽开设的位置应是金属液最先冲击的部位或金属液汇流处;另外,在内浇口两侧
或其他金属液不能直接充填的死角区域也应开设相应的溢流槽来实现该区域的充填。
2) 排气槽设计
压铸生产时,金属液的充填速度非常快,充型时间非常短,故型腔中的空气及涂料挥发产生的气体的排出是一个极其重要的问题。开设排气槽的目的是让型腔中的气体在充型时尽可能多地被金属液挤出,排气槽一般与溢流槽配合,设置在溢流槽后端以加强溢流和排气效果,推荐的排气道厚度为 0.05-0.2mm。此外,在设置推杆、活动型芯和分型面等处,也可以利用该处的配合间隙实现排气。
综上,完成锌合金盖板件的压铸浇注系统及排溢系统设计,如图 3.7 所示,其中,溢流槽体积为 3559mm3,约占铸件体积的 16%。
1.5 总结
本文以某型号锌合金盖板件为研究对象,详细介绍了锌合金压铸中压铸工艺参数选择和压铸浇排系统设计的原理与方法,并完成了该产品的压铸工艺参数选择及压铸模设计。
1)根据相关文献及生产经验,确定该产品的压铸工艺参数,包括充型速度、浇注温度、模具工作温度等;
2)结合产品的结构特征,详细阐述该产品的浇注、排溢系统的设计过程,包括内浇口设计、横流道设计以及排溢槽设计等。