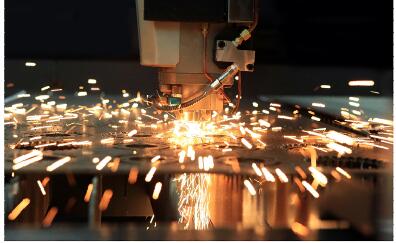
文:共立精机(大连)有限公司 冯晓梅、赵 然、徐庆琳
摘要 降低压铸模成本的基础是要选择好模具材料,经济可靠的优化设计是降低模具成本的关键,高速切削加工模具部件,合理管理加工各工序,减少设计加工失误,是降低模具成本重要手段。
关键词:压铸模;成本;材料;NC加工
1、 引言
随着科技发展,压铸模制造的铸件,正被广泛应用我们日常生活中,如汽车离合器壳体、变速器壳体、四缸体、三缸体,滤清器,行李架;摩托车左右箱体、左右箱盖,后衣架;电子铸件散热件,电机壳体等许多机械电子铸件。压铸生产的铸件已渗透各个领域,国内外压铸生产厂家在迅速发展,对压铸模需求也越来越多。压铸模市场竞争激烈,多数压铸生产厂家对压铸模价格特别关注,不断要求模具制造成本价格降低。模具价格主要包括:模具材料(原材料、规格品、标准件);模具设计 CAD(2D/3D);模具制造,NC 粗精加工、放电线切割加工;模具组装研配,试模,检测,包装运输等。
2、 选择材料是降低压铸模具成本的基础
选择材料要根据客户铸件要求,压铸件市场需求数量来考虑:(1)如果压铸铸件需求数量多,模具型腔材料,可以选择好的进口材料一胜百DIEVAR、QRO90、日立金属 DAC55、大同钢材 DH31-EX 等。可保证模具寿命长为8万~10万模次。(2)如果压铸铸件需求数量少,模具型腔材料,可以选择一般材料国产优质 H13、日立金属 DAC-P、大同钢材DHA1等。(3)模具模板材料:一般压铸机为 350t 以下可选择 S50C,压铸机大于 350t 可选择 FCD550、S50C,压铸机大于2,000t如铸件为汽车离壳、变壳、四缸体、三缸体可采用Sn2MC(铸钢)、S50C、P20等材料。(4)主要规格品采购:模具侧抽油缸可选择南武油缸(NAMBU)、掘内油缸、派克液压缸(PARKER)、国内大连三尾油缸等,采用国内油缸价格相对便宜。在购买油缸时,如客户无特殊要求,要降低模具价格可只购买油缸单品,不含油缸限位装置等附属品。因油缸成品含油缸限位装置等价格很高,模具厂家可自制油缸附属品、油缸限位装置等部件,从而能节省模具成本。(5)选择好的模板和油缸可以重新再利用,只更换模具型腔,就可继续压铸,节省模具成本。有些压铸厂家,在制造模具的同时要求制造备用模具型腔一套,这样能压铸出更多铸件。(6)软模制造材料选择:软模即实验用模具,一般为新铸件开发,只要求模具压铸出 2,000 件左右。模板可选择为 45 钢,模具型腔材料可以选择国产优质H13或NIKKA30。
压铸厂家制造模具时,不能单纯只看模具价格,首先主要看制造模具选用的材料,确认模具能保证的寿命。如果压铸厂家不看重材料,只贪图价格便宜,模具压铸不了多少件就有可能报废,得不偿失,即铸件需求量决定模具材质和价格。
3 、模具设计是降低成本的关键
(1)模具设计要按铸件大小,通过铸件投影面积计算,合理确定压铸机的吨位(90~3,500t),确认好模具结构(压铸的腔数)。如果铸件是左右对称,或铸件形状是细长,可选择1模2腔,如图1所示。如果铸件是多种小件需求量大,在压铸机条件允许下可选择 1模 2 腔,1 模 4 腔或 1 模 6 腔等,同时压铸出多件,能降低成本。
(2)模具造型设计要根据铸件确定基准坐标系,造型设计首先要对铸件进行设计,增加加工余量,转为毛坯件,再加上收缩率转为铸件。在铸件上按出模方向,合理构造出分型面,进行动模、定模、侧抽芯分型设计。压铸件摆放决定模具型腔材料尺寸,压铸件摆放要合理,便于压铸成型,减少侧抽多角度设计。如图1、图2所示。
