文:中国汽车工业工程有限公司 韩桥 兰冬云
摘要:阐述了液态模锻压铸工艺的特点和产品优势,以及液态模锻压铸工艺在铝合金汽车结构件生产上的应用。同时简单介绍了液态模锻压铸工艺的生产流程和设备选取。指出了在铝合金汽车结构件生产上采用液态模锻压铸工艺是一种行之有效的先进技术。
关键词:液态模锻压铸 ; 铝合金汽车结构件 ; 产品优势
1、 前言
液态模锻压铸技术作为先进的压铸成型技术,在国外已经得到20多年的成熟应用。其原理是对进入液态模锻铸型型腔内的液态或半固态的金属或合金施加较高的机械压力,使其成形和凝固,从而获得铸件的一种工艺方法。由于高压凝固和塑性变形同时存在,金属在压力下结晶凝固并强制消除因凝固收缩形成的缩孔缩松,因此可以获得组织致密、无气孔缩松等造缺陷的液态模锻铸件。
充型和凝固是液态模锻工艺中两个重要的环节,低压充型和快速高压补缩凝固是液态模锻铸件组织致密的保证。
充型:全自动液态模锻机充型采用液压驱动,低压充型,下端进料,上端排气,充型速度无级可调,排气通畅,充型过程无卷气,铸件内部几乎无气孔缺陷。
凝固:液态模锻需要借助较大的机械压力(100MPa 左右)完成铸件凝固过程中的补缩,液态金属在此高压下凝固时,组织细小、致密,同时无气孔,缩松等缺陷,所得铸件的综合性能较高,可接近锻件。
2、 液态模锻压铸工艺特点
液态模锻是铸锻相结合的一种新兴工艺,它既具有铸造工艺简单、生产成本低、可制件形状复杂的优点,又具有模锻产品晶粒细密、组织均匀、力学性能好、成型精度高的特点。
①在成形过程中,尚未凝固的金属液自始至终在等静压的作用下结晶凝固、流动成形;已凝固的金属层在压力下发生塑性变形,具有热变形组织,晶粒细小,组织均匀,同时压力使制件外侧紧贴模具内壁,使工件形状尺寸准确。
②由于先结晶凝固层产生塑性变形,要消耗一部分能量,因此金属液经受的等静压不是定值,而是随着凝固层的增厚而下降。
③固液区在压力作用下,发生强制性的补缩,从而能消除制件内部缩孔疏松等缺陷,提高了制件力学性能。
④与普通热模锻相比,金属液的流动性远大于固体金属,充填模具型腔的性能较好,能够用一副模具一次成形形状比较复杂的制件。
⑤密度、力学性能基本等同模锻件。
⑥由于无需冒口补缩,因而金属利用率高,生产过程节能环保。
⑦可铸造变形合金,因此可做表面阳极氧化。
⑧液态模锻铸件与压铸铸件不一样,可以进行固溶及时效热处理,以大幅度提高铝合金的力学性能。液态模锻工艺与常用铸造工艺的指标比较见下表 1。
3、在铝合金汽车结构件上的应用
随着汽车行业轻量化趋势明显,对铝合金部件拉动巨大,未来几年是汽车结构件轻量化发展的黄金时期,液态模锻压铸工艺是目前最经济适合生产汽车结构件的成型方式。液态模锻压铸工艺已经在日本丰田、本田、马自达等汽车企业和欧洲的德国、意大利等国得到广泛应用,生产的产品涵盖包括转向节、控制臂、车轮、副车架、连接杆等大量汽车结构件上和坦克履带轮等军工产品,技术和工艺风险较少。
目前,国内外汽车厂家采用液态模锻压铸工艺所生产的铝合金汽车结构件主要零部件有铝合金活塞、铝合金轮毂、铝合金衡量(十字粱)、转向节、气囊支撑臂、汽车控制臂、制动卡钳、铝合金发动机支架、铝合金变速箱以及铝合金空压机连杆等。国内汽车厂家里如东风汽车公司、吉利汽车公司、比亚迪汽车公司、广汽集团、长城汽车等大型汽车厂家都在采用液态模锻压铸工艺所生产的铝合金汽车结构件,并且使用的数量和比例在逐步增加。
图 1 和图 2 为采用液态模锻压铸工艺所生产的典型铝合金汽车结构件。
4、 典型产品优势分析
4.1 铝合金汽车转向节优势分析
汽车转向节是汽车极其重要的安全结构件,在转向、紧急制动、侧滑、越过不平路面时承受多种疲劳载荷作用和意外事件的冲击。传统汽车转向节主要由球墨铸铁铸造而成。为了汽车轻量化和提高簧下性能,国外自十年前左右开始研发高性能铝合金转向节,目前欧美、日本等许多汽车已规模化使用铝合金转向节,由现有的铸铁件、锻造件向铝合金精确铸造新产品的升级换代,以实现转向节产品的轻量化、高性能化和低成本化。目前国内已有企业掌握其制造技术,成功开发了汽车转向节产品,并进行量产化。
液态模锻代表产品转向节的各类工艺及成本对比如表 2。
从表中数据,可以看出液态模锻工艺生产的铝合金汽车转向节具有以下优势。
①产品质量可以得到保证。液态模锻工艺生产的转向节组织致密、气密性好,性能接近锻件,优于重力铸造和差压铸造。
