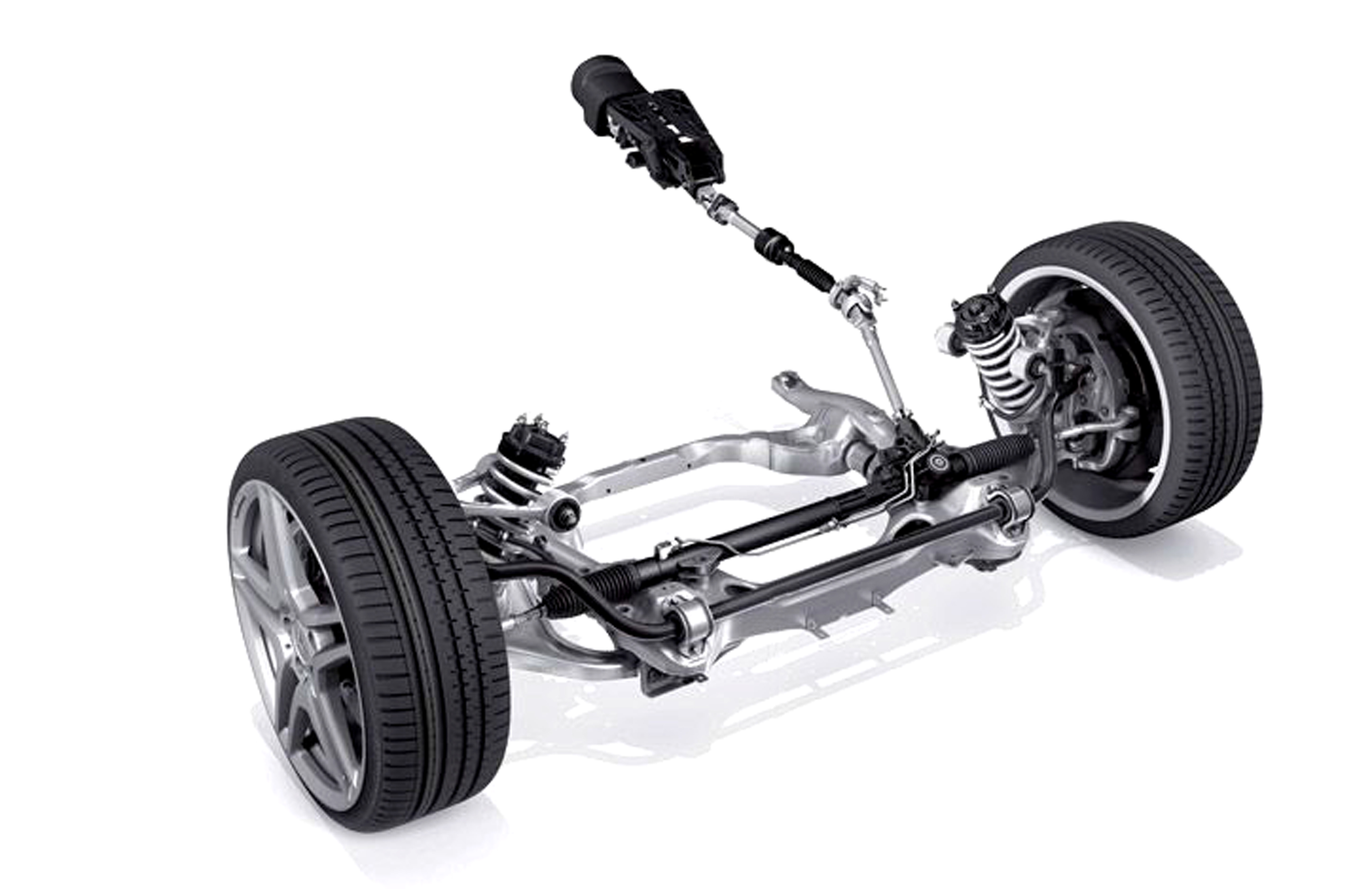
文:朱 超
四川工程职业技术学院
摘 要:进行转向器壳体的压铸工艺设计,为实现分型,共设置了 5 个滑块。 用 4 个内浇道充填主体、一个内浇道充填斜孔位,在产品各个成型远端设计溢流和排气槽。 抽芯机构内部设计冷却水道, 型腔均布点式冷却水孔,流道位置设置线式冷却水道,分流锥 / 浇口套采用冷却水道。 设计压铸模时,斜放产品、调整油缸位置,避免和压铸机干涉。 严格执行工艺规程,防止出现粗糙、修模痕、涂料脱落、损伤等铸造缺陷,成功地生产了 ADC12 转向器壳体。
关键词:压力铸造;转向器壳体;ADC12;铸造缺陷
图 1 是某压铸厂采用 800T 压铸机生产的乘用车转向器壳体,材质为 ADC12,大批量生产。 要求产品外观颜色光亮,组织致密,加工面不允许出现气缩孔,产品外表面不允许有冷隔,裂纹,缩陷等缺陷。压力铸造优点突出,但影响因素众多,铸造工作者需要认真进行工艺设计、铸型设计,制定操作规范等工作, 才能获得合格的压铸件以及高的工艺出品率。
1 工艺设计与压铸型设计
根据压铸机的参数,初步选择了压射压力和压射速度,进行了工艺设计与压铸型设计。
1.1 工艺设计要点
(1)选择分型面。 选择压铸件分型面时尽量通过铸件的最大截面之处,并且使铸件留在运动的半型内。 铸件相互尺寸精度要求高的部位放在同一半型内。考虑到产品出模和便于流道分布,本铸件选择的分型面为经过转向器轴线的与滑块移动方向平行的平面,见图 2 中的"PL"平面。
由图 2 可见,为实现分型,共设置了 5 个滑块:左右各 1 个,上方 2 个,侧方 1 个。 下方留有足够空间,以利布置浇注系统。
(2)设计浇注系统。 内浇道要使金属液进入方向和型腔排气方向一致,保持型腔排气系统畅通。根据需要设置溢流槽。内浇道的形式有中央浇口、侧浇口、切向浇口等。 横浇道有等宽、扇形、T 形、圆形、分支等型式。 横浇道与直浇道与内浇道过渡处横截面形状要平缓转换。
内浇道形状及流道设计。考虑到产品总长较长,产品致密度要求较高。 为了利于填充和产品补缩。 产品主体用 4 个内浇道。 另由于斜孔位要求很高,单独设置一个内浇道进行填充和补缩。 内浇道布置见图 3。
