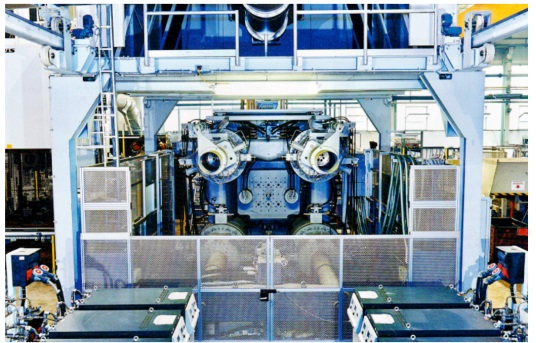
压铸工厂经济性的持续改善
通过系统方法获得成功
高效的工艺流程对压铸厂的经济效益至关重要。 因此生产商不断尝试优化他们的流程,来提高产品质量和利润。但是影响生产流程的因素很多,可实施的针对性措施也同样多。因此,建议采用系统方法来持续优化工艺流程。
工艺流程优化的基础是各台设备目前状况的充分可靠信息。实践证明应考察设备的整体效能或OEE(整体设备效能),这直接反映了压铸厂的经济性。影响这一指标的三个重要因素为废品率,机器使用率,以及压铸车间自身的生产率(图1)。OEE是用来检查设备能效和经济性的特定设备参数。它同样有助于确定能效提升的改善措施。经验表明,压铸设备的OEE应超过65%。
系统方法
系统流程优化首先分析哪些因素对OEE影响最大。 取决于所生产的工件和压铸厂的条件,效能和质量损失,以及停工所带来的影响程度会有所不同。对于废品率极高的生产,优化的重点首先在于铸件质量。在这种情况下,首先考虑改善周期时间或者使用率是没有效果的。第二步再调查设备使用率和工艺稳定性,最后提出改善周期时间的相应措施。直接影响这三个因素的可能变量是机台,现有模具,以及人员(图2)。模具往往需要很大投入才能进行改动,而机台精调却能很快实现改善。培训和训练有素的员工也能提高压铸车间的效率。
提高质量,减少废品
只有出现的铸件缺陷能被明确识别,质量改善措施才能达到目的。这里指的是能导致组件出现各种功能缺陷的物理性流程错误。一方面包括设计错误,比如变形,扭曲或错位。另一方面必须注意孔隙,气泡或杂质等内部缺陷,以及裂纹,冷料和毛刺这些表面缺陷。根据缺陷情况,它们也有可能组合出现,针对性的采取特定措施进行修正。为此,通常会对压铸机台参数和外围设备进行调整,以及对压铸模具进行修整。在某些情况下,这还不够,还要求对模具设计进行更深入的干预。这一步骤通常耗时且成本高昂。
改善使用率
为了显示可能的和实际生产时间之间的差异,需要对停机时间进行充分评估。停机可能是由于保养和维护,技术故障和维修,以及由于操作错误,缺少材料和人员所导致的组织性空转。通过特殊的软件工具,比如位于瑞士乌兹维尔的布勒公司的“事件分析器”,能够对停机时间和原因进行自动评估。这一软件被安装在机台控制系统里。在那里,将生成一份LOG文件,该文件可以传送给布勒专家团队进行评估。然后评估结果和统计数据返回铸造厂,依据这些结果和数据,可以与布勒公司一起研究出提高利用率的具体措施(图3)。
通过比较,从不同的铸造厂所获得的数据得到惊人的结果: 平稳生产情况下的铸造设备几乎没有中断发生, 并且在自动模式下能运行长达100分钟, 但是我们每天却可以记录到有不稳定流程的设备多大200次的中断。某些情况下,自动模式下运行的时间甚至不足10分钟(图4)。通过这些数据很容易看到,还有哪些提升生产力的潜力未被利用。通过持续性的原因研究以及适应性措施,压铸设备的使用率能得到持续提高。在观察长时间停机的原因时也会看到有趣的结果。然后可以明确评估所实施改善措施的效果(图5)。
有效的生产转换
在观察压铸厂时可以发现,有效的模具切换可以为提高机台生产率做出巨大贡献。一种用于优化铸造车间使用率的工具为SMED(快速换模)。SMED是一种使生产转换更有效和更快速执行的方法。通过标准化流程和工具,比如快速接头,来减少模具切换时间,然后设备可以更快的重新投入生产。
改善周期时间
周期时间的优化能直接提高生产率。换句话说,能增加单位时间内所生产的铸件的数量。在目前常规的压铸工艺过程中,高达45%的外部能量释放时间用于喷涂(图6)。这是一大问题, 因为较长的周期时间不仅降低了机台的生产效率, 还会导致巨大的热负荷,从而缩短模具的使用寿命。另外,进料以及铝的凝固也会占用大约40%的周期时间。这些数字清楚的表明,将外围设备无缝集成到压铸工艺中,以及通过共形冷却和新的微量喷雾工艺来改善热量管理具有巨大的潜力。
