纪莲清 熊守美
摘要: 应用具有不同浇道尺寸的简单圆形拉伸试样研究压铸工艺参数对ADC12铝合金超低速压铸件性能的影响, 以优化超低速压铸工艺及其参数。试验结果表明, 各种超低速压铸工艺条件下铸件的密度都比普通压铸高, 影响铸件性能的主要因素不再是气孔, 而是合金的凝固组织及飞溅凝固片和氧化夹杂等缺陷。在超低速实验条件下, 浇道截面尺寸越大,对铸件性能影响越大, 不同浇道尺寸对应有最佳浇道速度, 在试验的三种浇道条件下, 最佳浇道速度均低于0.6 m/s;模具预热温度、浇注温度、铸造压力都有最佳值; 在无增压条件下, 仅采用较大的压射压力也可使铸件获得较好的力学性能。
关键词: 铝合金; 超低速; 压铸; 工艺参数; 力学性能
孔洞类缺陷是压铸中公认的最主要缺陷之一, 铝合金中金属液流动过程的卷气和凝固过程的收缩是产生孔洞类型缺陷的主要原因, 不仅使铸件力学性能下降, 不宜进行热处理, 而且降低了压铸件的耐压性和气密性, 限制了压铸件的使用。因此, 研究超低速压铸工艺以减少压室及型腔中气体含量, 从而减少压铸时的卷气十分必要。
压铸时理想流态应是慢压射冲头慢速前进, 排出压室中的气体, 直至合金液充满压室, 再选择合适的快压射速度, 在合金液不凝固的情况下充满型腔, 然后压射冲头以高速、高压施加于合金液上, 使压铸件在静压力作用下凝固, 以获得表面光洁、轮廓清晰、内部组织致密的压铸件。超低速 ( Supper Slow Speed,以下简称SSS ) 压铸正是利用极低的压射速度, 使金属液以极低的速度 ( <0.15 m/s ) 顺序充填型腔, 从而降低铸件气体含量, 提高铸件质量的一种压铸工艺。国内外不少学者对一般压铸时加压开始时间、加压压力、速度等对铸件密度变化的影响进行了大量的研究,但对超低速压铸工艺的研究还未见报道。本研究以工
业用压铸铝合金ADC12为研究对象, 设计了标准拉伸试棒金属模具并进行超低速压铸试验, 从铸件密度、力学性能、组织等方面, 考察不同超低速压铸工艺参数对铸件力学性能的影响。
1 试验过程
1.1 试验材料
试验所选材料为商业用压铸铝合金JIS ( 日本工业标准) ADC12, 用ICP ( 等离子体发射光谱仪Vista-MPX )测得其化学成分 ( 质量分数, %, 下同) 为11.25 Si、3.09 Fe、2.51 Cu、0.21 Mn、0.096 Mg、1.74 Zn, 其余为Al。
1.2 超低速压铸工艺参数
根据GB/T13822—1992 《铸造有色合金试样》 A型的规定, 设计并制作了如图1所示超低速试验的模具,有Φ24 mm、Φ24 mm半圆、24 mm× 6 mm三种浇道尺寸, 并应用该模具对各影响因素进行较详细与系统的研究。试样在650 t冷室压铸机 ( TOYO BD-650-V4-N )上进行压铸, 基准条件为: 浇道尺寸Φ24 mm× 2 mm、溢流槽尺寸20 mm× 3.0 mm、高速速度0.09 m/s ( 浇道速度0.39 m/s ) 、低速速度0.1 m/s、铸造压力100 MPa、熔液温度700℃、模具预热温度150 ℃、持压时间10 s、除气时间20 min、料柄厚度40 mm, 采用超低速专用低速离型剂 ( 与水的比例为1∶ 30 ) , 冲头用低速润滑剂润滑。
将试样从浇道处取下, 测量不同试验条件下试样( 图1 ) 的密度 ( JT5003型电子天平, 精度± 0.001 g ) 及其力学性能 ( CSS-2220B电子万能试验机) , 并在所得压 铸 件 上 截 取 并 制 备 金 相 试样 , 在 金 相 显 微 镜( DMM-400C光学显微镜) 及扫描电镜 ( LEO-1530热场发射扫描电镜) 上观察微观组织及断口。在万能材料试验机上进行拉伸实验时应变速率基本控制在1 mm/min左右, 同一工艺条件下试样测量3-5个, 并取平均值,然后作为最终测量结果。
