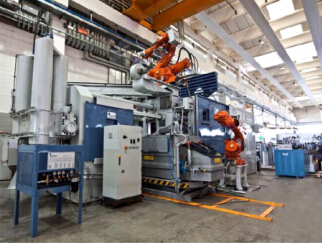
文:柯美元,陈学锋
顺德职业技术学院
摘 要:弹簧壳体零件壁厚较大且不均匀,铸件多孔位,分布密集,给压铸生产带来了很大的困难。 为生产出合格的铸件,将速度比降至 10.4,并结合型芯表面涂层技术,解决型芯冲蚀和粘模的问题;通过提高浇注温度、增大溢流槽,增设辅助流道等措施解决了浇注不良的问题;通过延长冷却时间,解决了铸件脱模开裂的问题。 通过工艺改进,最终生产出了合格的压铸件,产品不良率小于 0.5%。
关键词:压铸;铝合金;速度比;厚壁
在汽车工业,汽车压铸件占压铸件总产量达到了 65%以上。 随着一系列压铸新工艺新技术的研发应用,如真空压铸、充氧压铸、挤压铸造、半固态压铸和超低速压铸等, 压铸件的性能得到大幅提高,从而进一步扩大了压铸工艺的应用范围。
在压铸合金中,铝合金铸造性能好,密度小,比强度高,耐腐蚀性、导热性、导电性能好,切削性能良好。 因此,铝合金在压铸行业中的应用最广泛,其用量高于其他有色合金。 随着人们对节能、低碳和轻量化要求的日益提高, 汽车中的许多零部件,如发动机缸体等,逐渐被压铸铝合金取代,以铝合金制造汽车零部件成为汽车轻量化的战略目标。
刹车系统空气干燥弹簧壳体是汽车零部件中的重要零件,性能要求高,且壁厚较大,又很不均匀,给压铸生产造成了很大的困难。 通过反复生产实践,并不断优化工艺参数, 最终生产出了合格的铸件,实现了稳定生产。
1 压铸工艺分析
弹簧壳体零件如图 1。 该产品平均壁厚 4 mm以上, 局部壁厚超过 8 mm, 局部筋位壁厚小端 2.5mm。 产品轮廓总长 190 mm,宽 92 mm,高 42 mm。铸件有耐 1.5 MPa 的气密
性要求, 材质为铝合金A380,铸件质量为 0.55 kg。 该铸件总的工艺特点是壁厚较大且不均匀,孔位较多,分布较密集,压铸时成形通道多起伏,其他工艺条件一般。
由于弹簧壳体是保护壳体零件,零件壁厚较厚,并有筋位,以加强壳体的强度和刚度,铸件有气密性要求,因此铸件不得有缩松、缩孔和气孔等缺陷。 对于厚壁件,防止缩松、缩孔是重点和难点。 压铸生产时,工艺上要求填充流量要大,内浇道要厚,浇注温度要低。 同时,为了防止卷气产生气孔,要求填充速度要尽量低。而弹簧壳体零件由于壁厚不均,且孔位多, 成形通道多起伏, 当浇注温度和填充速度过低时,容易产生浇注不良的问题。 因此,实际的工艺参数需要在生产实践中, 根据具体情况进行反复的权衡、调整和优化。
2 初始工艺方案
2.1 压铸设备的选择
设定铸造压力为 100MPa,按铸件投影面积的 1.5倍计算胀型力为 0.19×0.092×100×106×1.5=2622(kN)。因此,选择350T 冷室压铸机。
2.2 浇注系统设计
浇注系统设计方案如图 2。 采用 3 个内浇道浇注,10 个溢流槽排渣,12 个排气槽排气。 通过内浇道截面的质量为 0.73kg(包括铸件和溢流槽的质量),铸造总质量(包括浇注系统、铸件和溢流槽等)为 1.03 kg。中间内浇道截面尺寸为 24.0 mm×2.5 mm,两边的两个内浇道尺寸为 26.0 mm×2.5 mm。 因此,内浇道截面积为 F
内=(26+24+26)×2.5=190(mm
2)。
压射冲头的直径为 60 mm,可计算出压射冲头的截面积为 F
冲=2 826 mm
2。因此,速度比为 F
冲/F
内=14.9。
设定压射冲头的高速速度为 3 mm/s,则内浇道的理论填充速度为
3 mm/s×14.9=44.7 mm/s
压射冲头的理论高速行程为
S
高=m(ρF
冲)
-1=0.73(2.6×10
3×2826×10
-4)
-1×10
3=99 (mm)。
式中 S高为压射冲头高速行程,m 为流经内浇道的质量,ρ 为 A380 铝合金的密度,F冲为压射冲头的截面积。
