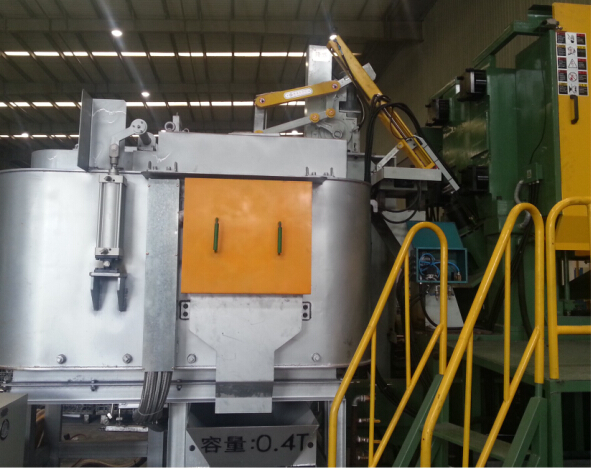
文:李顺
北京北方车辆集团有限公司
摘 要:介绍了液态模锻成形技术的概念和特点;分析了国内外液态模锻成形技术和成形设备的发展现状,并介绍了铝合金及其复合材料液态模锻成形零部件的实例;指出了液态模锻在成形技术方面存在的难点,提出了相应的解决方案;对液态模锻成形技术和成形设备的发展趋势进行了展望。
关键词:液态模锻;铝合金;研究进展
随着我国交通运输业和武器装备制造业向现代化、高速化方向发展,产品轻量化要求日趋强烈,特别是轻量化程度要求高的飞机、航天器、高速列车、汽车、舰艇、火炮和坦克等装备的重要受力部件和结构件,需要大量使用铝及铝合金锻件和模锻件来替代原来的钢结构件。例如,飞机的所有结构件,汽车(特别是重型汽车和大中型客车)的轮毂、保险杠、底座大梁,坦克的负重轮和炮台机架,直升机的动环和不动环,火车的气缸和活塞裙都已应用铝合金模锻件来制造。而传统的模锻技术已不能完全满足这些铝合金关重零部件的制造需求和使用性能,正是这种需求使得液态模锻和半固态模锻成形技术的研究受到广泛的关注。
液态模锻成形工艺是建立在压力下金属凝固原理基础上,将一定量的熔融金属直接浇入金属模腔,随后在压力的作用下,使熔融或半熔融的金属液发生流动并凝固成形,从而获得具有近净形状的固态零件。其优点是省力、节能、材料利用率高和工序简单,制件接近零件的最终尺寸,性能接近热模锻件。
液态模锻虽然具有上述优点,但都是以凝固为主,辅以少量塑性变形的成形技术,在成形过程中存在合金凝固过程,是由于制件形状、合金成分、应力状态的影响总是存在着不均匀的应变场。当金属在凝固的末期(脆性温度区),延展性或塑性不足以承受当时应力产生的应变量时,会发生沿晶断裂,即热裂纹,这是凝固成形形成裂纹缺陷的一般规律;因此,对铝合金液-固态模锻过程组织性能不均匀性的研究具有特别重要的意义,其理论研究成果对铝合金液-固态模锻成形技术具有重要的应用意义。另外,研究液-固态模锻成形的凝固过程和控制方法,对于实现液-固态模锻制件组织性能均匀化的精确控制有重要指导意义,可以为轻质合金制件采用近净成形技术奠定理论基础。
1 液态模锻成形技术研究进展
1.1 工艺流程
液态模锻是一种少无切削加工技术。其工艺流程如图1所示,可分为金属熔化和模具准备、浇注、合模和施压、卸模和顶出制件。
1.2 研究进展
1.2.1 液态模锻成形技术研究进展
液态模锻是一种借鉴压力铸造和热模锻工艺而发展起来的金属加工技术。1937年,前苏联A.B.乌里托夫斯基就曾全面探讨过液态模锻技术。初期,液态模锻的研究主要集中在铜合金上,第二次世界大战期间,采用该工艺成功地进行了铜合金轴承套的大批量生产,这标志着液态模锻技术开始从试验阶段向工业化应用阶段转移。到1964年,前苏联采用该工艺生产的厂家已有150家,约200多种产品,并以B.M.普俩茨基发表的专著《液态金属模锻》为标志,使这项技术在生产中得到确立。
20世纪80年代,液态模锻技术在日本、美国、英国、前西德、波兰、法国、比利时、意大利和巴西等国家得到较快发展,用于铝合金、铜合金、铸铁和碳钢等金属制品生产。其产品实例有爱国者导弹前仓盖、壳体预制坯、齿轮、活塞、轴瓦、形状复杂的管接头、铜合金衬套、摩托车减震器、阀门、自行车零件和家用电器零件等。目前,有色金属液态模锻技术早已应用于生产并获得成功;黑色金属液态模锻技术尽管难度和深度较大,发展缓慢,但也正在逐步进入小批量生产阶段。
