文:陈 宇
重庆隆鑫压铸有限公司
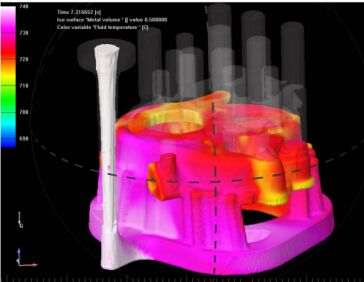
摘 要:如何提高压铸铝合金模具的寿命一直是人们关心的问题,使压铸铝合金模具的使用寿命缩短的失效形式很多,但其主要的失效形式为热疲劳裂纹,即热裂。本文就这个问题进行了分析,导致铝合金压铸模具出现热裂的因素很多,如模具材料、模具设计、热处理状态及工作环境等,就对这些情况提出了相应的改善措施。
关键词:压铸;模具;寿命;热裂
前言
结合我们公司的生产情况来对压铸铝合金模具的情况进行分析,压铸模具主要选择的材料是H13(4Cr5MoSiV1)。H13钢是一种新型热作模具钢,其化学成分处于共析点附近,锻造后经球化退火,组织为球状珠光体和少量碳化物,1000~1050℃淬火后组织为针状马氏体,它具有高的韧性,良好的冷热疲劳性能,与熔融金属相互作用小,且价格便宜,因此广泛应用于铝合金的压铸模具。在国内H13钢已于20世纪90年代初批量生产投放市场, 取得了较好的效果。H13钢的主要成分(%)如下表:
其化学成分特点:①WC为0.32%~0.45%,以保证高硬度、高韧性和较高的热疲劳抗力;②加入较多提高淬透性的元素Cr、Mn、Si,Mn 可以改变钢在凝固时所形成的氧化物的性质和形状,避免硫在晶界上形成低熔点的FeS,而以具有一定塑性的MnS存在,从而消除硫的有害影响,改善H13钢的热加工性能,Cr和Si可以提高耐回火性;③加入产生二次硬化的元素Mo、V,Mo、V能防止第二类回火脆性,提高耐回火性。H13钢是目前世界上用量最大的二次硬化型铝压铸模具钢,90%以上的压铸型腔模都是由H13钢制造,由于H13钢是相当成熟的压铸模具钢,通过提高冶炼质量可进一步改进性能,但是H13钢在工作时承受很大的冲击载荷、强烈的摩擦、剧烈的冷热循环引起的热应力以及高温氧化,常出现热裂、塌陷、磨损和崩裂等失效形式,其中热裂是最重要的失效形式,如何防止这种缺陷是本文研究的重点。
1 热裂产生的原因及对模具的影响
1.1 热裂的形态
热裂是模具最常见的失效形式,如图1.1所示:
1.2 热裂的定义
热裂是模具最常见的失效形式。热裂纹通常形成于模具型腔表面或内部热应力集中处,当裂纹形成后,应力重新分布,裂纹发展到一定长度时,由于塑性应变而产生应力松弛使裂纹停止扩展,随着循环次数的增加,裂纹尖端附近出现一些小空洞并逐渐形成微裂纹,与开始形成的主裂纹合并,裂纹继续扩展,最后裂纹间相互连接形成网络状裂纹而导致模具失效。热裂主要是材料热应力疲劳所引起,即材料在热应力的作用下,由于经受反复或脉动应变而产生的一种连续的、局部的、永久性的组织变化。与热裂相对应的最重要的材料性能是材料的抗热疲劳性。迄今为止,衡量材料抗热疲劳性能的标准尚未统一。因此,如何用常规力学性能来反映抗热疲劳性能就显得较为重要。有资料表明,与抗热疲劳性能有关的最重要的力学性能是材料的强度,另一种观点则更倾向于材料的韧性。从热疲劳试验结果分析,铝压铸模具的热疲劳裂纹中存在疲劳辉纹,并以弹性应变为主,而且多数模具的使用寿命在104~105次以上,具有高周疲劳的特性。根据疲劳强度理论,强度高的材料更能适应长周期的弹性应变,在这种情况下,抗热疲劳性能与强度的联系更为紧密。但是,如果型腔表面的工作温度偏高( 如压铸铜及铁基合金等) 或因其他因素使模具产生过大的热应力,从而使应变幅度大大超过材料的弹性应变范围,应变则以塑性应变为主,具有低周疲劳特性。此时韧性高的材料具有更大的优势。因此考核材料的热疲劳性能时,应注意区分材料的疲劳形式,并据此确定模具合适的强韧性配合。
1.3 热裂产生的原因
(1)模具材料的影响,模具钢的晶界无共晶碳化物夹杂,大块状的共晶碳化物和杂质强度极小,不能抵抗热疲劳,降低了钢材的塑性,是热裂发生的起源点,同时模具组织存在的成分偏析导致在相同奥氏体化温度下, 淬火后得到的马氏体组织粗细不均匀,这也是产热裂的原因之一;
(2)模具的设计的影响,过小的圆角半径、壁厚差悬殊的扁宽薄壁截面,以及孔、槽位置不合适等,很容易在模具热处理和使用过程中引起过大的应力集中而萌生裂纹,同时冷却系统设计不合理,会使模具的冷却不均匀产生热应力,导致热裂的产生;
(3)模具的制造的影响,制造模具的一般选用机械加工和电火花加工,机械加工的表面粗糙度对模具热疲劳性能有很大影响,模具型腔表面应获得较低的表面粗糙度值,不能留有刀痕、划伤和毛刺,这些缺陷会引起应力集中,诱发热疲劳裂纹萌;电火花加工后的型腔表面会产生出一个变质层,这一层的化学成分、金相组织、力学性能(强度、硬度、韧性)等都发生了改变,变质层又硬又脆,并有应力和大量的微裂纹,会引起模具早期龟裂;
