文:柯春松
宁波职业技术学院
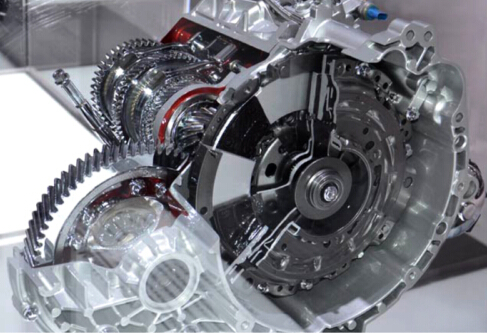
摘要:采用铸造仿真MAGMA软件对高挡位自动挡变速箱壳体的三种浇注系统和排溢系统进行充填和凝固过程数值模拟,通过分析比较模拟结果,确定了最优浇排系统设计方案和压铸工艺。同时,采用局部增压技术,对铸件中的高压油道进行增压补缩,消除了缩孔、缩松等铸造缺陷。最后通过压铸生产,验证了浇排系统和局部增压结构设计合理,为其他类似的大型、复杂变速器壳体压铸工艺设计提供参考。
关键词:变速箱壳体;数值模拟;局部增压;工艺优化
高挡位自动挡变速器因为档位间具有更加细密的速比分配、更大的速比范围,使得汽车各方面性能都得到改善。另一方面,随着对变速器性能要求的不断提高以及结构设计的不断改进,变速器结构越来越复杂,精度要求越来越高。变速器壳体是变速器的关键零件,结构复杂,加工精度要求高,目前主要是通过铝合金压铸成型,压铸毛坯的质量直接影响后期的加工质量,从而影响变速器整体性能。
本文以国内某品牌轿车高挡位自动变速器壳体为例,利用先进的铸造仿真软件MAGMA对铸件的充填和凝固过程进行数值模拟,分析比较模拟结果,优化浇排系统设计和压铸工艺。同时,采用局部增压技术,对壁厚较大的关键部位进行增压补缩,提高铸件的致密度。最后通过压铸生产,验证了模具设计和压铸工艺参数设置的正确性。
1 铸件工艺性分析
1.1 铝合金材料分析
变速箱壳体材料采用YZAlSi9Cu3铝合金 (表1)。YZAlSi9Cu3具有良好的流动性能和耐磨性能,是一种具有良好综合性能的压铸铝合金,能够较好地成型复杂结构的变速箱壳体。
1.2 结构工艺分析
变速箱壳体结构如图1所示,质量10.6 kg,外形尺寸443 mm×384 mm×248 mm,平均壁厚约为4 mm,最大壁厚达到31 mm。压铸件结构复杂,壁厚相差较大,设计有大量的加强筋板、凸台和凹槽,尺寸精度和耐磨性能要求较高。
如图1a所示,铸件A区设计有2-Ф50 mm、Ф54mm、Ф60 mm共4个轴承孔,B区有Ф60 mm的轴承孔,这些轴承孔在工作中承受较大的交变载荷,因此,不允许出现冷隔、浇不足等铸造缺陷。C区位于浇口对面,属于最后填充区域,且壁面设计有许多加强筋板,不利于充型,容易产生气孔、缩孔等铸造缺陷,影响壳体的气密性。
如图1b所示,铸件D区和E区共设计有3条高压油道,高压油道1 (图1b) 尺寸为Ф6 mm×75 mm,高压油道2、3 (图1b) 尺寸分别为Ф6 mm×210 mm\Ф6 mm×240 mm。高压油道要求在0.5 MPa检测压力下不泄露,因此,铸件内部不允许出现气孔、缩孔和缩松等缺陷。
1.3 模具设计方案拟定
通过以上分析,压铸模具可采用四面抽芯及滑块结构设计。设计要求,一方面采用数值模拟技术,优化浇注系统和排溢系统,使铸件各区域的内部质量符合要求;另一方面采用局部增压技术,使铸件D、E区的高压油道获得致密的组织结构。
2 浇注系统和排溢系统优化
2.1 不同的浇注系统和排溢系统设计方案
根据变速箱壳体铸件的结构特点,方案1 (图2a)确定了浇注系统的进浇位置、形状和尺寸。通过对方案1充填过程进行分析,方案2 (图2b) 对方案1中内浇口和溢流槽进料口的厚度做了调整,同时增加了一个辅助浇道。方案3 (图2c) 在方案2的基础上,在最后充填的末端增加了2个溢流槽,改善C区成型质量。三种不同设计方案的结构特点如表2所示。
2.2 压铸模流分析
采用模流分析软件MAGMA对变速箱壳体的充填和凝固过程进行数值模拟,下面以方案3为例,对模流过程进行分析。#p#分页标题#e#
2.2.1 建立解析模型
如图3所示,建立变速箱壳体解析模型,模型由铸件、浇注系统、溢流和排气系统组成,重力方向向下,压铸方向垂直于料柄。
根据变速箱壳体三维模型,浇注系统内浇口截面积为1 054.4 mm2,压射冲头直径为Ф150 mm,截面积为17 662.5 mm2,高速压射阶段,压射冲头速度为3.5m/s,内浇口与压射冲头的关系如公式1所示。
其中:

为压射冲头截面积;

为压射冲头速度;

为内浇口截面积;

为充填速度。
根据公式1计算可知,充填速度V充填=58.63 m/s,一般充填速度控制在60 m/s以内,以免压射速度过快,产生喷射现象,形成卷气,所以充填速度合理。
2.2.2 网格划分
大型、复杂压铸件的网格划分是压铸模流分析的重点和难点,既要考虑计算精度,又要考虑运算的效率。方案3网格划分情况如表3所示。
2.2.3 压铸工艺参数设置
压铸工艺参数设置对模流分析的结果有重要影响,铸件采用28 000 kN的卧式冷室压铸机生产,铸件、模具物理参数及压铸工艺参数设置如表4所示。
2.3 3种方案的充填和凝固过程分析
2.3.1 方案1
如图4a所示,型腔的充填时间为0.08 s,从整个充填过程来看,金属液体充填比较顺畅,充填速度中间快,两边慢,容易卷气产生气涡,形成气孔。A区充填比较理想,B区的充填流动距离比较长,充填缓慢。从图4b的温度场分布情况看,A、B区的温度相差比较大,B区温度比较低,容易出现冷隔。从图4c的凝固过程可知,A、B区凝固较好,D、E区由于产品壁厚较大,凝固较慢,容易出现缩孔、缩松等铸造缺陷。
2.3.2 方案2
在对方案1模流结果进行分析的基础上,对浇注系统和排溢系统进行改进,将内浇口厚度加大到4.9 mm,降低中间浇口的充填速度;其次,为加快B区的充填速度,增加辅助浇道,缩短B区流动距离,使金属液体整体平稳向前推进,最后为排气更加顺畅,将所有溢流槽进料口加大到1.8 mm,更加有利于气体排出。但铸件C区成为最后充填位置,需要对排溢系统进一步改进。
2.3.3 方案3
在方案2基础上,在C区新增二个溢流槽,将气体和温度低、有杂质的合金排到溢流槽中。如图5a所示,型腔的充填时间为0.07 s,金属液体整体平缓推进,充填速度基本一致,无回流包气等不良现象,C区最后填充,充填效果理想。从图5b的温度场分布情况看,产品的整个温度比较均匀,新增的2个溢流槽对延缓C区温度下降起到补偿作用。从图5c凝固可以看出,溢流槽对C区起补缩作用,除了D区、E区需要局部增压补缩外,各区域凝固均匀,无缩孔现象产生,流道最后凝固,对铸件有效的增压提供了保障。
综上所述,从方案1到方案3,浇注系统和排溢系统不断得到改善,方案3为最优方案,因此,确定方案3为最终浇排系统方案。
3 局部增压压铸技术
局部增压压铸技术就是模具型腔内金属液充型结束后,在铸件的凝固过程中,对厚壁处直接施加压力,通过强制补缩来消除关键部位的缩孔、缩松缺陷。局部增压通常采用的结构形式如图6所示,最大壁厚为H,增压压射行程为L,图6a为增压前增压杆的位置示意图,增压杆和增压杆套间的配合间隙很小,使铝液无法流入杆套内部,图6b为增压后增压杆的状态,在铝液的凝固过程中,增压杆把L处的铝液补充到铸件H处,提高H处的致密度,消除缩孔、缩松等铸造缺陷。#p#分页标题#e#
3.1 局部增压结构参数计算
3.1.1 增压过程中被压缩的液态金属体积计算
如图所示,假设局部增压处的金属质量为M,根据质量守恒定律:
式中:

为局部增压前的密度和体积;

为局部增压后的密度和体积。
因此,增压时被压缩的液态金属体积为:
3.1.2 增压压射行程L和增压杆直径D杆确定
因为

其中,

。
3.1.3 增压油缸直径D
油缸选用局部增压时,增压杆压强一般为系统压强的20~30倍,即:

30,即

,所以

。其中,

为增压杆压强(Pa);

为压铸机系统压强 (Pa);

为增压杆截面积 (cm2);

为增压油缸截面积 (cm2)。
3.1.4 增压时间
增压开始时间对增压效果影响非常明显,通常在型腔充填结束后,延迟0.8~2 s开始增压,此时液态金属表面已形成了一层薄薄的硬壳。增压开始时间越长,金属流动性越差,补缩越困难。
3.2 局部增压结构设计
变速箱壳体设计了三处高压油道,有着较高的气密性要求,由于壁厚不均匀,容易造成铸件内部缩孔和缩松等缺陷的产生,因此采用局部增压压铸技术。如图7所示,图7a为高压油道1的原结构,设计有直径Ф6 mm×75 mm的油道孔,图7a为增压前对结构进行处理,由于Ф6 mm×75 mm的油道孔无法压铸成型,只能在后期采取机加工,因此,Ф6 mm的油道孔取消,同时构建Ф15 mm×8 mm的凸台,图7b为增压后产品结构,采用直径Ф10 mm增压杆,压射行程8 mm,杆套配合采用基孔制H7/e8,杆套间隙为0.032~0.077 mm。
同理,对高压油道2、3采用局部增压的方法,如图8a所示,在高压油道上均匀构建5个Ф24 mm×8 mm的凸台,增压杆直径为Ф18 mm,压射行程8 mm,杆套配合采用基孔制H7/e8,杆套间隙为0.032~0.077mm。
变速箱壳体增压压铸模具结构如图9所示,为高压油道2、3的增压结构,由增压油缸、增压杆、增压杆套构成。高压油道1的增压油缸选择直径为Ф110 mm,吨位为8 t的油缸,高压油道2、3的增压油缸选择直径Ф140 mm,吨位为12 t的油缸。
4 产品试制
产品在28 000 kN压铸机上进行生产,模具的初始温度200 ℃。试模初期,由于模具温度低,容易在铸件B区出现冷隔。在试模后期,模具温度逐步达到热平衡,铸件缺陷逐渐消失,铸件质量逐渐稳定。对于局部增压工艺,经过调试,当增压开始时间为型腔填充结束后2 s开始增压,增压油缸压力为8 MPa时,局部增压效果最好。经气密性检测,高压油道内部质量没有出现泄漏,产品符合客户要求。
5 结论
(1) 利用数值模拟技术对变速器壳体的压铸过程进行分析,根据分析结果,不断优化浇排系统设计,最终成功开发了变速器壳体的浇排系统。#p#分页标题#e#
(2) 研究了局部增压的结构形式,在高压油道处设计凸台,通过增压杆挤压凸台,对油道起到很好的补缩效果。
(3) 通过产品试制,确定了最优的增压工艺参数如增压开始时间和增压压力,铸件质量达到客户要求。