内浇道面积和宽度计算。 选用较低填充速度和填充时间计算,最终选内浇道面积约 500 mm
2,内浇道宽度取 2.5 mm。
(3)设计溢流、排气系统 。 在产品各个成型远端设计溢流和排气, 主要采用集中排气和单个排气相结合,以利型腔气体和前端冷料在填充时充分排出,保证产品质量。 排气系统见图 4。
(4) 设计冷却系统 。此产品壁厚,热量集中,特别是滑块成型部位是包裹铝液,所以,模具冷却系统的设计是关系产品质量和生产效率的重中之重, 采用了以下方式冷却:各抽芯型芯内部设计冷却水道、产品型腔均布设计点式冷却水孔、 流道位置设置线式冷却水道、分流锥、浇口套采用冷却水道。
1.2 压铸型设计
一个压铸型一般是由以下部分组成的: 型架部分、成形部分、浇注系统、抽芯机构、顶出铸件机构、排溢系统、导向零件、铸型冷却加热系统等。
(1)避免干涉。 铸件较长,较多孔位需抽芯直接成型, 模具外形 3 368 mm×1 366 mm×700 mm。800T 的压铸机大杠之间位置会与抽芯油缸相干涉。所以,在设计时采取斜放产品、调整油缸位置,避免和压铸机干涉。
(2)抽芯结构。 用抽芯机构来实现活动型芯在合型后的就位和开型。首先考虑型芯的抽拔力,然后确定抽芯机构形式。
考虑到滑块行程很长,且要保证滑块运动平稳,并且部分滑块有动作顺序要求, 故全部采用油缸抽芯结构。 保证在机床上能顺利实现动作顺序。 另外抽芯结构全部被铝液包围,属
于高热点,且产品壁厚较厚,抽芯的包紧力较大,故抽芯拔出力在设计计算需取大一些,特别是左、右长滑块更需要将安全系数放大。企业经过试生产,确定了工艺,成功生产了压铸件。 铸件的压铸模见图 5。
2 关键环节控制
该铸件生产节拍为 74 s。 浇注量 2.93 kg,填充量 1.86 kg, 零件质量为 1.58 kg, 材料利用率为54.0%。 在生产过程中,要求操作人员必须严格执行操作规程,遵守工艺纪律,按照《作业指导书》要求进行全检产品的外观,如有异常,应及时报告班长或检验员,决定是否可继续生产。
2.1 操作规程
(1) 严格交接班记录。 开机操作前必须点检设备,并做好登记。
(2)技术人员指导压铸工要严格按工艺操作,重点关注以下因素:喷涂料、金属液温度、压住模样温度、顶杆刷油、分型面清理、料饼厚度控制。