(4)模具的热处理的影响,合理的热处理工艺可以使模具获得所需要的力学性能,提高模具的使用寿命,但是如果因热处理工艺设计不当或操作不当而产生热处理缺陷,将严重危害模具的承载能力,引起早期失效,缩短工作寿命;热处理后的模具要求一定的硬度,硬度偏低,易出现粘模和早期龟裂,如果硬度太高又可能开裂;
(5)压铸工艺的影响,高温的铝水传递给模具的热量比较多,致使模具温度比较高,当铸件取走后模具温度就急剧下降,这样就很容易产生热疲劳现象,出现热裂现象;充填速度过高会造成粘模、冲蚀、龟裂;当低速压射速度较高使金属液包裹较多的气体时,气体在高速压射进入型腔中的低压区会膨胀,气体膨胀产生爆破,气体带动铝液以很高的速度冲击、侵蚀型腔表面,造成型腔表面气蚀缺损,被气蚀的表面还会有裂纹产生;铝液压力的大小和受力方向对模具龟裂的影响也是很大的;脱模剂对模具激冷也会对模具产生热疲劳现象。
2 如何防止模具热裂现象
2.1 模具材料的要求
为提高模具抗热冲击韧度,目前常用的H13钢的化学成分纯净度要求为:优级钢S含量(质量分数,下同)要小于0.005%;超级H13钢要求S含量小于0.003%,P含量小于0.015%,同时要使用电渣重熔炉的精炼钢,它不仅纯净度高,还具有组织致密、优良的热疲劳抗力、抗热裂性好、优良的韧性及塑性,优良的抛光性、较好的异向同性等性能。钢材的均一性要求材料的组织要均匀,钢坯具备任意方向力学性能同性,不要有纵、横、深方向的性能差异。正确选用模具材料,采用高强度合金材料可以提高模具使用寿命;
2.2 模具设计要求
压铸件壁厚应尽量均匀,棱角过渡要有圆角或斜坡以减小应力集中,可使用筋条结构消除铸件形成的热节;模具的易龟裂部位和易损伤部位尽量采取镶件结构,损坏后便于维修和更换;模具中各组件、各部位都具有足够的厚度、宽度,使模具有足够的刚性以承受各种应力,还要使这些受力达到适当的平衡,以防止模具变形、开裂;正确设计浇注系统,设计内浇口的位置和充填流向时,尽量防止高速充填的铝水正面喷射冲击到型壁或型芯,设计内浇口截面大小时,如果选用的压射充填速度太高,有大量的动能减速后转变成热能传递到模具上,使模具温度升高,促使模具出现粘模、龟裂、冲蚀缺陷,压铸铝水的最大充填速度不应超过56m/s,充填速度以≤46 m/s为好,设计内浇口的厚度时,在保证产品表面品质的情况下,还是选用厚而大一点的内浇口为好,这样可以增加流量,又不增加对模具的冲击力;在模具的横浇道、分支浇道、内浇口附近,在铸件厚壁处的型腔、型芯等模具吸收热量比较多的部位要通水冷却;
2.3 模具制造的要求
模具制造的尺寸精度和配合精度要高,密封接触的配合面,必须密封配合,密封接触的面积要大,防止铝液钻入,尽量避免人为因素造成的烧焊修补处理,因模具烧焊修补过的部位,很容易出现龟裂;电脉冲或线切割放电精细加工时,应尽量采用低的电流及高的频率,以减小模具表面的过烧深度,使用好的电火花专用油液,可以起到冲洗、冷却、润滑、绝缘、防电离和减轻变质层的作用,放电时浸油比冲油能更好地减轻变质层;模具型腔精加工时,走刀量要小,不要留下刀痕,必要时需留下打磨抛光的余量,模具型腔的所有表面,即使没有留下加工刀痕的表面,都要进行一次打磨抛光,用以消除刀具加工或放电加工产生的硬化层和白亮层;
2.4 模具的热处理要求
H13 钢采用高压液氮气冷高真空炉淬火为好,可以有效防止模具表面的脱碳、氧化、变形和开裂,把淬火温度升高到1000~1050℃,根据模块材料的尺寸大小,和各个零部件要求的强度和韧性,适当控制温度和保温时间,使合金碳化物充分溶入奥氏体,这样可以减少模具因热处理碳化物溶解不充分,残留在晶界之间而造成的模具龟裂,但要注意钢的临界点Ac1和Ac3及保温时间,防止奥氏体粗化。淬火后用不同温度分3次回火,特别注意回火的效果,如果还要进行氮化处理,可以减少一次回火处理。模具加工时产生的切削应力、电火花放电变质层的应力、和压铸时产生的热疲劳应力,可以通过退火来减轻或消除,模具应定期退火处理消除应力:第一次去应力退火应安排在淬火之前(退火温度700~750℃ ),第二次去应力退火应安排在试模合格后的量产之前,再在压铸1万模、3 万模时各退火处理一次,氮化一次可以代替一次退火处理,对H13钢退火消除应力的温度比淬火时最后一次回火的温度低20~40℃,保温时间为1.0~1.5h,合理选择模具的硬度(HRC),所以一般建议:中、小型的铝合金压铸模为46~48;尺寸大的铝合金铸件和比较厚或形状复杂件的模具,应适当降低硬度(HRC)为44~46;
2.5 压铸工艺的要求
(......)