文:宁波大红鹰学院 张玉玺
锁模力是选用压铸机时首先要确定的参数,是压铸机所具备的能力。在压铸成形时,当金属液被压铸机的压射系统高速、高压瞬时充填入模具型腔时,金属液受到很大的压力,此力作用在压铸型型腔的各个方向,该力试图将压铸型沿分型面胀开,此力称之为胀型力。胀型力与压铸件在模具分型面上的投影面积及其浇排系统面积有关。为防止压铸型不被胀开,压铸机的锁模力要大于压铸型在分型面方向上的总胀型力,这样才有可能使压铸生产顺利完成。但是这不是唯一条件,还有一个条件就是必须确保总胀型力中心与压铸机的锁模力中心一致。当压铸机的锁模力远大于压铸型的总胀型力时,两个中心是否一致常被忽略不计,但当总胀型力接近压铸机的锁模力时,偏心不利现象就会突显出来。压铸机的锁模力主要是由四个较粗的哥林柱所受的预拉力实现的,哥林柱直径是按预拉伸条件下的刚度设计计算的,每根哥林柱的最大受力极限值是压铸机锁模力的四分之一,单侧两根哥林柱的最大受力极限值是压铸机锁模力的一半。当胀型力中心不在压铸机安装中心时,意味着四个哥林柱受力不均,带来不利影响,因此让胀型力中心与锁模力中心重合很有必要。
1、 压铸件特点及工艺条件分析
户外圆桌面整体是由外围四个扇形压铸件 (铝合金ADC12)和中央一个圆形冲压件盖板 (不锈钢201)组合 而成 (图1),桌面直径 1150 mm,内圆直径420 mm。桌面表面有许多复杂网纹,筛面多孔,由4个1/4圆的扇形压铸件组合而成。
扇形压铸件面积较大,正投影面积为1 760 cm2,平均壁厚为3.5 mm,质量约为2.5 kg。该扇形压铸件高度尺寸较小,成形工艺要求不高,压铸工艺较简单,但是压铸模具设计需考虑胀型力及模具安装问题。否则,当胀型力中心不在压铸机锁模力中心时,会造成压铸机单侧锁模力不足,影响压铸生产,甚至会引发压铸机故障。
2、 扇形件压铸模具设计
2.1 第一次模具设计方案
第一次模具设计的动模侧如图2所示,在设计时采用常规的设计方案。根据外圆直径D和内圆直径d估算扇形件正投影面积 : A=0.785 ×(D2 -d2)÷4=0.785 ×(1152 -422)÷4=2249 cm2。因铸件尺寸较大,压铸件分型面投影总面积则以铸件面积的120%估算,则铸件分型面投影总面积 (含浇排系统):A全=2249×1.2=2699 cm2。
选择压射比压,由于铸件高度尺寸较小,成形工艺相对简单,比压选择最低值:P=25MPa=0.25t/cm252 -422)÷4=2249 cm2。
胀型力:F=A全×P=2 699×0.25=675 t。
选择压铸机,因上述计算未考虑铸件的多孔部分,且浇排系统也是估算值,结合实际情况选630T压铸机。DCC630压铸机射料中心位置为-250 mm,即射料中心在安装中心之下250 mm处,哥林柱内距750 mm,哥林柱直径160 mm,冲头直径分别为70、80、90 mm。由于铸件有多孔结构特点,无法计算胀型力中心位置。凭经验将射料中心设置在圆桌面中心以上40 mm处,考虑到模具安装问题,将模具上侧两角设置缺口,并用三维软件模拟安装。最后形成安装方案:即安装时将模具分开,先装定模侧,再装动模侧。虽然完成了模具的基本设计,但在压铸生产过程中暴露出严重的问题:模具上半边跑料,铸件厚薄不均,铸件成形不足,内部气孔缩孔严重,铸件强度不合格,甚至还出现压铸机合模故障。
2.2 模具修改方案
第一次模具设计失败后,为挽回损失,将原模具的浇口套和分流锥安装孔进行偏心扩孔加工,以实现射料中心上移。由于尺寸的限制,最终模具射料中心成功上移30 mm。
由于射料中心是模具在压铸机上的定位中心,因整改后的模具整体下移30 mm,为消除模具下边两角干涉,将模具下边原有的两个导柱孔废除,在上面相应处重新加工安装,并将模具下两角进行缺口处理。整改后的模具有一定的改善效果,可以维持基本生产,但成品率及产量均很低。
3、 改进设计方案亮点剖析
3.1 型腔布局确定
如图3所示,将模具胀型力中心设置在压铸机的安装中心位置上,溢流槽数量位置合理布局,模具安装问题得到充分解决,消除第一次模具设计需分模安装的弊端,模具可以在上下哥林柱之间横向移入压铸机,实现模具整体无干涉快速安装。生产过程中,避免了铝液飞溅,压铸件品质稳定,成品率显著提高。