图 1所示铸件摆放纵向和天侧平行,设计结构紧凑,节省材料,加工简单,便于钳工组装。模具总体积小,节省成本,有利于压铸。图2所示铸件摆放纵向和天侧端面不平行,明显模具型腔要大于图1所示结构,设计繁琐,浪费材料,加工复杂,因侧抽带角度,钳工组装麻烦,模具总体积大,模具成本增大。
(3)模具结构设计是在分型设计基础上,按压铸机吨位确定模具型腔大小、模板大小、侧抽滑块大小方向、油缸大小等。模具设计合理,结构紧凑,能压铸好的压铸件是模具制造成败的关键。压铸模设计时,要考虑模具各个部件加工简单、易操作,钳工组装方便等。这样才能节省加工时间,降低成本。#p#分页标题#e#
(4)模具镶件结构,模具型腔局部易损处,应该设计为镶件。如模具在压铸过程中,模具型腔损伤或龟裂时,可只更换模具型腔镶件继续压铸,延长模具使用寿命。
(5)模具套板结构,模具型腔重要成型部位可选择好材料如 QRO90、DIEVAR,边缘、浇道处则可选择普通材料SKD61、H13 等。这样既可保证压铸出铸件质量,又可节省成本。如果模具型腔成型处有龟裂、破损,只更换型腔成型处即可,保证模具使用寿命。
(6)模具侧抽、滑块座设计:如果模具侧抽不是侧抽芯,或小侧抽,模具侧抽应尽可能设计成分体结构,即由侧抽和滑块座二部分构成。侧抽为一体结构,材料大浪费,制造难度大,侧抽材料一般同动定模型腔为 SKD61 或 DIEVAR,滑块座材料一般为 NIKKA30、H13、P20等。
(7)模具设计结构要合理,要考虑CAM 模具加工编程,NC 加工、放电加工,保证加工操作易实现。配合处有R角处应尽量增大R角,有利于NC 加工,节省加工时间,节约成本。如 R 小为 R1mm、R0.5mm,NC加工需要更换直径小刀具,进一步做局部清根加工。如图 3、图 4 所示,如 NC 加工不能实现,有时需要补电极放电加工清根。增大模具 R 角,同时还能延长模具使用寿命,R过小,模具型腔会容易损伤,易出现早期龟裂。
(8)压铸模具设计要标准化,要实现优化设计。模具设计选择材料规格要合理,尽量减少加工成本。DH31-EX,DAC55 等材料是无棒料,设计抽芯和圆直径大模具镶件,应该优先选择 DAC 材料,如果直径大抽芯材料选择 DH31-EX,粗加工首先要把板材料加工为棒材,即要做方形改圆形加工,浪费材料,消耗工时,增加模具成本,不可取。
(9)模具设计软件最好选用好的3D设计软件,使用 Pro/E 参数化设计可以实现分型设计。Pro/E 能打开各种3D设计软件,如UG、CATIA、Solid Works 便于模型输入输出。应客户要求提供 3D 文件格式为STEP 或 IGES,最好是提供 STEP 格式,STEP 导入曲面,漏面少,易转换为实体。能节省修补漏面时间,缩短设计周期。
(10)模具设计时要对铸件设定好收缩率,一般为 0.5%~0.6%。如收缩率选择正确,压铸出毛坯件,成型尺寸基本在公差范围内,减少铸件孔位调整,减少反复修模、试模,能节省时间,降低模具成本。
(11)模具设计要合理布置浇铸系统和冷却水、积渣包、排气道等。有条件要做好模流分析,这将有利于压铸出好的铸件,有利于延长模具寿命,减少损耗。如设计不好,模具型腔易损坏,开裂。反复焊接修正会影响模具寿命,增加成本。