(3)按生产准备清单逐项检查、确认已经完成了准备工作。如涂料、螺栓、冷却水、喷雾机、给汤机等。
(4)用天燃气喷灯预热冷模具。 确保温度均匀,预热之后,需在模具表面涂分型剂,逐渐增大压铸机工作压力。
(5) 模具温度上升到规定值后 ,选择增压正常生产。
(6)正常生产 5~10 模后,将模具冷却水全部打开。
(7)对型腔局部拉伤和深腔部位,可适当进行手工补喷,并将型面、型腔水分吹干,对拉伤的型腔部位可适当少量均匀涂刷分型剂。
(8)必须注意观察打料油缸压力表、增压或快速蓄能器氮气压力。 一旦发现异常(如掉压、无压或压力不足等)应立即停机检修。 确认正常后方可继续生产。 生产的转向器壳体如图 6。
2.2 缺陷成因及防止
在生产过程中,压铸件出现了一些缺陷,组织技术人员分析原因并提出了防止对策。
(1)粗糙 。粗糙缺陷是指压铸件表面粗糙、凹凸不平,属于表面缺陷。 原因是修模时损坏模具表面、涂料过厚,在生产一段时间后脱落。 粗糙缺陷防止、解决措施是停机修模、严格涂料喷涂工艺。
(2)修模痕 。 修模痕指的是操作者在修模粘结在模具的金属块时所附带的修模痕迹, 导致生产的铸件表面外观受到影响。 原因是操作工在修理模具所使用的修模工具将非拉伤面划伤、 由于浇口腐蚀粘液,操作工在处理过程中将模具划伤。修模痕缺陷防止、解决措施是对模具喷砂处理。生产出来的产品能返修的返修,用砂纸及打磨工具进行返修。
(3)涂料脱落。 涂料脱落原因是操作工喷涂过程中掉涂料、当模具腐蚀修模后的部位很容易造成涂料积压、经常修模后导致模具氧化形成涂料脱落。 缺陷防止、解决措施是对掉涂料部位清理后补喷涂料。
(4)损伤 . 损伤是指铸件受机械撞击而破损、残缺不全的现象。 原因是产品铸造生产出来后在搬运或加工过程中没有对产品非加工进行有效保护。 解决措施: 生产过程中产品与产品之间要保持一定距离防止相互碰撞造成碰伤、 产品堆码时要使用胶垫对产品进行每层隔离。
3 结语
经过工艺设计与试生产,确定了铸件模具。 严格控制生产过程,成功实现了 ADC12 转向器壳体的压铸生产。 目前每月交货5 000 余件,全部一次合格。铸造操作者的操作水平和责任心在铸造缺陷形成中占据很大比例。 通过以上缺陷分析成因可以看出,很多压力铸造缺陷是由于操作不当引起的,所以严格控制工艺过程对防止压力铸件缺陷有重大意义。