3.2 模具胀型力中心位置的确定
3.2.1 铸件面心的确定
图4为铸件投影面积图。在设计中,先按删除法在CAD界面下将铸件正投影图中投影面内部的线条删除,只保留投影面域轮廓,然后将投影面域打上剖面线,求出“剖面线”面积,即为准确的投影面积。将计算得到的投影面积用于胀型力计算,再将该轮廓导入三维软件,并拉伸成实体,即可求出质心数据。由于拉伸的是等厚实体,则实体质心的X坐标Y坐标与面心相同。同理,当设计出浇排系统之后,仍然可以求出面心数据。
当面心数据相对浇口中心与压铸机参数吻合时,则胀型力与锁模力位置重合,压铸机哥林柱受力均衡。
3.2.2 全铸件胀型力中心的确定
图5为全铸件胀型力中心位置示意图。图5a为第一次设计方案,图5b为改进设计案一,图5c为改进设计方案二。图5c为设计改进最终方案,在铸件高度位置不变的情况下,射料中心逐步向上调节。以图5a为基准,图5b压射中心上移50 mm,图5c压射中心上移70mm。由于图5a胀型力已略超过压铸机临界值,故图5b和图5c将溢流槽设计进行合理化处理,溢流槽总投影面减少,但总容量通过加深设置来保证,并且在铸件下方两边设置溢流槽更有助于铸件成形。
3.2.3 全铸件胀型力中心的尺寸设计
首先分析第一次模具设计失败原因。如图6所示,将全铸件实体坐标设置在射料中心,求出该方案条件下全铸件的质心为x=1.22 mm,y=317.48 mm (z轴数据忽略,z轴数据与拉伸实体时输入尺寸相关)。因压铸机射料中心位于压铸机安装中心之下250 mm处,所以不难看出,第一次设计时胀型力中心偏离压铸机安装中心67 mm。由于这种严重偏心,导致在压铸生产过程中出现种种不良问题。
3.3 设计改进方案一
图7为设计改进方案一的模胀型力中心位置图。本方案中:①将浇排系统进行了较大调整,首先浇口形式由四分支改为二分支;因为理想的浇口以单一为主,考虑铸件浇口处中部有一个外凸形状,二分支浇口更有利于浇口清理;②溢流槽也由原来的密集型向合理设置型转变;③为调节偏心,将射料中心在第一次模具设计方案的基础上上移了50 mm。最后,将CAD图导入三维软件进行“拉伸实体”处理,并将全铸件实体坐标仍然设置在射料中心,通过前述方法,求得本方案条件下全铸件的质心为x=1.07 mm,y=271.26 mm。不难看出,此方案设计的胀型力中心偏离压铸机安装中心21 mm,偏心程度明显减小。
3.4 设计改进方案二
图8为设计改进方案二的模胀型力中心位置图。在保持图7总体方案不变的条件下,通过CAD制图“拉伸”命令将射料中心上调20 mm,再将CAD图导入三维软件进行“
拉伸实体”处理,并将全铸件实体坐标仍然设置在射料中心,求得形成该方案条件下全铸件的质心为x=1.08 mm,y=252.96 mm。此方案设计中,胀型力中心偏离压铸机安装中心仅为3 mm。将图8方案的射料中心再上调3 mm,则形成如图9所示的最终设计方案。
从图9所示最终设计方案的数据看出,全铸件的正投影面积为2029 cm2,选择压射比压P=30 MPa=0.3 t/cm2,模具胀型力:F=A全×P=2 029×0.3=609 t。由于压射比压由
25 MPa调节到30 MPa,所选择压射比压可调节空间增大,铸件成形质量得到保障,铸件强度得到提高。
4、 生产验证
用最终设计方案制造的模具投入压铸生产,再无跑料现象发生,班产稳定,压铸机运行平稳可靠。最终设计方案生产的压铸件如图10所示。压铸件壁厚均匀,成形良好,铸件内部气孔缩孔均在合格范围之内,铸件强度合格率达100%。
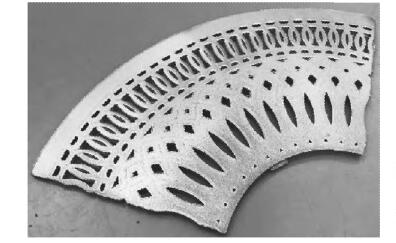
图10 最终设计方案铸件图
5 、结束语
户外圆桌面扇形件压铸模设计制造从失败到成功,整个过程经历了整改、分析、精确计算。最终设计方案解决了三个问题:一是解决了偏心问题;二是增加了模具强度,第一次设计动定模及其套板上侧尺寸薄弱,强度不足,改进后的模具动定模及其套板尺寸实现均衡设计,强度合适;三是解决了成形问题,铸件成形质量得到保障,铸件强度得到提高。此次模具结构设计改善效果显著,压铸机能力得到正常发挥。