(12)模具设计最后要做干涉检查,防止部件组装时干涉,导致模具反复拆分修正,减少加工返工消耗工时,减少模具成本。
(13)模具设计标准基础要力争简化加工,如模具易损件,即模具 型 芯 设计,图 5 所 示 型芯定位台ϕ10mm 尺寸,可直接选择棒料ϕ10mm 设计,这样可省去车加工型芯定位台ϕ10mm,节省材料,缩短加工时间。因模具型腔型芯定位台孔,单边要比型芯定位台直径大 0.5~1mm,设计模具型腔型芯孔时,要考虑棒料规格,不要盲目设计。有许多压铸厂家要求型芯设计,按标准顶杆设计,如图6所示,型芯定位台和配合段尺寸严格按顶杆尺寸设计,加工型芯时可利用顶杆,只修改前端成型处就可以使用。这种方法,节省型芯加工时间,也为压铸厂提供方便,压铸厂家采购型芯备件只需购置一批顶杆,省事省钱(因大批量采购顶杆能便宜,能节省成本)。
4、 模具加工是节省成本重要手段
目前先进科学技术发展,CAM高速切削加工可以实现模具粗精加工,替代一些原有的模具放电加工,省去了一套费时费力加工流程,如图7所示。原模具放电加工需要先拆分电极,购买电极材料,加工粗精电极,人工要参照样件修电极,检测电极,再放电加工模具型腔。放电加工后,钳工手要修型抛光,去除放电加工痕迹,如图8所示,成本较高。
放电加工(电火花)加工的原理是石墨或铜电极(阳极)和钢材(阴极)之间的不导电介质中放电,模具的侵蚀通过放电来控制。操作过程中,负电极进入钢材中获得所需形状,电火花加工中钢材的表面温度非常高,从而使其溶化和蒸发,在表面产生了一层溶化后再凝固的较脆层,紧接着这层的是再淬硬和回火层,电火花加工对模具加工表面性能产生了不利的影响,破坏了钢材的加工性能。因此,模具加工如果高速切削能实现,应该尽可能采用切削加工。模具加工注意下面几点,可实现节省成本。#p#分页标题#e#
(1)电极加工:要考虑粗精电极加工成本。大电极粗精电极可用一个,粗电极放电加工完,下沉加工为精电极,再放电精加工型腔。如考虑要制造复制模具,电极材料可加厚,反复利用作为复制模具粗电极。
(2)电极拆分:整体电极(一体电极、主电极、大电极),可带成型处边缘设置的积渣包、桥部等。局部电极(小电极):①铸件尺寸要求严格;②整体放电加工不到位;③NC加工实现不了的部位,可拆成局部小电极再放电加工,拆分好电极一定要在3D中装配检查,防止干涉,避免失误。
(3)模具粗加工,在保证型腔热处理变型前提条件下,留用精加工余量要小些,缩短精加工时间,这样能降低制造成本,提高劳动生产率。
(4)粗加工去除切削材料,回收价值很低。模具型腔套板或模具型腔中有大镶件可先进行线切割加工,线切割加工出中间材料可再利用制造小部件。再切削加工模具型腔编程时,毛坯料应选择为线切割加工后的坯料尺寸。这样可缩短加工切削时间,减少刀具的损耗,大大降低成本。
(5)模具型腔CAM 精加工要精确到位,便于钳工组装研配,减少模具反复修正,减少试模次数。这样能节省时间,节省成本。
(6)采用先进的加工工艺,实现计算机辅助生产管理,合理安排各工序工位,可节省模具加工时间,提高劳动效率。
5、 结束语
展望压铸模具发展,压铸模具设计要创新,要建立人工智能和专家系统,充分利用先进3D设计软件,将铸件 3D 造型快速分型设计,及时进行模具流模分析,迅速定出模具结构方案,缩短设计周期,要设计出节省成本优质好的压铸模具。模具加工要利用先进高速切削加工设备4轴加工中心、5轴加工中心,精确加工出模具各个部件。应选用价格便宜,能延长模具寿命的新材料,力争做出高质量低成本的压