液态模锻复合材料在航空工业中的应用如下:美国把液态模锻复合材料技术用于F15战斗机,战机质量减轻20%;美国还耗资1500万美元,研制了连续碳化纤维增强6061.2124铝合金,分别用于战斗机的垂直尾翼和翼根,其翼展为3810mm,翼根长1026mm;原苏联也把液态模锻复合材料用于安-28、安-27飞机上。
液态模锻复合材料在航天工业中的应用如下:美国DWA公司应用石墨纤维增强铝基复合材料为NASA和Lockheed公司制造卫星上的波导管,其波导管不但轴向刚度好,而且比原有石墨/环氧-铝层复合制造的波导管轻30%;航天飞机析架、卫星抛物面天线骨架等也采用了液态模锻复合材料。液态模锻复合材料在兵器工业中的应用如下:美国ARCO公 司 开 发 的SXA材料,代替了ALS14410材料制造装甲车履板,减轻了装甲车质量,提高了寿命,该材料也用于导弹导航系统中仪表外壳,战术坦克 上的光学红外瞄准镜部件;美国LTU公司应用SiC/Al复合材料制造了战术导弹发动机壳体、航板;美国海军利用SiC/AI复合材料制造 鱼 雷 和 水 雷 外 壳 等;美 国1969年 研 制 的M60A2主战坦克在比1960年研制的M60坦克增大火炮口径(从102mm增大到152mm)的情况下,通过在弹药架、炮塔座圈、负重轮、拖带轮和油箱等制件上采用铝合金,使得M60A2车质量较M60车质量亦有减轻(从44t减至46.3t);1967年装备的M551轻型侦察坦克由于广泛采用铝合金制件,如车体、负重轮等,车质量仅有16t,该战车机动性较高,能空投、空运、水陆两用;装备的XM-723步兵战车采用5083铝合金、7093铝合金装甲和负重轮等制件,全车质量仅19.5t,便于用火车、飞机和其它交通工具装运;20世纪80、90年代,世界各军事大国在装甲车研制中均大量采用铝合金及铝合金复合材料,如俄罗斯的T-72、БМ∏-3步兵战车、德国的TH495步兵战车、美国的AIFV装甲步兵车、法国的“凯撒炮”155自行火炮、意大利“达尔多”步兵战车等。我国液态模锻技术从1957年起开始研究,20世纪80年代后期,该技术逐步发展并陆续用于生产。在液态模锻产品方面主要是用于汽车、摩托车等车辆的零部件,如汽车活塞、空调机阀体、法兰盘、摇盘、空心传动轴等,哈尔滨工业大学研制的铝合金负重轮、螺旋桨具有代表性意义;此外还用于高压锅、拉丝机收线盘、法兰、电动机端盖、迫击炮下体和机枪枪管支架等。国内利用纤维复合材料制造不同性能要求的零件也有报道,例如,双金属、纤维强化性活塞和纤维复合材料模具等。哈尔滨工业大学杜之明在与北京北方车辆集团有限公司研究人员合作研究的基础上,开发了铝合金液态模锻成形技术以及铝基复合材料成形技术,并由杜之明首次提出了半固态-塑性变形一体化模锻的技术,采取理论分析、数值模拟和试验研究相结合的技术路线,在液态模锻成形技术研究方面取得了一定经验,开发了一系列的液态模锻成形工艺,制备了一大批铝合金及铝基复合材料负重轮和铝基复合材料履带板等零部件,实现了车辆的减轻质量和节能降耗。
1.2.2液态模锻成形设备研究进展
