文:刘金保
摘要 用热分析方法和热传导原理,对压铸模用水冷控制模温进行了研究,总结出一整套模具冷却水孔的设计要领和计算公式,列举了计算实例。阐述了压铸模控制模温后对提高压铸件金属组织的致密度、压铸生产频率和延长模具寿命等起到的效果。
关键词:热传导 压铸模 水冷控制 模温
1控制模温的目的
合金在压型中的冷却速度是影响压铸件致密度的关键因素。在压射参数相同和保证合金液能充满型腔的前提下,模温越低则合金的冷却速度越快,铸件金属组织也就越致密。产品的不同结构和壁厚,对压型表面温度有不同的要求。我厂是生产汽车气制动阀的专业厂,阀类压铸件小而复杂,壁厚一般在4-8mm范围内,经多年摸索,这些产品的压型表面温度,铝合金为220一240℃时工作状态良好。在压铸生产过程中,只要压型能维持在这个温度范围内,就能获得优质铸件。在无冷却系统的压型中,随着压射次数的增加压型温度则不断上升,导致压型内部与表面温差不断减小,使合金在压型中的冷却速度越来越慢,得不到致密的金属组织,机加工后铸件会出现针孔甚至大的缩孔,更严重的是已加工的产品在做气密性试验时因漏气而大量报废。要获得高致密度铸件就必须控制模温,为此,对水冷控制模温技术开展了研究。
2模具冷却系统的设计原理
2.1模具的热分析
每次压射金属液时,压型表面温度急剧上升,紧接着由于热传导作用,压型内部温度也上升。压型内部如果没有冷却水及时将这些增加的热量带走,则下一个压射循环时压型内部温度梯度缩小。如此往返下去,温度梯度渐趋缩小,甚至压型心部与表面温度接近,形成一个较均匀的温度场,使合金在型腔中冷却得十分缓慢。
压型中的热分布受产品结构及模具壁厚等诸多因素的影响,是一个很复杂的问题。尽管热分布复杂,在整体模具其他冷却条件不变的前提下,热传导形式可归纳为两种基本类型。第一种类型——只与金属液接触不被金属液包容的压型,称为热放散型。压型从金属液得到热量后能迅速不断地向模具外形及空中传导和扩散;第二种类型——被金属液包容的压型,称为热集中型。这种压型从金属液获得的热量最多,而且又无法向周围的模具或空中传导和扩散。冷却系统设计的主要对象就是这部分压型。在设计压型的冷却系统时,首先要通过热分析,找出形成热集中型的那部分压型,然后根据金属液给与这部分压型的热量,计算出这部分压型冷却通道的表面积大小,最后根据模具结构确定通道的密封和出入口连接方式。
2.2冷却通道计算的基本公式
2.2.1压射金属液给与压型的热量计算
式中Q—单位时间压射给金属与压型的热量,kJ/h
P —每次压射金属液的质量,kg/n
N —单位时间的压射次数,n/h
C —合金比热(平均),kJ/C•kg
TC—浇注温度,℃
ts —铸件出模时的温度,℃
H—合金熔解潜热.kJ/kg
2.2.2冷却水应带走的热量
在单位时间里冷却水应带走的热量等于合金液给与压型的热量与自然散发热量(压型向空中散发和涂料带走的热量)之差。即
式中Q —单位时间冷却水带走的热量,kJ/h
Qn—单位时间合金液给与压型的热量血, kJ/h
Qn—单位时间自然散发的热量,kJ/h
Qn值与压射生产频率、环境温度、涂料喷涂量等因素有关。在我厂生产条件下其平均值

,因此:
前面已叙述,冷却通道设计的主要对象是热集中型的压型。形成这部分铸件形状是由两部分压型组成的,即被金属液包容和不被金属液包容的压型。经过几年的摸索和验证,前者为得到冷却水应带走热量的

,后者仅为

。因此在计算热集中型压型得到的热量

时,在式(3)前者面应冠入

这样一个经验系数,即是

,由式(1)(2) (3)得:

2.2.3压型表面到冷却水孔表面的距离计算
为了维持压型表面合适的工作温度,在每一个压射循环内金属液给与压型多余的热量应正好由冷却水带走,就要确定压型表面至冷却水孔表面的距离。由热传导公式可求得其距离,现作如下推导。
l)平壁类热传导公式

