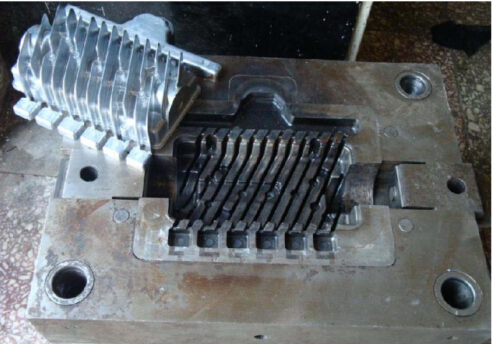
文:吴燕华
摘要:论述了压铸模结构对铸件质量及模具寿命的影响因素,并通过实例提出了通过改善模具结构来提高铸件质量和模具寿命的方法,可为压铸模设计者提供借鉴。
关键词:压铸模结构;铸件质量;模具寿命
1引言
压力铸造生产具有效率高、材料利用率高、铸件质量稳定等优点,再结合新材料的不断开发和应用,一些体积小、质量轻、形状复杂、壁薄等特点的有色金属铸件及配件越来越广泛地采用了压力铸造的方法进行生产。在压铸生产过程中,铸件的质量和压铸模具的使用寿命是生产者最关心的问题,而铸件的质量及模具的寿命跟很多因素有关系,本文从压铸模具结构上来阐述对这两者的影响。
2
压铸模结构对铸件质量的影响压铸模是压铸生产中的重要工艺装备,它对生产能否顺利进行,铸件质量的优劣起着极为重要的作用,它与压铸工艺、生产操作存在密切而又互相制约、互相影响的特殊关系。压铸模结构对铸件质量的影响主要体现在如下方面:
(1) 决定着铸件的形状和尺寸公差等级。
(2)其浇注系统(特别是浇口位置)决定了熔融金属的填充状况。
(3)溢流排气系统影响着熔融金属的溢渣排气条件,控制和调节压铸过程的热平衡,决定了铸件表面质量及变形程度。
(4)模具的结构会影响模具的刚度,模具的刚度限制了压射比压的最大限度,压射比压合适与否严重影响铸件的质量从而影响成品率及生产效率。
通常模具在设计时都会注重铸件的形状和尺寸精度,而浇注系统和溢流排气可以在模具试模后根据具体情况进行改进,以获得良好的表面质量和内在质量,在设计过程中,模具的强度和刚度往往是最容易被忽视的。比如一些抽芯滑块较大,铸件成型两侧都在滑块上,压铸模模框结构往往达不到压铸生产中承受铸造压力的强度,使滑块后移,铸件尺寸超差直至报废。以前常用的模具结构是模框(动、定)与座板分体式的,这种结构对于无滑块机构的模具是适用的,只需模具框及座板进行调质处理,就能获得所需的强度。但对于抽芯滑块,尤其滑块较大时,铸件侧面成型都在滑块上结构的模具强度就差得多。
比如,某公司高速弹力丝机关键铸件900-8225B筒管架座压铸模,老模具模框的结构是分体式的,而且滑块楔紧斜面,高度仅为滑块高度的1/4,定模模框楔紧块固定部分的深度仅50mm,锁紧斜面后端悬空,受力点都在50mm厚的定模框上,强度低,受力不平衡,滑块易拉毛、咬死。另外导流块未镶在模框内,易往外退,压射时铝液易喷出,使铸模型腔充填不足,铸件缺料。再者,压铸模在长期高压作用下,定模框楔紧块固定端由弹性变形逐渐转化为塑性变形,使滑块后退,铸件两端尺寸增大、超差,不符合图纸要求。

分析这些模具结构的原因造成的模具的强度、刚度差,在此基础上提出如下改进措施:
a.如图1所示,将动定模模框做整体式结构,以增加模框的刚度。
b.加大模框周边尺寸,使导流块做在模框内,不至于位移。
c.如图2所示,将滑块锁紧斜面高度改进前为滑块成型高度1/4,改进后需大于滑块成型高度1/2,使滑块锁紧力点平衡。
d.如图3所示,滑块导向槽采用GCr15淬火,镶于动模框内。
e.滑座采用T10钢调质处理。
改进后的动模框,强度大大增加,刚性好不易变形。滑块与滑槽材料采用不同的材料,且硬度也不同,亲和力变小,不易拉毛、咬死。定模框采用整体式后,锁紧机构与模框一体且高出分型面40mm,锁紧斜楔面高度为滑块成型高度的1/2,使滑块锁紧力点平衡,锁紧牢固。通过对该模具的结构进行改进后,生产至今近8万模,未出现滑块后退现象,铸件尺寸保持在图纸要求范围之内,且表面质量良好。
