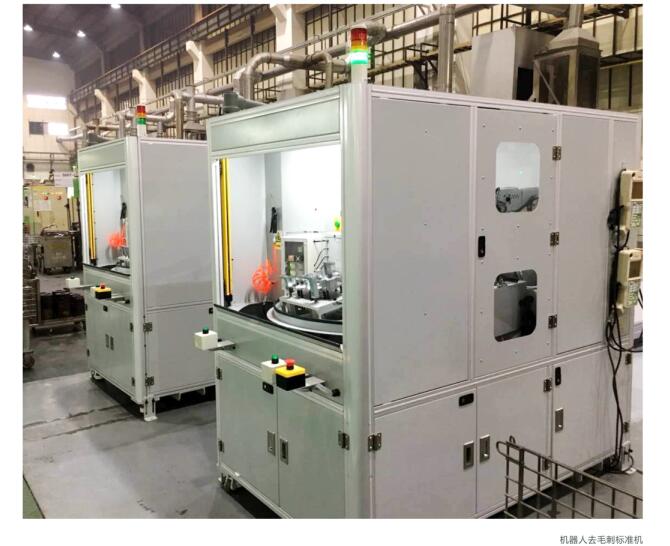
广州太威机械有限公司 陈月军
摘要
在压铸成型中,零件成型同时,也产生不同程度的毛刺,尽管压铸和模具技术的不断进步,毛刺在减少却不能避免。一般在进行加工处理前需要进行去除毛刺作业,然而去毛刺的工作繁琐,耗费大量人力成本。在人力成本不断上升,招工难的大环境下,自动化设备去除毛刺成为一种趋势。利用机器人进行去除毛刺作业更是一种高效的方法。本文由此展开对机器人去毛刺的优势进行分析、对机器人去毛刺中浮动技术的应用进行研究。
机器人去毛刺的优势
对于压铸成型产生的毛刺,目前去毛刺的方法主要有人工去毛刺、专用机去毛刺、3轴机床去毛刺、机器人去毛刺。其中人工去毛刺占了比较大比重,人工去毛刺结合电动工具、气动工具是比较主流的方案。但人工去毛刺存在劳动强度大,动作重复和需要比较大的力气,工具产生的震动和噪声对工人的健康造成影响。同时还存在工作环境差,加工质不稳定,生产效率较低的缺点。所以目前稍有规模的企业也在寻求自动化去毛刺的设备。
专用机处毛刺是根据每一款工件具体结构来设计的设备。一般结构简单,毛刺比较集中在某个位置的工件可以采用这种方式。因为去毛刺的机构都是量身定做设计,很难做到同时对应多种类的工件,工件发生变化也需要投入比较大的成本进行改造。不具有柔性化,较难推广应用。
3轴机床或者CNC进行去毛刺的方案,与专用机去毛刺方案对比,具有柔性化,更换工件的工装治具,就能导入新的产品。但也有它的局限性,这样的机床所能对用工件必须是一个方向的毛刺,机床机构决定了只能对应结构的简单工件。对于复杂的工件。对于多个面,多角度的毛刺,这样的方案显得束手无策,非常有局限性。
近年来越来越多使用机器人去毛刺的方案。机器人去毛刺的方案一般有两种模式,一是机器人装载加工主轴,工件固定,二是机器人抓取工件,加工主轴固定,两种方式都是目前比较主流的方案。机器人去毛刺方案一般采用6轴机器人,结合去毛刺主轴。6轴机器人优势是运动速度高、运动灵活,在工作范围内,可以进行任意角度、姿态加工。对于复杂结构的工件、毛刺分布分散的工件也能对应。而且机器人具有可编程性,新的产品导入只需要更换工装治具,程序切换就能完成。这使设备具有更高的柔性化,更适合目前企业的需求。同时机器人去毛刺的方案能减少工人劳动强度或直接省去工人,有效保证加工品质一致性,提高整体生产效率,改善工厂工作环境。这些优势都是显著的,纵使设备投入成本略高,也越来越多被企业接受。
浮动去毛刺技术
在去毛刺加工中,决定去毛刺效果的因素有刀具、主轴转速、切屑速度、机器人轨迹四个方面。其中机器人轨迹是一个比较主要的因素。机器人轨迹路径决定了加工的路径,机器人的重复定位精度我们毋庸置疑,但在编程时,机器人的点位一般通过示教来完成,示教式通过人工确认位置,这样就会使点位存在误差,就会导致切屑效果不均匀。同时一般压铸成型的工件外尺寸存在误差,固定的切削路径也会导致切削效果不均匀。过切或者切不到的情况是无法避免的。这也是目前很多机器人去毛刺设备去毛刺效果不好或者失败的原因。
针对这样的情况,浮动去毛刺的技术的应用是一个很好的解决方法。浮动的方法一般有两种,利用力传感器进行浮动加工和利用浮动式工具进行浮动加工。利用力传感器的原理是在机器人末端和工具之间加入力传感器,通过传感器反馈末端受力信号到机器人控制器,机器人控制器通过算法来校正机器人的运动,从而保证加工时候的接触力保持在一定的范围。这样的方案具有通用性高,但控制系统上比较复杂,成本也比较高,而且力反馈具有滞后性,机器人加工的速度将会受到限制,无法达到高效加工。
