文:唐建敏
摘 要:高压压铸模具的温度控制一直是压铸行业难以解决的一大难题模具温度对产品的内部质量有着至关重要的影响。随着社会的发展,人们对产品质量的要求越来越高,常规的检测方法已经无法满足产品质量的稳定要求。
本文通过防水热电偶与 TP700-16/TP700-40 多路温度测试仪相结合,研发出一套能对模具温度进行实时监控的装置。
经实际应用证明此装置能够及时发现模具温度异常,提高压铸生产的稳定性,有效改善产品质量,大幅度降低废品率。
关键词 高压铸造 模具温度 实时温度
汽车变速器外壳结构复杂, 进行高压铸造时由于模具温度不能精确检测和控制,导致废品率较高,高达 30%,严重影响到企业的正常生产和经济效益。 因此,为了降低废品率,充分掌握变速箱体温度场变化是企业和研究者共同关注的问题。 汽车变速箱体外壳实物如图 1 所示。
1 主要仪器设备
图 2 为热电偶探头和传感线。 在模具相应部位加工热电偶安装位置, 热电偶测点与模具型腔表面相距 25 mm(保证模具冲刷强度),探头与测温点接触无间隙 。
热电偶通过传感线联接到TP700-16/TP700-40 多路温度测试仪(图 3),并对温度数据进行储存。TP700-16/TP700-40 多路温度测试仪有两种温度显示方式,第一种是数字显示,能直观地显示出每秒钟的温度情况;第二种是曲线形式显示,可以和模具运动状态相结合,形象地表达出压铸在某个状态下对应的温度情况。
2 工作原理
图 4 为温度检测系统的工作原理图。 热电偶固定在螺纹套筒上,通过螺纹联接到模具上,且保证热电偶探头刚好与模具测温点表面接触;热电偶补偿馈线集中在防水快插芯上,模具段端选用公头,在防水快插芯封壳上标记编号以区分检测位置点, 在与温度记录仪联接的母头插芯上面标记对应编号。
当热电偶感应温度后以电波的形式通过补偿馈线传输到温度仪,温度仪接收到信号后处理成数字显示,记录出该点的温度情况, 同时当温度高于或低于设置温度时将反馈给报警装置。
热电偶探头与模具的接触点离型腔表面有 25 mm 的距离, 有一定的温度差,因此,采用另一个热电偶在压铸后直接接触该点成型表面检测出温度或者用手持红外线测温仪拍摄温度, 与温度记录仪显示的温度进行对比, 温差在20~ 30℃ 之间。 因此,在显示仪上设置温度补偿25℃ ,则显示的温度十分接近真实值。
3 试验与分析
3.1 测点位置选定
通过大量试验, 并总结汽车发动机外壳在前期生产中的情况,得出定模在点 10、
11、12 处的温度需要重点监测,如图 5 所示。
3.2 仪表端连接线图
图 6 为仪表端连接线图。如图所示,标识 1 为动模插头,标识 2 为定模插头,连接时要特别注意其方向。 将热电偶馈线穿入不锈钢波纹管内, 对应序号1~ 9 的馈线接入到标识 3 插头的 1~ 9, 对应序号10~ 12 的馈线接入到标识 4 插头的 10~ 12,同时注意其正负极。
3.3 终端显示结果
图 7 所示面板显示各点温度, 其中定模 CH10点温度显示为 182.89℃ ,CH11点 温 度 显 示 为209.80℃ ,CH12 点温度显示为 148.80℃ 。
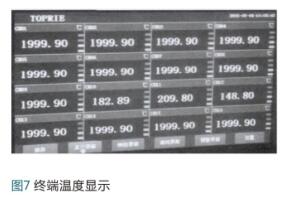
#p#分页标题#e#
3.4 准确性验证
图 8 为红外线的测温结果。 图 9 为红外线测温与温度检测系统的温度测量值对比。由图 9 可知,对热电偶测温进行补偿后, 热电偶测量的温度与热成像仪拍摄的温度十分接近, 它真实地反映了模具的温度变化过程。由于热成像仪需要暂停压铸进行拍摄图片,每次需要大概 5min, 因此用热电偶监控模具温度避免了停机时间的浪费成功地提高了设的利用率,OEE(设备综合效率)提高了 2.5%。
由于热电偶实时监控模具温度, 当模具温度不达标时马上报警提醒工作人员, 有效地避免了在压铸期间无法及时发现模具温度问题, 有效地保证了压铸的稳定性。从实际生产统计数据看,压铸件内废品率降低了 4.4%,外废品率降低了 5.1%,从而有效地提高了产品的合格率,降低了生产的成本。
4 结语
(1)此温度测量技术提高了设备的利用率,减少了停机时间,提高了 OEE。
(2)研发的压铸模具实时温度监控装置能够及时发现模具温度异常,提高了压铸生产的稳定性;能有效改善产品质量,大幅度降低废品率。为进一步提高温控系统的精确度, 今后可从以下方面问题考虑并解决:
(1)模具装配孔加工问题:
热电偶和模具采用螺纹联接。 在加工时螺纹精度不够、孔位偏差大,会影响热电偶的装配精度,无法准确地采集到该点的温度。
(2)热电偶的质量问题:
在正常状态下,热电偶必须与模具检测点接触且离检测点越近检测的温度越精确,
但国内的热电偶无法实现精度要求,热电偶的检测灵敏性低。