2 试验结果及讨论
2.1 模具预热温度对超低速压铸件的性能影响
模具预热温度分别采用100 ℃、150 ℃及200 ℃三种, 其它压铸成形参数固定, 性能测试结果列于表1。从表1可以看出, 在模具预热温度为150 ℃时, 超低速压铸成形件的密度最高, 抗拉强度、屈服强度及伸长率也都最高, 这是因为SSS压铸时压射速度很低,合金液在压室及型腔中温度有较大降低, 熔液流动性不好, 当模具预热温度过低时, 坯料在充型时冷却速度过快, 坯料还没来得及填充整个铸件浇道就已经凝固了, 冲头压力施加时间不够或施加不上, 所以密度和力学性能较差。事实上SSS的充型性能差, 只能压铸壁厚较大的耐压制件。当模具预热温度较高时, 即当模具预热温度能满足坯料在一定压铸条件下可以完全充型时, 如果再提高模具的预热温度, 压铸时在型腔表面的冷却层极薄, 组织粗大, 力学性能下降, 生产效率也较低, 且有可能产生飞边, 增加合模难度。可见, 在超低速成形时, 模具预热温度应控制在一个合适的范围, 根据试验结果, 特别是本试验采用的模具形状比较简单, 选择150 ℃作为模具预热温度, 这样既可兼顾充型能力和合模难度, 同时又#p#分页标题#e#
可保证铸件良好的力学性能和一定的生产效率。
2.2 浇道速度对超低速压
铸件的性能影响
浇道速度对铸件性能的影响见表2, 从表2可以看出, 同一种浇道时浇道速度对铸件密度的影响较小;随着浇道速度的增大, 铸件抗拉强度呈现先增大后减小的趋势, 当浇道速度为1.2 m/s时达到最小值; 屈服强度随浇道速度的变化影响较小; 浇道速度对伸长率的影响规律与抗拉强度相同。不同浇道时, 浇道截面积越大获得的铸件密度越大, 铸件的抗拉强度、伸长率越高, 对屈服强度的影响不明显。浇道速度增大或恒定对铸件的密度影响较小, 但加速时力学性能较高。超低速压铸时, 由于冲头慢压射速度很低, 慢速运动时将金属熔体堆积在冲头前端不产生跳跃波, 熔体液面随冲头前进逐渐升高达到压室顶部, 使压室的
气体可以及时排逸; 且冲头快压射速度更低, 使金属液以极低的速度顺序充填型腔, 减少了合金液流动时的卷气, 故超低速压铸件气体含量很低, 密度较高。
但由于SSS压铸时合金液在压室中停留时间长, 温度下降较大, 高速速度又太低, 熔体达到型腔后快速冷却凝固, 会降低熔体的流动性和充型能力, 故采用截面较大的浇道或增加浇道速度可提高合金液的充型能力,从而提高铸件的性能。但过大的浇道速度会产生较多的飞溅凝固片和氧化物夹杂, 这些凝固片或氧化物夹杂作为拉伸时的裂纹源直接导致铸件的力学性能下降,这就是随高速速度提高力学性能提高, 而高速速度继续提高后力学性能反而降低的原因, 其拉伸断口形貌见图2。铸件的拉伸断口为静拉应力造成的混合断口,有典型的辐射状棱线形貌, 可以很容易据此找到裂纹源 ( 图2a ) 。扫描断口由多个解理平
台组成, 很少有韧窝, 且断口上有较多的二次裂纹, 呈典型的脆断特征( 2b ) 。
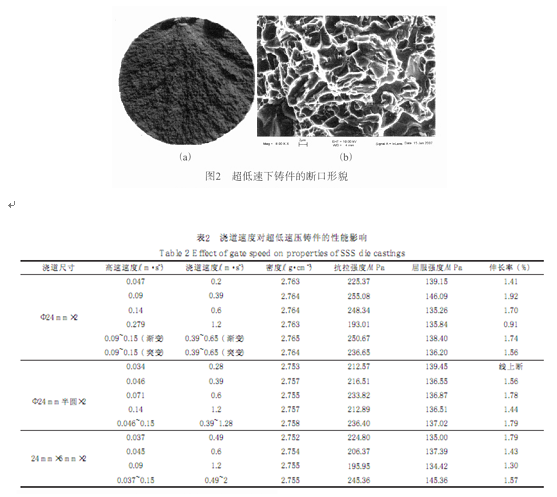
2.3 铸造压力对超低速压铸件的性能影响
比较表3中结果可得, 随着铸造压力的下降, 超低速压铸件的密度略有下降; 其力学性能随铸造压力增大呈现先增后减的趋势, 三种浇道都是在铸造压力为100 MPa时性能较好,
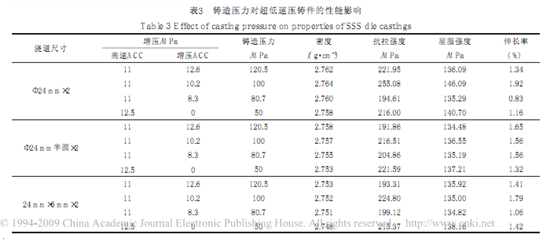