采用浮动式工具的方式是机械式顺应的结构,控制系统上不需要传感器,在响应上更加迅速,机器人加工的速度可以大大提升。浮动式工具加工的主轴就不是固定的,而是可以浮动的,具有顺应性。刀具和工件的接触式柔性的,浮动装置介入后机器人轨迹对去毛刺的影响将会变小,在一定范围内浮动将会弥补机器人轨迹。这样对机器人轨迹的精度要求就会降低,使得机器人编程变得简单,便利。
浮动工具的原理和功能
浮动工具一般是利用压缩空气进行浮动调整。以日本FINE TECHNO品牌的AF40浮动刀柄为例。刀柄中空部位安装去毛刺的主轴,主轴能在轴向方向上有最大5mm浮动量,径向方向上最大5度的浮动角度。浮动刀柄中有提供浮动力的气室,通过调整气室的压力,可以该表浮动力的大小。浮动压力不改变时,在浮动范围内,浮动力基本保持恒定,这是一个非常重要的特性。浮动的恒定这是保证切削量均匀的重要因素。所以气压式浮动比一般弹簧浮动的装置性能好的原因。
浮动去毛刺的优势
吸收偏差。压铸成型后的工件存在尺寸误差,工装治具也存在定位误差,这些误差是无法避免的。介入浮动功能后,加工轨迹编程时,通过刀具预压入的方式,浮动装置可以保持浮动力恒定。这样工件产生偏差是通过浮动可以吸收的,在一定的偏差范围内浮动装置可以令刀具和工件保持贴合,刀具和工件之间的接触力也保持恒定。与刚性连接的工具相比,能有效防止过切和切不到的情况,确保加工品质的一致性。
自动跟随轮廓。对于一些压铸或者锻造成型经过CNC加工后的零件,产生的翻边毛刺,直接用CNC去除这些毛刺是比较困难的。因为这些毛刺产生在加工面和成型面之间,这些轮廓有较大的不一致性。这时候使用浮动式去毛刺的方法就可以很好解决这些问题,尽管轮廓不一致,浮动装置保证了刀具了和工件的浮动力,切屑是具有顺应性,能跟随轮廓进行加工,切削量也比较均匀。
小毛刺和水口可一次性加工。一般来说压铸成型后的毛刺分布在模具结合面,和水口部,合缝线的毛刺比较小,水口部厚大比较厚,这样的情况想一次性切削很困难。但利用浮动装置浮动力可调整的功能,可以通过机器人实时控制浮动力的大小,水口部位置时切换较大的浮动力,合缝线部位切换较小的浮动力。通过调整浮动力达到改变切削量的目的,这样也大大减少了对机器人轨迹的依赖。例如,在进行倒角加工的时候,机器人轨迹程序已经编写完成,由于工艺要求需要调整倒角的大小,这种改变并不需要重新编写机器人的运动轨迹,只需要调整浮动力的大小就可以调整切削量。当浮动力增大时,切削量增大,倒角变大;当浮动力变小时,切削量减少,倒角变小。这样的条件变更,远远比编写机器人的轨迹容易,很大程度上简化调试的难度。
结语
利用机器人去毛刺是去毛刺领域自动化中比较好的方案。减少工人劳动强度,较少作业工人,保证加工品质一致性,提高整体生产效率,改善工厂工作环境。6轴机器人具有灵活性,复杂零件的加工也能对应。为产品换型,新产品导入也提供了便利性,具有极高的柔性化。在机器人去毛刺应用中,浮动工具的介入是关键的技术,浮动工具的利用使机器人去毛刺的应用更加稳定和便利。
机器人去毛刺技术上已经日益成熟。这样的设备可以进行模块化和标准化,设计成标准机的形式,有标准机设备床身,标准的工作台,标准的浮动主轴工具。根据工件尺寸,毛刺的大小和位置,选用不同的标准模块,可以很快做出相应的解决方案。机器人去毛刺标准机也可以变成像CNC加工中心一样的通用化设备,标准机化的去毛刺机也可以大大降低成本,使设备成本回收期更短,这些特出的优势,机器人去毛刺的自动化设备将获得更好的推广。