文:杨 蕊
东北石油大学 机械科学与工程学院
图1 Mercedes-Benz C-Class 减震器支座
摘 要 通过对白车身前舱减震器支座的两个冲压件改制成一个铝合金压铸件以实现汽车轻量化是一种可行的途径,并符合当前节能减排的要求。针对改制后的铸件模型,基于 Procast 对其进行压铸充型过程的模拟分析,同时结合合金熔液的流动状态及卷气情况进行结构优化。仿真结果表明,在合适的工艺参数下,该类零件可以达到满意的充型效果,对实际生产中实现汽车减重具有一定的指导作用。
汽车轻量化作为当今汽车发展的潮流, 已得到了许多公司的重视。而要实现轻量化,主要在于结构的优化和轻质材料的应用。目前,已有很多汽车厂家研究轻质材料以及相应的新工艺在车身上的应用。在2014 年的欧洲白车身会议期间,奔驰公司展示的Mercedes-BenzC-Class 轿车前舱就采用了压铸工艺生产出的一体化的减震器支座, 如图1 中箭头所指部件。而通用汽车集团旗下的一款凯迪拉克轿车也同样采用了一体化压铸铝减震器支座, 如图2中箭头所指部件,并且采用与美国MinnesotaMining andManufacturing 公司合作开发的3M 结构型胶来实现压铸铝减震器支座与高强度钢前纵梁异种材料之间的连接。
在国内,在目前的白车身生产制造中,大都是采用冲压工艺实现的。由于冲压工艺一般要求零件在冲压方向下不能存在负角, 因此能生产出来的零件的复杂程度就受到了限制, 以至于很多时候本应是一体的构件不得不拆开成两个或者更多的零部件,这就增加了后续装配的工作量, 而且整车的性能也会受到一定的影响。同时,为保证冲压成形性,一般采用低碳钢材料进行生产, 难以实现轻量化和节能减排的目的。
现今虽然一汽铸造研究中心在汽车零部件的应用上已在尝试采用AZ91D 镁合金材料研发TAL发动机罩盖以实现车身轻量化。但诸如采用铝合金等轻质材料进行压铸生产的薄壁零部件, 目前在国内的中低端乘用车中还是罕闻寡见的。为此很有必要探讨如何基于压铸工艺生产出轻质的零部件,以简化车身装配工艺,同时实现轻量化。
众所周知, 压铸工艺一个明显的优点就是可以生产出很复杂的零件, 这是传统的冲压工艺所不能比拟的。基于此,本文将以某公司一款轿车的减震器支座为例,采用铝合金材料,并利用procast 2013 对减震器支座进行模型分析及结构优化, 为后续的生产和应用提供指导。
1 减震器支座模型工艺分析及仿真参数设置
如图3 所示, 传统冲压生产的减震器支座有A和B 两个零件通过焊接组成。为了从材料上减轻车身重量, 同时简化装配工艺, 拟将减震器支座一体化, 并采用高压铸造工艺实现铝合金铸件的生产。
结合压铸工艺特点重新构建的一体化减震器支座三维模型如图4 所示。
考虑到压铸件与冲压件的不同, 一体化后的减震器支座的厚度适当增加到2.5mm。依据减震器支座的特征,参考铸造手册可选用曲面分型面,浇注系统确定为中心浇口的结构形式, 在金属液最后填充区域和交汇区域布置溢流槽,共设置为6 个,并利用三维建模软件对减震器支座进行铸造系统的建模,如图5 所示。
在Procast2013 中对三维模型进行四面体网格划分, 如图6 所示。减震器支座的材料采用AlSi11Cu2Fe 铝合金, 模具材料选择热作模具钢H13,其化学成分分别如表1、2 所示。
根据生产经验, 设置的工艺参数为: 浇注温度610℃,内浇口速度40 m/s,重力加速度为9.8 m/s2,模具初始温度为180℃。
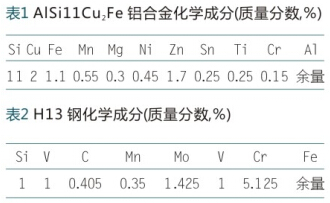
#p#分页标题#e#
2 充型过程分析及优化
充型作为整个高压铸造过程极其重要的一个环节,是后续凝固过程分析的基础。在充型过程,往往会随着合金液强烈、不规则的紊态流动,型腔中的空气来不及排出而被卷入合金液内, 从而导致卷气现象的发生。而铸件中卷气的严重程度对铸件质量有着重要的影响, 因此很有必要对充型过程合金熔液的流动状态进行分析, 并力求通过结构和工艺参数的优化来获得合理的流动状态。
减震器支座初步浇注方案的充型过程中的卷气情况如图7 所示。
由图7(a)、(b)可知,直浇道尺寸不合理,合金熔液触到模具后回流,导致该区域空气滞留;过大的浇注系统还会产生过多的废料,导致材料成本增高。由图7(c)、7(d)可看出,合金液充填过程基本平稳,6 个溢流槽几乎都是最后才充型完成, 有利于型腔中气体的排出和氧化夹渣的容纳, 避免缺陷出现在铸件本体上。但从图7(e)来看,图示A 区域由于被左右两股金属液包围, 气体无法排出而产生比较严重的卷气现象,如图7(f)所示。
针对初步浇注方案浇道尺寸过大以及溢流槽不合理的问题,对浇注系统和溢流系统进行结构优化,即根据金属液流动的形态减小压室尺寸, 然后在减震器的A 区域增加一个溢流槽,如图8 所示。保持相关工艺参数不变,重新进行仿真模拟。最后铸件充型完毕后减震器支座上几乎没有卷气缺陷的存在, 这说明结构的优化对铸造缺陷的
解决可以起到相当重要的作用。
3 总结
(1) 通过对铸件压铸过程的仿真模拟, 可以在设计前期及时发现存在的问题, 有利于针对性地进行结构上的优化。仿真实验表明,合理的浇注系统,有利于铝合金熔液的平稳流动,减少卷气现象发生,同时避免材料的过多浪费。同样,正确的溢流槽位置和数量, 可以有效地容纳铝合金液在充型过程中因卷气而产生的氧化夹渣等杂质。
(2) 通过对车身零件进行组合重构,采用铝合金等轻质材料,运用压铸等先进工艺进行零部件的开发生产是一种实现汽车轻量化的切实可行的途径。