热量管理
提高铝压铸经济性的最大潜力在于工艺流程的热量管理。特别是通过喷涂工艺从外部冷却模具这种做法应该减少。喷涂过程的实际任务是涂上脱模剂,使得液态铝不会和模具钢料反应和粘附。同时还可以防止模具腐蚀。使用喷涂工艺进行冷却非常耗时和耗费资源。此外还需要大量必须进行回收和净化处理的脱模剂。现在已经有一些工艺,对于复杂的产品也可以高效快速的从内部冷却模具。为此在模具设计阶段就应具体考虑,如何以及在何处做模具运水是可行和合理的。
随形冷却注塑技术领域目前已普遍使用增材制造工艺来加工模具镶件。但是在压铸领域仍然很少使用。已有研究表明,模具中3D冷却结构的正确布局,能将铸件的纯冷却时间减少约一半(图7)。同时,冷却流道的分支可以实现更均匀的表面温度和更高的冷却液通过量。然而,模具设计和冷却结构的分配是复杂和要求极高的过程。增加的设计和模具加工成本,在进行整体计算时,可以被缩短的周期时间和减少的资源消耗所抵消。
微量喷涂
与优化过的内部模具冷却相结合,建议使用微量喷涂技术。因为模具不再需要通过喷涂过程来进行冷却,因此仅需喷上一层薄薄的脱模剂就足够了。这样一方面可以大幅度减少喷涂时间,另一方面可以极大节省喷涂剂,压缩空气和水的用量(图8)。此外,减少对模具的腐蚀,能显著延长模具寿命。
并行进程
同样,并行进程也可持续缩短周期时间。目前,压铸机台工艺和外围设备工艺,比如去毛刺压力机,是分开考虑的。原因在于,浇注过程由机台控制,而取件及其进一步处理由本地机器人进行控制。因此,全面优化是困难的,其可能性是有限的。将来,更高层次的整体车间管理具有巨大的潜力。具有更高优先级别的核心工艺仍被视为首选。通过外围设备的全面集成,更好地合作,能够实现协调一致的动作,缩短启动阶段并压缩周期时间。同时,显著提高铸造车间的可用性。
能带来盈利的方法使用
在实践中,这种逐步进行流程改善的方法已经得到验证。无论是通过自己的主动行动还是通过咨询外部顾问,都可以通过这种方法得到令人印象深刻的结果。 除了生产质量改善外,铸造厂还能从更高的设备效率中获益。与此同时,由于资源的使用显著降低,也会使得铸造厂能更加生态地运作。通过将来引入车间管理,生产力的进一步显著提高将成为可能。
OEE优化的经济影响
OEE的优化相当于提高了单位时间的合格品产量。压铸厂的经济性能因此显著提高,以下计算示例清楚地说明了这一点:
计算示例 1
产品: 电子产品外壳
模具: 4穴
重量: 200 g
年产量: 1 500 000 件
机台锁模力: 1000 吨
周期时间: 45 秒
OEE改善...
使得每年节省5 %
40 500 € (相当于 2 %)
使得每年节省10 %
76 500 € (相当于3,8 %)
使得每年节省15 %
109 500 € (相当于5,4%)
计算示例2
产品: 4缸发动机缸体
模具: 1穴
重量: 12 000 g
年产量: 200 000 件
机台锁模力: 2800 吨
周期时间: 90 秒
OEE 改善...
使得每年节省5 %
82 400 € (相当于1,1 %)
使得每年节省10 %
155 600 € (相当于2,1 %)
使得每年节省15 %
221 000 € (相当于2,9 %)
成功的秘诀
熔炼技术和材料技术的结合是以需求为导向,是研发出热作模具钢Thermodur E 40 K Superclean的关键。为提高韧性,降低了硅含量。此外,材料专家还优化了钼,钒和铬的含量。其结果是提高了耐热性和导热性。为了进一步延缓使用中出现热裂纹,德国特种钢材厂通过电渣重熔去除有干扰的钢杂质,如硫化物和氧化物。结合额外的结构处理,可以实现结构的高纯度和均匀性。因此,这一热作钢能满足变化温度负荷方面的最高要求,并能永久承受。由于热裂纹的出现延迟,材料的使用寿命显著增加。因此,这种特种钢最适合用于大量使用的压铸和挤出模具。用户受益于高质量的组件,以及轻金属产品生产成本的降低。