2.3 压铸试产工艺参数
压铸试产时,采用手动喷雾、手动取件,其主要工艺参数如表 1。

3 试产结果、原因分析与工艺改进
3.1 第 1 次试产结果、原因分析与工艺改进铸件可基本成型, 但远离内浇道的孔壁及筋位生产至 500 模次左右, 压铸模具在近浇口的几个柱位型芯发生较明显的冲蚀, 铸件粘模并产生粘缺现象,导致无法继续生产。
由图 2 看出,内浇道正对着型芯,型芯在高温、高速的金属液的反复冲刷下容易产生变形和磨损,从而导致铸件粘模。 由于铸件上孔位较多, 周围都分布有孔位,且孔位分布较密集,内浇道无法避开型芯。 有鉴于此,我们从以下两个方面进行改进:一方面通过加大内浇道截面积来降低充填速度, 从而减缓对型芯表面的冲刷, 将内浇道厚度由 2.5mm 加大到 3.5mm, 从而将速度比由原来的 14.9 减小到 10.6;另一方面,通过涂层技术,在型芯表面镀一层很薄的纳米陶瓷,以提高型芯表面的硬度和耐磨性能。
3.2 第 2 次试产结果、原因分析与工艺改进
采取以上工艺措施之后,进行了第 2 次试产。试产结果显示,近浇口型芯粘模现象已经消除,可以实现连续生产。 铸件冷隔、水纹现象有改善,但是两侧柱位的冷隔和水纹现象仍然较为明显。 为了进一步改善冷隔和水纹问题, 将铝液温度从 670 ℃提高到680 ℃, 结果 铸件脱模后又发生了轻微开裂 。 因此, 单靠提高浇注温度来改善冷隔和水纹问题是行不通的。
除了提高浇注温度以外, 生产中还常常采用减薄内浇道、以提高充填速度的措施,来改善浇注不良的问题, 但提高填充速度将会增大粘模的风险。 同时, 减薄内浇道必然会影响到厚壁件补缩效果的实现。 所以,通过加大充填速度来改善冷隔、流痕的问题是不可取的。
压铸时,铝液在填充路线上的起伏多,铝液经过长距离的跋涉, 温降比较大是产生浇注不良的主要原因。 采取的工艺措施主要有以下几个方面。 首先,加大冷隔、水纹部位外围的 4 个溢流槽的容积,可以加大冷料的排除,有利于平衡定模模温。 其次,浇注温度仍然提高到 680 ℃,同时,将冷却时间(铸件留模时间)从 6 s 提高到 10 s,以避免铸件脱模时开裂。第三,为解决两侧柱位的冷隔、水纹问题,取消左右两侧近浇口的溢流槽,改为两个辅助流道,如图 3。两个辅助浇口的尺寸为 1.2 mm×2.5 mm。 修改后,F
内=(26+24+26)×3.5+1.2×2.5×2=272(mm
2),速度比为 F
冲/F
内=10.4。
3.3 第 3 次试产结果

第 2 次工艺改进后,进行了第 3 次试产,试产结果表明:①粘模现象,确保了生产能够连续进行;②在较低的充填速率下,产品出现冷隔、流痕的问题基本解决;③铸件脱模后基本
没有开裂现象。进行批量压铸生产后,产品的气孔、缩孔不良率小于 0.5%。 对铸件进行测漏检测也没有出现不良品。 第 3 次试产后的铸件如图 4 和图 5。
4 结论
对于一般压铸件, 资料和经验推荐的速度比为15~25,但在生产实践中 ,需要具体问题具体分析 。对于弹簧壳体这一厚壁件, 其速度比可以降低到10.4。 压铸过程是多方面因素共同作用的复杂过程,需要对速度比、合金温度、压射速度、模具温度、冷却时间等参数的不断调整和优化, 才能取得令人满意的结果。 在铸造生产中,要根据不同的问题,分析和找出问题的实质,有针对性地采取措施加以解决。
在刹车系统空气干燥弹簧壳体零件的压铸生产中,通过增大内浇道横截面积,降低填充速度,并结合型芯表层镀膜技术, 解决了型芯冲蚀和粘模的问题;通过提高浇注温度,增大溢流槽容积,并增设辅助流道,解决了铸件浇注不良的问题;通过延长冷却时间,解决了铸件脱模开裂的问题。经过以上工艺措施的改进,最终生产出了合格的铸件,产品不良率小于 0.5%,实现了稳定供货。