②产品重量轻,有利于汽车轻量化,符合国家产业政策。从表中可以看出,液态模锻工艺生产的转向节分别比重力铸造工艺和差压铸造工艺生产的转向节要轻1kg 和 1.1 kg。
③单件产品采购价降低。对于客户来讲,最终采购成本是要摊到每辆整车的每个零件上的。对于同样数量需求的转向节,例如1万件,不同铸造工艺的采购成本为:液态模锻 =2.3×75×104=172.5( 万元 );重力铸造 =3.3×60×104=198( 万元 );差压铸造 =3.4×60×104=204( 万元 )。对比可以看出,虽然液态模锻转向节的销售单价(按元 /kg 计)高于其他两种工艺,但是对于客户而言,由于产品重量降低,同等数量的转向节综合采购成本反而显著降低。因此,在综合价格优势方面液态模锻是占优的。
④产品尺寸精度高,减少机加工余量,从而降低内部机加工成本和加工废料量。
⑤产品结构更合理,给予汽车底盘各零部件预留出更多的安装空间。产品自重的降低和尺寸精度的提高,在满足关键尺寸和必要结构的前提下,带来的必然是产品体积的减小,也可以形容成“瘦身”。“瘦身”的好处就是尽量少的占用拥挤的底盘安装空间,使别的底盘零部件有更大的灵活性和自由度。
采用液态模锻压铸工艺生产的铝合金汽车转向节各项性能如图 3。
图3 铝合金汽车转向节各项性能
4.2 铝合金气囊支撑臂优势分析
气囊支撑臂是比较特殊的汽车结构件。目前,只有在新能源电动汽车上才会使用气囊支撑臂,在传统燃油汽车中不使用这个结构件。由于目前汽车用动力电池发展未取得突破进展,为获得续航能力强的电动汽车就必须坚定的走轻量化道路,铝合金件的应用极大的降低了电动汽车的整车自重。气囊支撑臂作为重要的电动汽车结构件,采用铝合金材料是势在必行的。目前,采用液态模锻压铸工艺已经成功批量生产气囊支撑臂,而且也是目前唯一一种成功生产此类产品的铸造工艺。
5、 液态模锻压铸工艺生产流程和设备选用
5.1 生产流程
一般情况下,液态模锻车间分为铝液熔化、液态模锻和铸件清理三个工段。
①铝液熔化工段
铝合金熔化炉的最佳选择是采用燃天然气的集中快速熔化保温炉,因为该炉具有以下优点:采用洁净燃料,污染物少,对车间环境影响小;熔化速度快,氧化率低,材料损失少,金属烧损率 <1.5%;炉内设置有铝液液位检测装置,防止溢流发生;铝液温度控制精度可达 ±5 ℃,铝液的质量高;该炉采用优质耐火材料,使用寿命可达 3~5 年。
在铝液熔化工部设置精炼除气设备,并采用无毒(无公害)精炼、除气熔剂来对铝合金液进行精炼、除气处理。同时设置浇包预热装置进行浇包的预热。采用带铝液保温包叉车,负责向每台液态模锻机的保温炉内分配合格的铝合金液,供浇注用。
②液态模锻工段
液态模锻工段所用铝液从铝液熔化工段通过叉车运送至每个液态模锻机的保温炉内。液态模锻机全部配备自动喷涂料机,自动取件机械手、铣冒口机、飞边毛刺打磨机、铸件输送机。全自动液态模锻机采用计算机管理系统,实现整个铸造过程的检测、存储、计算和记录。
③铸件清理工段
铸件经过锯冒口,打磨飞边毛刺后,人工码放在料框里。然后通过输送系统送至热处理工位部分(需要人工打磨的则运送至人工打磨工位)。铸件的热处理采用 T-6 连续式热处理炉,铸件筐通过辊道进入热处理炉,进行固溶、时效、淬火等工序。
热处理后的铸件,输送至抛丸工位,抛丸清理采用悬链式抛丸清理机,以提高生产效率。抛丸后的铸件需经过荧光渗透、X 射线探伤等检测手段,检测合格的铸件装筐运送至机加工车间进行机加工。
液态模锻车间生产工艺流程见图 4。
5.2 设备选用
液态模锻机是液态模锻压铸工艺生产中的关键设备,一般配置其他辅助设备形成一套液态模锻机单元。在液态模锻机单元中可以完成铝液保温、铝液浇注、模锻成型、自动取件、铣冒口、清理飞边毛刺等功能,从液态模锻机单元出来的铸件可以进行下一道工序。
典型的液态模锻机单元布置如图 5。
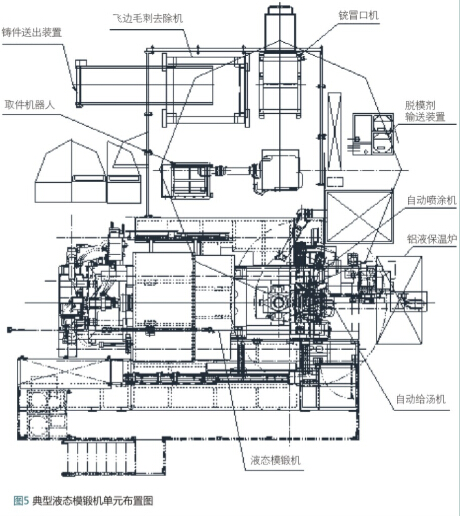
6、 结语
(1)液态模锻压铸工艺作为一种先进的铸造工艺已经在铝合金汽车结构件上得到成功且广泛的应用。
(2)相比于重力铸造、差压铸造等传统铸造工艺,液态模锻压铸工艺生产的铝合金汽车结构件具有内部质量好、产量重量轻、产品单价采购件低、尺寸精度高、产品结构合理等优点。因此液态模锻压铸工艺必将得到迅猛发展。