3压铸模结构对模具寿命的影响
3.1模架刚度对模具寿命的影响
压铸模的设计主要根据铸件形状而定。但模具设计和尺寸会对模具寿命有影响。首先,模架应有足够的刚度,有条件的话,尽量不用板式结构,而应用整体结构(见图4)。同样重量的材料,但模具刚度比板式结构好得多。其次,在动定模芯上增加凹凸作为工艺定位(见图5),从而消除上下模框导柱、导套配合的误差,消除压铸件因型腔错位而产生的废品,从而提高模具的使用寿命。
3.2浇注系统对模具寿命的影响
浇注系统设置得合理与否,对模具寿命影响较大。首先要避免注射时高速、高压金属液直接冲击、冲刷型芯。例如,一压铸模具在浇注系统改进前,金属液是通过内浇口进入型腔,直接冲击定模型芯的,因此产生很大的反作用力,阻挡后续金属液的流动方向,产生极大的流动阻力,从而使浇口处型腔容易磨损,产生疲劳裂纹,及加快该处腐蚀,最终导致整付模具失效而报废。改进后(见图6)在型腔与横浇道上方定模处增加一个圆弧过道,使金属液在此处改变流动方向,增加流动速度,从而使流动阻力大大降低,让金属液顺利充填型腔,
大大提高铸件的质量。
3.3冷却系统对模具寿命的影响
压铸模冷却系统的设置是必要的。经实践证明,加装冷却系统包括滑块、浇口套(见图7)也尽可能设置冷却装置有利于铸件质量的改善,及模具寿命的提高。模具温度在生产过程中对铸件的质量、生产效率具有重大影响,模温不均匀或不适当都会导致铸件尺寸不稳定、铸件顶出困难且易变形,产生热压力、粘模、表面冷隔等缺陷。 对于铝合金压铸,模具表面温度以150~250℃为宜,为了使模具达到该段温度,多数压铸厂采用瓦斯喷枪加热型腔或采用金属液低速充填型腔的方法来提高模具的温度,由于这两种方法都会导致型腔表面温度上升过快,而型块内部温度较低,因此产生了相应的内应力,模具容易产生微裂纹,既影响铸件的外观质量,又降低了模具的使用寿命。
目前,国内外著名压铸厂家在使用高精度模具生产高品质的铸件时,采用模温调节器,通过对导热油加热的方法,提高模具温度。当导热油不断流过模具内管道时,使模具的温度总体均匀地提高到适宜的温度,由于导热油还可以像水一样进行冷却,当模温超过设定值时,导热油开始起冷却作用,从而使模具温度能保持一定的范围内,通过采用模温调节器,可以保持模具温度的均匀性,提高铸件表面质量和模具使用寿命。
3.4溢流槽和排气槽的设置对模具寿命的影响
溢流槽与排气槽的设置。溢流槽(见图8)的位置尽可能置在:
①金属液最后填充的部位;
②遇有型芯阻碍而使金属液分为两股或两股以上时,应在型芯附近的部位;
③铸件壁厚过薄难以充填的部位,铸件壁厚过厚易产生缩孔和疏松的部位;
④型腔温度较低的部位;
⑤排气条件良的部位;
⑥金属液汇合处;
⑦浇口两侧或金属液不能直接填充的死角区域。排气槽一般与溢流槽设置相配合,设在溢流槽尾部以加强溢流和排气效果。有时,也可在型腔的必要部位单独设排气槽。可利用推杆配合间隙排气(配合间隙一般可采用H7/d8或H7/e8)。可利用型芯配合间隙排气,也可利用滑块配合间隙排气等。注意,排气槽表粗糙度要求要高,以防止金属液粘附于槽内从而堵塞排气槽。
4结束语
铸件的质量和压铸模的使用寿命是生产者最关心的问题,其影响因素也非常多并很复杂;但模具的结构无疑是对这两者影响最大、最直接的,这就需要模具设计技术人员在模具设计过程中要细致地、严谨地、广泛地考虑问题,并与时俱进,多吸收新技术和方法,来满足生产的需要。