文:谭家明 李小华
重庆宗申动力机械股份有限公司
摘 要:浇注系统对金属液在模内流动的方向与状态、排气溢流条件、模具的压力传递等起到重要的控制作用,并且能调节充填速度、充填时间和模具的温度分布等充填型腔的工艺条件。因此,浇注系统的设计是决定压铸件质量的重要因素,同时对生产效率、模具寿命等也有很大影响。设计浇注系统必须系统考虑,根据经典流体填充理论结合产品结构布置进浇和排溢。
关键词:直浇道;横浇道;内浇口截面积;填充速度;溢流槽;排气槽截面积
1 内浇口位置的设计
在浇注系统的设计中,内浇口的设计极为重要,在确定内浇口的位置之前要根据压铸件型腔的基本情况,分型面的不同类型,充分预计所选内浇口的位置对金属液充填型腔时流动状态的影响,分析充填过程中可能出现的死角区和裹气部位,以便布置适当的溢流和排气系统。应遵循以下几个原则:
(1)导入的金属液应首先充填型腔深处难以排气的部位,而不宜立即封住分型面造成排气不畅。
(2)应使流入型腔的金属液尽量减少曲折和迂回,避免产生过多的涡流,减少包裹气体。
(3)一般设置在压铸件的厚壁处,有利于金属液充满型腔后补缩流的压力传递。
(4)应考虑到减少金属液在型腔中的分流,防止分流的金属液在汇合处造成冷接痕或冷隔现象。
(5)应尽量避免金属液直冲型芯,减少动能损失,防止冲蚀和产生粘模,尤其应避免冲击细小型芯或螺纹型芯,防止产生弯曲和变形。
(6)凡精度要求较高、表面粗糙度值低且不加工的部位不宜布置内浇口,以防止去除浇口后留下痕迹。
(7)内浇口的设置应考虑模具温度场的分布,以便使型腔远端充填良好。
(8)还应考虑浇注系统的切除方法。
2 内浇口截面积的计算
内浇口一般是浇注系统中截面积最小、阻力最大的部位,它的截面积与该处的金属液流动速度的乘积和压室的截面积与压室中金属液流动速度的乘积相等,并且等于流经压室的金属液体积(型腔和溢流糟的体积之和)与所用时间之比。
即:
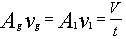

——内浇口的横截面积 m
2

——内浇口处金属液充填型腔的充填速度 m/s

——压室横截面积 m
2

——压射内金属液的流动速度 m/s

——型腔和溢流槽的体积 m
3

——充填时间
由上式得出:公式的前提是内浇口在其全面积内流速均等理想的充填速度

按下式计算:
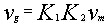
式中

——额定充填速度,常取 40m/s

——与压铸件壁厚有关的速度修正系数
(见下表)

——与作用于金属液上比压有关的速度
修正系数(见下表)
最佳的充填时间

按下式计算

式中

——额定充填时间,常取 0.06s

——与压铸合金物理性能有关的时间修正系数(铝合金取 0.9)

——与压铸件壁厚特征有关的时间修正系数(见下表)
从以上可得到内浇口横截面积的计算公式:
上图产品为例

=403796mm
3。

=1 ,

=0.8 ,

=0.9 ,

=1 ,

=40,

=0.06
3 横浇口设计
横浇道是金属液从直浇道末端流向内浇口之间的一段通道,其作用是将金属液引入内浇口,同时当压铸件冷却时用来补缩和传递静压力。
横浇口设计要点:
(1)横截面积从直浇道的末端起到内浇口止应逐渐缩小,否则横浇道中出现横截面积扩大,会使流过该处的金属液出现负压,由此必然会吸收分型面上的空气并增加金属液流动过程中的涡流。
(2)多型腔压铸模的一次横浇道截面积应大于各二次横浇道的截面积之和。
(3)横浇道截面积在任何情况下均应大于内浇口的截面积。
(4)为了减少金属流动阻力,达到均衡流速,横浇道不宜突然收缩与扩张。
(5)为了改善模具的热平衡条件,根据工艺需要,可以设置盲浇道,同时盲浇道兼有容纳冷污金属和气体的作用。
横浇道的截面积形状根据压铸件的结构特点而定,一般以扁梯形为主,横浇道的截面积一般比内浇口截面积大,以内浇口截面积

为基准数时,横浇道的截面积

。
4 溢流槽设计
溢流槽的作用:
(1)容纳最先进入型腔的冷污金属液和混入其中的气体与氧化夹杂,防止压铸件产生冷隔、气孔和夹渣。
(2)在选定浇注系统的情况下,溢流槽的设置可与浇注系统一起共同起到控制金属液流动状态的作用,防止局部产生涡流,造成有利于避免压铸件缺陷的充填条件。有时也用来转移缩孔、缩松、涡流包气和产生冷接痕的部位。
(3)调节模具的温度分布,改善模具的热平衡状态,尤其对薄壁或充填距离较长的压铸件,可以减少压铸件表面流痕、冷隔和充填不足现象。
(4)在某些情况下,溢流槽可作为压铸件脱模时推杆推出的位置,防止压铸件变形及避免压铸件表面留有推杆的痕迹。
(5)在压铸件对动、定模部分的包紧力接近相等时,为了防止压铸件留在定模,此时可在动模上设置溢流槽,增大压铸件对动模的包紧力,使分型时压铸件确保留于动模,便于推出机构的推出脱模。
(6)对于真空压铸和定向抽气压铸,溢流槽常常作为引出气体的起始点。
溢流槽的位置选择
溢流槽位置的选择应遵循如下的原则:
(1)溢流槽应开设在金属液最先冲击的部位,排除金属液流前头的气体和冷污金属液,稳定流态,减少涡流。
(2)溢流槽应开设在两股金属液流会合的地方,清除集中于该处的气体、冷污金属液和涂料残渣等。
(3)溢流槽应开设在内浇口两侧或金属液不能顺利充填的死角区域,起到引流充填的作用。
(4)溢流槽应开设在压铸件局部壁厚的地方,并且增大其容量和溢流口的厚度,以便将气体、夹渣和缩松转移到该处,改善压铸件厚壁处的质量。
(5)溢流槽应开设在金属液最晚充填的地方,以改善模具的热平衡状态和充填排气条件。
(6)在设计溢流槽时,还应注意溢流槽去除后不能影响或损坏压铸件的外观。
(7)不应在同一个溢流槽上开设几个溢流口,以免金属流从溢流糟流回型腔而产生倒流现象等。
5 排气槽的截面尺寸
排气槽截面积的计算公式如下:
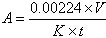
式中

——排气槽总的截面积

——型腔、溢流槽的容积之和

——排气时间,即等于充填时间

——排气槽开放系数。金属液充填分型面上的型腔时,容易先堵塞排气槽,

取 0.1-0.3;对于复杂多阶梯的型腔,金属液流速快,并在某些部位会发生二次喷射时,

取 0.3-0.5;复杂型腔转折又多,金属液流到排气槽时速度有所降低,

取 0.5-0.7;排气槽位于金属液最后充填的位置,且内浇口处充填速度较低时,

取 0.7-0.9。
当前国内压铸行业发展迅速,但设计开发要求的周期很短,模具设计人员也多是模具技工转行而来,设计方案差缺系统分析和校对计算,因而在后续的压铸生产中常常出现多次试模都不合格,或者产品合格率低、生产效率低下,模具寿命短。本文根据经典流体填充理论、铝合金材料特性并结合压铸生产实际情况,总结固化了关于模具进浇和排溢的相关注意事项和计算公式,供业内同行参考。