文:重庆长安汽车股份有限公司工艺技术部 李帅 、侯安顺、 李莉 、马薇
摘 要:压铸模具在整个压铸生产中占有举足轻重的地位,其中浇注系统设计又是压铸模具设计的关键,本文试从工艺角度分析缸体压铸模具浇注系统设计对压铸生产质量、成本、效率的影响。
关键词:压铸模具 浇注系统
1 导言
发动机缸体在目前国内大型压铸件市场上占有相当的比例,其产品结构及压铸工艺具备一定的代表性,是一类典型的复杂的大型箱体压铸件;压铸模具在整个压铸生产中占有重要地位,是整个压铸工艺设计的核心,实际生产中约有70%的工艺问题与模具直接相关;毫无疑问,在压铸模具设计中浇注系统的设计对压铸生产的影响是决定性的,本文我们从工艺角度分析缸体压铸模具浇注系统设计对压铸生产质量、成本、效率的影响,最终尝试给出浇注系统设计的基本思路。
2 现行模具设计的弊端
对于传统压铸厂而言,通常不具备大型压铸模具的设计、制作能力,缸体压铸模具一般委外制作,往往压铸模具厂对压铸工艺的理解程度远低于压铸厂,同时不熟悉压铸模具的实际使用工况,这就造成了压铸模具设计与实际压铸生产的脱节。这一现象在目前国内压铸行业是普遍存在的,必须通过深入的技术沟通和协同设计来改善,一方面模具设计人员需要深入了解压铸模具生产工况(即买方的工艺现状)和铸件质量要求,另一方面压铸厂需要介入模具设计过程,尽可能完整并准确地表达出工艺限制条件。
3 模具浇注系统设计的流程
3.1 产品数据确认
这一阶段主要是对铸件数据的检查与确认,评估铸件制造性风险,详细了解铸件质量要求,优化允许修改的产品细节,这个时候应当开始考虑浇注系统的布置,这个时候建议完成一轮CAE 凝固分析,帮助确定质量风险点;
3.2 浇注系统布置
铸件数据冻结后,模具设计正式开始,这个时候需要确定采用浇注系统的类型以及布置方向。对于缸体压铸件,浇注系统主要分为单边进浇与双边进浇两类,一般将浇口放置在缸体结构较复杂、质量要求较高的一侧;完成浇注系统的整体布置后,就基本可以完成模具分型的确认。
3.3 浇注系统设计
根据铸件体积,反求内浇口面积,在曲轴室壁上侧布置内浇口,根据局部体积分布分割内浇口比例;根据各部分内浇口流量,计算各段横浇道截面积;最后根据压室充满度结合冲头速度计算料饼体积,完成浇注系统初步设计,作为后续设计工作的原点。
3.4 模流模拟分析
将初步设计的浇注系统输入CAE 系统进行填充分析,根据模流分析结果判断浇注系统设计的合理性,并调整浇注系统设计,此时开始排溢系统的设计;不断重复以上过程,使整个流态达到理想状态,最终得到理想的浇注系统。
4 主要设计因子
模具浇注系统设计与产品结构、模具使用工况密切相关,只有对这两点做到了深刻理解,才能设计出优良的浇注系统。浇注系统所解决的充型问题本质上是流量问题,浇注系统的设计简单的说就是回答如下三个问题:
1) 铝液从何部位进入铸件—选择什么类型的浇注系统、浇注系统布置在铸件的什么位置;
2) 铝液的速度是多少—冲头速度有多快、内浇口速度有多快;
3) 铝液通过的截面积多大—浇注系统各部分截面积是多少,料饼直径选多大;
浇注系统的整体结构如图 1 所示(以双边进浇式浇注系统为例),下面我们详细分析各详细设计因子:
4.1 浇注系统类型
浇注系统主要分为单边进浇和双边进浇两大类,其对实际压铸生产质量、成本和效率影响很大,如表 1 所示;应结合铸件的具体结构特点进行布置,对于高度较高或是两侧悬挂面均有高压油道的缸体,应充分评估其填充难度,优先考虑采用双边进浇方式,产品质量相对好保证;对于要求不高、结构不复杂的缸体优先考虑单边进浇,以节约成本。
