文:黄奇德 德宝压铸技术公司
在汽车轻量化的发展趋势下,铝合金的应用受到了重视。当中使用压铸工艺的零件,形状越益复杂、质量要求越来越高。本文介绍奥地利美腾公司的新型AVD铝液给汤技术,如何应对此一新的挑战。
压铸结构件对熔炉和给汤机的要求
目前用在汽车车体结构的压铸件,有减震塔,AB柱,发动机托架,横梁,车门内板等。这些部件都是面积较大和壁厚很薄(2-3毫米),同时又要和其他不同零件结合,形状也很复杂(这些零件以前是焊接在一起的冲压件)。由于这些铸件很多都要经过安全撞击测试,或需要铆接,因此要很高的机械延展性能。有些铸件要焊接或热处理的,更会令铸件内含的微小气孔膨胀和起泡。以上的种种因素,都对整个压铸工艺流程(从适当的熔炼,铝液的处理和运转,优化稳定的压铸参数控制,特别是在整个充型过程中的高真空度保证),提出很高的要求。虽然生产压铸结构件比传统的压铸生产成本高很多,但相比原设计的多冲压件的组合,也可以透过汽车的设计优化、整体减重、和综合成本的降低,来达到生产的合理化。
此外,随着压铸机性能的提升和新工艺(如挤压/流变铸造)的开发,更多的零件如悬挂件,车底盘等都能用实时控制压铸机实现。生产这些零件都依赖非常稳定而准确的压射参数控制,其中包括给汤量。
大部分的压铸件都是用铝硅合金。如果是用于非结构性应用,使用的大都是二次回收的铝合金。但对于安全性的关键零部件和结构件,为了保证合金的纯度和低含铁量,就只能用初级铝来冶炼了。常用的结构件合金如AlSi10MgMn,由于是大面积薄壁件,浇注温度要提高来保证流动性。如果是流动性差的AlMg5Si2Mn,那炉温就更高。提高的炉温对吸氢率和个别合金成分的烧损率有负面影响。这些生产条件都对现有的给汤和保温提出了更苛刻的要求。
常见的给汤方式
目前压铸市场上主流的给汤技术有两大类,一种是用汤勺给汤,一种是气压给汤。
给汤方式是把汤勺装在机械臂上,汤勺伸进铝液中取汤。汤勺的倾斜角度可以调节,控制取汤量。机械臂把载了铝液的汤勺移动至压室进料口,倒入铝液。这种模拟人手舀汤的方式,操作容易,设备成本低,很适合一般压铸生产的要求。汤勺机械臂又分摇臂和横梁结构,摇臂式速度高,适合10公斤以下的给汤量;横梁式载重大,适合较大的给汤量。汤勺的材料有铸铁、钢包和陶瓷等。铁基汤勺重、惯性大,需要经常涂上防粘铝和隔热涂料,而且容易腐蚀;好处是价格便宜。陶瓷汤勺轻,不粘铝、保温性好,而且使用寿命长,容易清理,可烧结出复杂的形状。
气压给汤装置和保温炉是一体化的。虽然有不同的设计,原理基本是一样。是在密封环境下在炉膛或铸造室加气压,使铝液透过升液管流出,通过触动出汤口的探头计算加压的时间,从而控制给汤量。由于是封闭的炉膛,这种方式的优点时耗电小,减少和空气接触的氧化合吸氢;而且液面下取汤不含表面氧化膜,出汤量大而快。
奥地利的美腾工业炉公司在2010年开始对压铸的给汤技术做市场调研,发觉大部分用户对当前的技术有以下的意见:
-给汤精度不足,导致产品质量不稳定。
-铝液内有氧化皮,对铸件的机械强度有负面的影响。
-铝液温度控制差,同样影响铸件的机械强度。
-炉膛铝液过热,降低铝合金质量。
-压室的填充过程产生紊流,铸件质量不好。
针对上述意见,美腾公司开发了新的AVD铝压铸给汤系统,并在2011年德国的GIFA铸造展介绍这项新技术。首部设备于2012年初在欧洲开始了生产测试。现在让我们介绍一下新技术的工作原理。
工作原理
新设计是结合了汤勺舀汤的方便性,和气压给汤的优点,进一步提升给汤技术的高度。
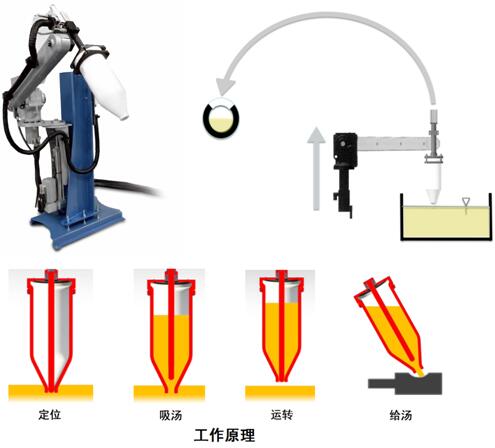
#p#分页标题#e#
特点是用了特殊的高强度密封陶瓷容器取代了传统汤勺。容器的底部时开敞的,利用摇臂把容器徐徐降下寻找液面,直至伸入铝液。进入后打开容器内的柱塞棒,开启负压把铝液吸进容器。容器上端有一称重模块,测量进入容器的铝水量,当达到预设的重量后,柱塞棒把开敞口堵上。摇臂把装有铝水的容器运转至压室进料口,再次打容器开底部把铝水放进压室。新技术期望了几个优点:
-铝水在液面下吸进,减少带入表面的氧化膜。
-铝液从炉膛运到压室过程中,封闭的容器在负压下不会进一步氧化。
-封闭的陶瓷容器可以保温,运转中减少温度降。