在液态模锻技术发展方面,日本的产业规模、技术发展水平和应用上都处于世界前列。在20世纪80年代,日本宇部公司成功开发了HVSC和VSC系列液态模锻机,使液态模锻技术在日本得到迅速发展。该公司的液态模锻机的液态模锻过程可由计算机编程,并显示精确控制和重要工艺参数,确保生产过程全自动进行。截至目前,日本宇部公司已销售液态模锻机307台,设备最大合模力达35000kN。日本丰田公司的轮毂生产厂拥有14台VSC系列液态模锻设备,已形成年产400万只高档汽车铝轮和120万只复合材料活塞的生产能力,并已在23种车辆上得到使用。近年来,日本的液态模锻新产品主要有用于日 本日产 汽车 和 马 自 达 汽 车 的A356合金承力件—汽车转向节、下杠杆,以及要求精确成形并要求耐磨、耐压的汽车空调压缩机铝涡旋盘等。
欧美各国由于压铸和热模锻技术比较强,过去对液态模锻技术不够重视,但近年来有明显改变。大部分的压铸机生产厂家在普通卧式压铸机上推出液态模锻新技术,例如瑞士布勒公司率先在卧式压铸机上实现液态模锻。该公司还开发了新一代实时压射控制机构,能对速度和最终压力曲线进行编程,以适合压铸零件的几何形状,实时控制质量。布勒公司压铸机设备开发出的液态模锻产品有滑轮、皮带轮、发动机支架、托架、连杆和雪车离合器等。荷兰Prince Machine公司、法国JL公司以及美国Grandville和Michigan公司联合开发的满料筒液态模锻技术,也是在普通卧式压铸机上实现液态模锻过程。其工艺过程分为3个步骤:首先是向压射料筒内100%充满金属液;然后缓慢地把金属液平稳地压入铸型型腔;最后让金属液在高压力下凝固。在产品生产上,为福特汽车公司开发生产了质量为10kg的A380铝合金的下曲轴箱,为通用汽车公司生产了质量为7kg的A356-T6铝合金的后上控制杆。
中国液态模锻技术理论水平及所开发产品等方面,与一些先进国家是相当的;但液态模锻的生产批量、制件质量档次还有相当的差距,其中最关键的是液态模锻设备的差距。在国内工作的100多台液态模锻设备中,约80%是经改装的普通液压机,进口的先进设备只有十几台,因而在生产效率、产品档次和生产成本等方面有较大差距。使用普通液压机,设备不稳定性对制件质量影响较大。由于液态模锻模具长期处在较高温度下工作,会造成液压机机油温度升高,黏度降低,进而导致设备油路系统内漏。操作者仅凭经验来控制某些参数,很难保证制件质量的一致性,最终导致产品尺寸超差,甚至造成成批不合格。另外,国内没有定量浇注设备的厂家,国外设备较昂贵,也是制约国内液态模锻技术发展的因素之一。
近几年,国内有少数企业开始生产出小型液态模锻机,如佛山市顺德区华人机械制造有限公司生产的Y28立式液态模锻机,合模力可达1500kN,能生产铜套和铝套。我国台湾地区在液态模锻机研究上有一些进展,据相关报道,台湾久大油压铸机公司在2000年就开发出了自动化液态模锻机,可满足汽机车、自行车产业零件轻量化生产的要求,最大合模力达到了1600kN。目前,在大陆上海三基的大型液态模锻机开发成功。
2 液态模锻成形技术难点及其解决方法
2.1 技术难点
液态模锻成形技术难点如下。