(5)
中

—平壁类压型表面至冷却水孔距离,m

—导热系数,模具钢为168kJ/ (m•h•℃)
S —压型受热面积,m2

—压型表面理想工作温度,铝合金 =220-240℃

—离压型表面 处的压型温度,℃
Qm—每小时冷却水应带走的热量,kJ/h
(2)圆筒类热传导公式
热集中型
热放散型
式中

—热集中型时,压型表面至冷却通道表面的距离,m

—热放散型时,压型表面至冷却通道表面的距离,m

—平壁类压型表面至冷却通道表面的距离,m
R—圆筒类铸件的半径,m
2.2.4冷却通道表面积计算公式
式中Q
m—冷却水从压型中应带走的热量,kJ/h(热集中型时为

)
A —冷却通道表面积,m2
h—冷却水入、出口平均温差下的传热系数,(kJ/m2•h•C)
t2—冷却通道周围压型温度,℃
t
3 —冷却水入、出口温差,℃
2.2.5冷却水传热系数 值的确定
h值受冷却水入出口温差、流量、通道大小等因素的影响,计算十分复杂。1969年国际锌压铸会议确定了 值的经验计算公式:
式中W —冷却水流速,m/s
D —冷却水孔通道直径,m
b—冷却水入、出口平均温差下水温常数(表l)

3 应用举例
了简明起见,用图1 所示的最简单压铸件为例。该件要求加工后在1MPa气压下无泄漏。在合模力1300kN压铸机上生产。压铸合金为A380.0铝合金。
3.1 A380.0合金特性及压铸工艺设定
合金密度

,平均比热

,熔解潜热
每小时压射次数 N=100 n/h,浇注温度

,铸件出模时的温度

,压型表面理想温度

,冷却通道压型温度

,冷却水出入口平均温差

(出口80℃,入口循环水水温20℃),水的流速

。
3.2热分析
从图一可知:形成φ16mm, φ50mm,φ34.7mm, φ9mm孔的型芯为被金属液包容的压型即热集中型,其余为热放散型。其中φ9mm型芯太小通水困难,因此该产品模具只对φ16mm, φ50mm, φ34.7mm型芯设计冷却通道(见图2、图3)。
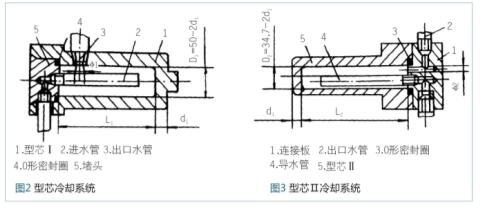
3.3计算
设型芯1这部分铸件的一次压射合金液质量为 ,型芯1与金属液接触的表面积为 、,其表面到冷却通道表面的距离为 ,冷却通道孔径为 ,冷却通道最小长度为 。设型芯II的相应量为

。
计算过程略
计算结果:
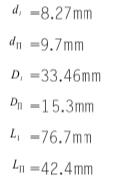
这样己完全确定了型芯1、II的冷却通道最小长度,分别为: φ33.46mm×76.7mm, φ15.3mm×42.4mm。冷却系统结构见图2、图3。
关于冷却水出口孔径的计算:不管进入冷却通道的孔径是多大,只要出水孔的大小额定了,在水流速度相同时,冷却通道的水流量也就额定了,出水口即为节流口。分别设型芯I、型芯φ的孔径为娇

。
由热力学公式

和质量与流量的关系式

得
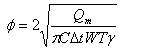
式中

—出水口(节流口)孔径,m

—lh内由冷却水带走的热量,kJ(对热集中型为

)

—水的比热,


—水的出入口温差即为式(8)的t
3,℃
W—水的流速,m/s

—水的密度,

对于型芯1,节流孔径φ1为:
φ1=5.7mm
φ2=3mm
(计算过程缩略)
我们备有带冷却塔的循环水池,水压、流速、水温都较稳定。必须指出,图2的件2、图3的件4一定要伸入成形段的最前端,否则达不到预期的冷却效果,这是为了低温水强行通过高温区而设置的导水管。
4控制模温后产生的效果
4.1提高了压铸件的致密度
加工后均须在1-2.5MaP气压下作气密性试验。未进行模温控制之前,经真空浸渗处理后,铝压铸件漏气率为40%一50%。水冷控制模温后提高了铸件致密度,铝压铸件的漏气率均已降到5%以下。
4.2提高了劳动生产率
未控制模温前,由于压铸生产时模温不断上升,有的模温可高达30O℃以上,为了维护正常生产,避免粘模拉模和铸件顶出不变形,只得放慢压铸生产频率。控制模温后生产频率大幅提高。
5.3提高了模具寿命
我们担心压型模壁减薄了易开裂。几年使用的结果表明:同样的压型材料和热处理,模具寿命可提高1.5倍以上。这是因为缩小了模具温差和降低了模温,防止了较大热变应力产生的缘故。
4.4减少了涂料用量
模温控制后由于铸件表层组织致密,改善了脱模效果,不易粘模,可以少上或不上压铸涂料。