-一体化的测重器,提高给汤精度。
- 提高能源效益。
产品推出后受到热烈的反响,从开始推广至今,已卖出约200套。
综合过去4年的客户反应,他们对真空给汤技术有以下评价:
客户反映的优点
第一是给汤精度。在以上的实际生产数据中,可以看到1.84公斤 的给汤量,达到的标准偏差是+/-8.2克,即0.45%,直径70mm料饼厚度实际偏差+/-0.8mm。应是当前给汤技术中精度最高的。其它的案例,好像是给汤量只有380克,标准偏差是+/-6.6克,即1.73%;直径40mm,料饼厚度实际偏差+/-1.96mm。另一给汤量990克的,标准偏差是+/-6.4克,即0.65%;直径70mm料饼厚度实际偏差+/-0.62mm。如果给汤量越大,标准偏差百分比越低。如文章前段所述,汽车结构件生产需要很高的压射参数稳定性,给汤量对实时控制压铸有关键的影响。
给汤量变化导致工艺不稳定
第二是铝液的温度控制。铝液从炉膛到压室的运输过程中,会透过容器的热传导和空气的热对流损失热量。和其它给汤系统比较,陶瓷容器的热传导系数远远低于铸铁和钢包,同时整个过程是密封的,热对流损失至低。
第三是铝液质量的提高。在2.5公斤的陶瓷容器测试中,10秒钟的铝液温度降是13C,比钢包低很多。钢包的温度降超过20C。因此,炉膛内的铝液温度就可以相应降低。这不单只节省能源,对于合金的烧损率也有减少。更重要的,铝液在温度较低时吸氢率较低,而对那些成分要求严格,特别是含镁、铍的铝合金,温度太高会烧损得快些,影响铸件机械强度。由于在液面下吸铝,吸入的铝水不含液面的氧化膜。同时相对于气压炉和汤勺在加压、出汤、运动过程中的不断氧化,陶瓷容器在运转时没有空气进入氧化,对铸件的质量有很大的提升。
第四是能源效益。壹客户使用1.2吨的AVDF真空给汤保温炉,和之前相比,炉温降低了35C,这等于每100公斤铝水可以节省0.875kW,而每小时输出量600公斤,再加上炉膛保温性能好节省了0.5kW的热损失,共节省5.75kWh。等于每年节省了~40000kW。
能源效益还包括料饼回收的减少。稳定的料饼厚度可以降低给汤量的设定,从而减少料饼回收率。以10公斤的给汤量来计算,其它给汤系统只能达到+/-2%,即200克。真空给汤能达到<0.5%即50克。以90mm直径计算,一年减少了65吨铝的回收(生产周期60秒,300工作天),不单省了20000kWh电量(重熔电耗0.3kWh/kg),更能降低铝合金周转的数量;特别是较贵的高纯度铝合金,大大降低资金压力。用户也告诉我们说低氧化杂渣含量的回炉料,使烧损率比以前减少了。
第五是简单的使用和保养。真空给汤系统使用的保温炉和普遍使用的保温炉差别不大。AVDF炉膛清理非常简单,清理空间大而且结构简单,维护工作快而方便。清理时不影响生产。加料也只在正常高度操作,没有安全隐患。对炉体的密封性也没有要求,更换零部件时无需考虑整体密封性。#p#分页标题#e#
陶瓷容器使用高强度的钛酸铝,除了隔热性能好、材质轻外,热膨胀系数低也能减少铝水的热冲击。良好的抗蚀性对铝水的侵蚀使寿命得到保障,一般寿命能达都10万至20万次,而且无需像铁浇包那样每天涂覆盖剂。要做到生产的密封效果,容器只需两片密封圈。又能透过系统的软件检测密封圈是否漏气,更换也非常方便。对于习惯用保温炉+汤勺给汤的操作维修工,很快就能适应。同时,容易使用的先进触膜屏图形操作界面,车间操作工也能迅速掌握。
灵活的配置
给汤系统的结构简单灵活,除了是独立的给汤机外,也有一体化保温炉,适合中央熔化的大量生产模式;还有用于小量生产的一体式熔化保温坩埚炉。如需要复杂给汤动作的可以用机器人。给汤机的陶瓷容器有不同的容量,从1公斤至20公斤。遇上2000吨以上压铸机,给汤量>20公斤的,则选用横梁式传输结构。
一体化真空给汤保温炉 一体化真空给汤坩埚炉
横梁式给汤 机器人给汤
总结
美腾公司的AVD真空给汤系统是新一代用于压铸生产的铝液给汤系统,已经在全球注册了设计专利。新产品正好符合现代化高标准的汽车压铸工艺,和低能耗环保生产的要求。更重要的是产品先进的同时,使用也非常简易。目前已在欧美各地的先进压铸企业广泛使用。如需进一步了解,请和我司联系。