1)大型复杂零件的组织性能不均匀。用轻质合金替代原有钢质材料制造形状复杂的关重件,采用压铸不能满足性能要求,采用固态锻造也难以成形。液态模锻是成形这类零件最有前途的方法,但有可能因为制件各部分施压不均匀导致相应的组织性能不均匀问题。在合金凝固过程中,由于制件形状、合金成分和应力状态的影响还存在着不均匀的应变场,其在凝固的末期(脆性温度区),当延展性或塑性不足以承受应力产生的应变量时,会发生沿晶断裂,即热裂纹。此外,在成形过程中,由于始锻时有一定金属与模壁接触形成固相,施加载荷后成形制件各部分的应变不均匀,产生微裂纹的可能性进一步提高。
2)铝基复合材料的耐磨增强。特殊性能要求的零件,对复合材料的制备提出了更高的要求。例如,铝合金履带板需要具有高强度,还需要具有一定的韧度和耐磨损性能。高体分率增强能满足其耐磨损性能,但延伸率低;低体分率增强则不能满足其耐磨损性能。
3)尺寸精度和表面质量控制。模具表面粗糙度、模具温度、涂料、浇注温度和浇注质量等对制件尺寸精度和表面质量有着重要影响。笔者认为目前金属液的熔炼质量和浇注质量是最主要的影响因素。大型零部件液态模锻成形过程的液态金属的浇注远不如压铸成形。熔融金属从熔炼炉取出到成形模膛,液面上会立刻形成氧化层,严重影响制件表面质量,人工浇注液态金属的质量不佳使制件的尺寸误差较大。
2.2 解决技术方法
2.2.1 液态模锻成形过程组织性能的均匀性控制技术
杜之明在已开展的汽车铝合金活塞、特种车辆履带板、铝合金轮毂模拟件和筒形件等液态模锻研究工作中发现,在常规单向加载进行的成形过程中,由于制件各部分壁厚、应力状态不同,各区域的性能存在差异。以筒形件为例,如图2所示,图中左侧为常规单向加载的液态模锻成形方式,由于直壁厚度大于底部厚度,加载后底部最先完成凝固,继续加载,底部几乎承载了全部载荷而进行塑性变形状态,限制和减缓了冲头的继续下行;而此时直壁部分可能尚未完全凝固。直壁和底部存在较大的不均匀凝固,从而在直壁与底部转角处产生较大的拉应变,易产生微裂纹。常规单向加载条件下铝合金液态模锻制件在制件直壁和底部转角处出现微裂纹(见图3),微裂纹可以通过超声波、涡流等进行无损检测和射线法、透射电镜进一步进行观察。观察到内部裂纹扩展成外部宏观裂纹,如图4所示。
程远胜等通过复合加载方式,即在最后凝固区域或易产生宏观缺陷的区域施加局部载荷和金属补缩,改善了凝固成形的应力场获得组织性能均匀的制件(见图5),取得了一些成果,但是对局部加载和
局部补缩对制件凝固均匀性和性能均匀性的影响还没得出数量的关系,需要进一步深入研究。
2.2.2
铝基复合材料耐磨增强增润技术铝合金履带板需要具有高强度,还需要具有一定的韧性和耐磨损性能,高体分率增强能够满足其耐磨损性能,但延伸率低。例如,采用SiCp·Al2O3混杂增强制备铝合金复合材料,体分率>20%时,其耐磨损性能超过对磨材料GCr15,但延伸率δ≤3%。此问题的解决途径是:
1)寻求能够降低铝基复合材料摩擦系数的增强材料和制备工艺,提高低体分率增强复合材料的耐磨损性能,从而同时满足强度和韧性的要求;
2)在增强材料上涂覆增润材料,因为一般铝基复合材料的摩擦因数为0.6~0.8,若使其降低0.2~0.3,可以解决该难点。
实践表明,增强体涂覆是增强体表面改性比较成功的技术手段之一。涂层除对增强体具有一定的保护作用外,对提高增强体与基体的润湿性和控制界面反应的发生也起着积极的作用。采用增强体增润涂覆后,在相同体积分数增强时,可提高材料的韧性,这样就可解决高体分率增强时,延伸率低的技术难点。
2.2.3 液态模锻成形制件尺寸精度和表面质量控制技术