4.2 浇注系统布置
首先识别缸体产品的质量关重部位,优先考虑布置将浇口在质量部位(如高压油道所在一侧),其次考虑充型的顺畅性,浇口附近位置应注意型芯对充型的影响,浇口附近的型芯不仅易弯曲折断,而且不利于前期铝液填充和后期增压压力压力传递。着重需要指出的一点是,对于缸体产品,在结构上曲轴室上方是最常见的内浇口布置位置,应尽可能避免铝水对模具滑块的直接冲击,该冲击不仅带来紊流卷气和填充能量的损耗,更带来对模具滑块的冲击损耗,模具寿命缩短,生产成本增高。
4.3 内浇口速度
内浇口速度对铸件的充填效果有着至关重要的影响,实际压铸生产中内浇口速度应控制在30m/s-50m/s,过快将引发严重的溅射紊流及模具成型滑块冲刷问题,过慢则带来填充时间过长,增加铸件冷隔风险;对于缸体压铸模具,设计浇 注系统时推荐将内浇口速度设置为35m/s-45m/s,以保证在实际生产中仍有调整空间。
4.4 内浇口宽度
对于一般缸体铸件 70ms-100ms 内将完成铸件填充,填充时间过短将带来能量消耗,对设备、模具消耗较大,无形中提高了生产成本,填充时间过长将带来远端冷隔等充型不良的质量风险;由于某一铸件的体积是一定的,可根据如下公式反求出总的内浇口面积。
其中:S-内浇口面积,
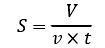
V-铸件总体积(含浇铸及排溢系统),
v-内浇口速度,
t-填充时间
得到内浇口面积的计算结果后,即开始内浇口布置,对于缸体铸件需要注意的是内浇口的宽度的限制要多于长度的限制,内浇口宽度除了取决于内浇口面积,还取决于曲轴室壁厚,其不宜超过曲轴室壁厚的 1.3 倍,以规避严重的铝液溅射。
4.5 横浇道截面
基于成本考虑,不希望横浇道截面过大,以提高铝合金材料利用率;但是从产品质量要求出发,横浇道设计应考虑铝液的流量必须足够,原则上横浇道任意段截面积应大于后端任意分支浇道截面积之和,以避免浇道内的卷气问题。另外,需要提出的是,横浇道应具有一定的厚度以起到保温的作用,避免在压型过程中下方的直浇道及内浇口过早冷却,影响压型后期的增压效果,这一点需要在凝固模拟分析中确认,浇口凝固断开时间至少要大于 3s。
4.6 料饼直径
通常料饼的直径取决于采用的压室直径,对于某一铸件生产过程,给料体积是一定的,压室长度往往受到设备限制,调整范围有限,因而压室直径是压室充满度的重要影响因素;充满度过低,压室内部原有气体过多,可能导致卷气,充满度过高,压室的液面面积过小,易引起慢压射过程中的紊流,引发卷气问题(见图 3),我们推荐设计采用的压室充满度为 45%-55%;另外需要注意的是,确认料饼直径时,需要考虑设备的增压能力,料饼直径越大大,设备能够达到的增压上限就越低,工艺调整范围就越小,一般来说缸体压铸生产中增压上限是 90MPa。
压室填充率—60%,冲头速度—0.3m/s,压室长度—1000mm,浇注温度—670℃。
4.7 其他
上面介绍的是浇注系统中主要的设计因子,浇注系统设计还包括局部几何形状的调整,比如直浇道进浇角度、分流锥的具体几何形状等,具体需要进行结合模流模拟分析进行优化调整。
5 小结
模具浇注系统设计是工艺设计工作中的重点,其设计水平将关系到后期量产的质量、成本、效率的实现,优秀的浇注系统一定是模具厂与压铸厂共同努力的结果,本文站在压铸厂的角度对缸体压铸模具浇注系统的设计进行了简要分析,初步提出了浇注系统主要设计因子的设计建议,这些当然是远远不足的,追求高质高效的压铸生产显然是我们共同的目。