铸造压力在80.7 MPa时性能较差。三种浇道相比, 截面积较大的浇道Φ24 mm的铸件性能明显优于另两种截面积小的浇道的铸件性能,Φ24 mm半圆与24 mm× 6 mm两种截面积较小的浇道的铸件性能相近。增大压射压力, 即使增压压力为零, 三种浇道也都获得了较好的铸件性能, 但此时三种浇道铸件性能相近, 浇道截面积中等的铸件性能稍优。
铸造压力是获得组织致密、轮廓清晰压铸件的重要因素, 铸造压力越大铸件越致密, 故铸造压力降低会引起铸件密度的降低。由于超低速压铸时浇道速度较低, 合金液充型时流动性不好, 在浇道处出现较多的金属堆积, 在压铸温度相同的情况下, 采用较大的铸造压力或较大的浇道尺寸可保证合金液的流动性,有利于减少缩孔和缩松, 提高铸件性能。在其他条件不变的情况下, 铸造压力越大, 铸件的组织应该越细小致密, 性能应该越好。而三种浇道铸造压力为120 MPa时铸件的性能比铸造压力为100 MPa时还差, 可能与充型速度慢, 温度较低的合金液在温度更低的模具型腔中快速凝固, 封堵浇道, 增压后浇道侧的铸件已经大部分凝固, 使冲头压力不能完全施加在铸件上, 特别是施加在由于最后凝固收缩而需要施加压力的铸件溢流侧有关, 其具体原因还不十分清楚, 有待进一步分析研究。
压射压力的作用和压射比压的作用相似, 且压射压力可以持续到铸件凝固, 采用较高的压射压力可以增进合金液的充型能力, 特别是浇道尺寸较小时对铸件性能的提高作用更大, 故采用较大的压射压力也可使铸件获得较好的性能。
2.4 浇注温度对超低速压铸件的性能影响
浇注温度的选择与许多因素有关, 除研究浇注温度对铸件性能的影响外, 本文还选择了模具预热温度、脱模剂等与浇注温度相关的因素进行了研究。工艺因素对铸件性能的影响见表4。浇注温度越高, 铸件的密度和力学性能均呈先增后减的规律, 在浇注温度为690 ℃时达到最大值。这是由于温度越高, 坯料的流动性和充型性等越好, 但铝合金在熔化时易吸入氢, 且氢的溶解度会随温度升高呈指数倍增加, 故浇注温度越高, 合金液中溶解的氢越多, 压铸后铸件中气孔越多, 且氧化物量也严重增加, 故浇注温度过高铸件性能降低。浇注温度太低,硅将大量析出以游离状态存在于压铸件内, 使性能变坏。#p#分页标题#e#
压铸模的温度直接影响压铸件的质量和生产率,在每一个生产循环中, 金属液传递给模具的热量、模具自然散热及通过冷却系统传走的热量应保持平衡。
模具预热温度较高时, 可选择较低的浇注温度, 这样有助于铸件快速凝固, 获得细小的凝固组织, 从而获得较好的力学性能。在压铸过程中, 模具不断地被高温液态金属加热, 其温度不断上升。过高的模具温度,将使压铸件产生一些缺陷, 如粘模、鼓泡、崩裂、热
裂等, 同时模具长时间地工作在高温环境中, 模具材料强度下降, 造成模具表面裂纹, 致使模具寿命下降,为缓解和解决以上问题, 在压铸生产中, 往往采用喷涂或涂敷脱模剂和防粘蜡的措施, 以减缓铸件 ( 压铸合金) 与模具型腔表面的机械冲击和摩擦作用。
3 结论
( 1 ) 超低速压铸铸件的密度较高; 浇道截面积越大越有利于合金液充型, 对铸件的性能影响也越显著。
( 2 ) 铸件的性能随浇道速度的增加先提高后降低,不同截面的浇道其最佳浇道速度不同, 最佳浇道速度均低于0.6 m/s, 当浇道速度为1.2 m/s时力学性能都较差。
( 3 ) 压射压力和增压压力对铸件的性能都有影响,超低速压铸时铸造压力为100 MPa时性能最好; 在无增压条件下, 仅采用较大的压射压力也可使铸件获得较好的力学性能。
( 4 ) 在超低速基准压铸条件下, 浇注温度690 ℃、模具预热温度150℃时铸件性能较好。