影响液态模锻成形制件尺寸精度和表面质量的因素主要有3个:
1)模具成形型腔的表面粗糙度,型腔表面越光滑,制件表面质量越好,尺寸精度高;
2)模具表面涂料,涂料隔热和脱模有2种功能,但涂料过厚或者不均匀,就会影响表面质量和尺寸精度;
3)前面已介绍的浇注液态金属的氧化和质量控制水平。随着模具加工业和涂料工业的发展,前2个因素已不是技术难点;因此,液态模锻成形制件尺寸精度和表面质量控制主要在于合金液的熔炼质量和浇注质量多少的精确控制,亦就是定量浇注设备的研制。
目前,国内还没有专门生产液态模锻浇注设备的企业。现有的定量浇注设备都是用于压铸,一次浇注的合金量较小,浇注方法主要有2种:一是容积法,采用螺杆泵或机械勺定量浇注,如重庆硕龙科技有限公司使用螺杆泵和高温浇注管定量浇注;二是电磁泵流量控制法,如北京北方恒利公司和中北大学的。上述2种方法均不能用于大质量液态模锻定量浇注。容积法的螺杆泵推进注射量较小,只能用于压铸工艺;机械勺不便于运输,环境差。经实践证明,电磁泵流量控制法没有充分考虑液态金属在黏性流动过程中的凝固损失,难以实现定量的精
确控制。为实现定量浇注精确控制,有研究者提出采用质量法定量浇注控制,即通过浇包的装入合金的质量信号来控制一次合金浇注量。笔者对国内外定量浇注设备进行了深入的调研,提出了技术原理,并给出设备结构简图(见图6)。
3 结语
随着科技的飞速发展,新工艺、新技术不断涌现,传统的制造业正面临着严重的挑战。展望铸、锻结合的先进的液态模锻技术,也要面对更多的技术要求和激烈的市场竞争,需要继续完善和发展。
1)目前,国内外学者对液压模锻技术的力学成形理论、模具热应力分析、强韧化材料机理、液锻凝固速度的测试及液态模锻缩孔的计算机模拟研究做了理论创新和研究,取得了一定的成效,也进一步完善了液态模锻理论体系。
2)由于操作简单、实用,液态模锻技术成为制备铝基复合材料最常用的方法之一。采用液态浸渗方法用于制备铝基复合材料,可实现材料制备与零件成形一体化工艺,增强材料可以选用陶瓷颗粒、晶须、纤维增强和混杂增强。
3)液态模锻技术应用主要集中在铝镁合金、高温合金和复合材料的成形,随着模具材料的发展,也在向黑色金属成形方面发展。如近期从国外进口的离心机钢质转毂就是采用液态模锻生产的,零件直径为260~780 mm,若采用热模锻生产全系列产品,锻造设备最大压力需要100000kN,而采用液态模锻,锻造设备最大压力只需30000kN。
4)液态模锻技术有助于节能降耗,将获得更多应用。液态模锻与铸造相比,不用设置浇冒口或余块,金属液利用率>90%,使制件性能大幅度提高。与锻造相比,可以制造形状复杂的制件,并实现毛坯精化,减少后续加工量,节省了材料,特别是有色合金材料,可节省50%~70%。液态模锻是液态金属充填,所需变形压力小,是热模锻成形压力的1/5~1/3,可以利用小设备实现大制件。
5)液态模锻设备研究远不如压铸机,主要是利用普通油压机辅以人工操作,效率较低。近10年发展速度较快,实现了从模具清理、喷涂、施压到取件全自动化,其中以日本的宇部公司的立式和卧式2种系列液态模锻机最为成功。
6)需要提高大型复杂制件性能和实现精确控制。液态模锻是以凝固为主辅以少量的塑性变形的成形技术,金属在凝固过程中的均匀性、成形载荷分布对制件性能的影响较大,需进一步深入研究。