文: 沈阳航空航天大学 杨 兵
摘 要:对某汽车发动机压铸铝合金缸体原有工艺及试漏过程中油路渗漏,导致废品率增加的问题进行分析,找出产生问题的主要因素,并对其进行合理优化改进。 改进后的工艺有效地降低了油路渗漏导致缸体废品率增加的几率,工艺改进取得满意成效。
关键词:压铸缸体;气孔缺陷;工艺改进;品质提升
随着社会的发展,人们的环境保护意识得到了增强,因此,汽车轻量化理念则随着时代的发展应运而生。 压铸铝合金缸体由于具备质量较轻、耐腐蚀性良好等优良性能,逐步成为了汽车工业发展的趋势。
图 1 为某汽车发动机压铸铝合金缸体示意图,其材料为 ADC12,轮廓尺寸为 367 mm×190 mm×263 mm,最小壁厚为 3 mm,铸件净重 13.2 kg,硬度90~110 HB (Z105), 铝合金缸体结构包括缸筒、水套 、高 压 油 道 、曲 轴 箱 、主 轴 承 座 等 ,油 路 要 求 在0.3 MPa 下打压 26 s 内允许泄漏量为≤2 m L/min。生产工艺路线:合金熔炼→压铸→清理→粗加工→浸润处理→一次打压试漏→精加工→二次打压试漏→检验。
该发动机缸体在打压试漏过程中出现不同程度的油路渗漏现象,此类油路渗漏现象的产生严重影响了发动机缸体的品质,使发动机缸体的废品率增加。 因此,对发动机压铸铝合金缸体原有工艺及试漏过程中油路渗漏问题进行分析, 找出产生问题主要因素, 并加以优化改进, 是提高发动机缸体品质,降低废品率的关键。
1 原生产工艺及原因分析
1.1 原生产工艺
(1) 铝合金熔炼工艺及压铸设备 铝合金熔炼采用高效燃气熔铝炉 STM-500, 除气机 型 号 为FDU-Great, 精炼介质选用氮气 , 精炼温度范围:700~720 ℃,精炼时间:(10±2)min,气体流量为 5~20 L/min。 精炼后,铝液进行静止、打渣,静止时间为20~30 min。
静止后的铝液转入压铸定量炉(W1700SPro Dos)内 , 待浇注使用。 压铸设备使用型号为IP2150SC。
(2)压铸 模及浇注系统设计 模具采用六面抽芯结构,主要由定模部分、动模部分、
成型部分、浇注系统、抽芯机构、顶出机构、排气系统、加热保温及冷却装置、定位导向系统等组成。 模具型腔部位的材料为 DIEVAR,模框材料为 S50C(锻钢),铸销材质选用 SKD61,
氮化硬度为 900~1 100 HV,使用寿命约 1 万模次以上。由于铸机结构限制且缸体缸套为嵌入式,通过对浇注过程的模拟分析,本缸体采用单侧浇注(如图 2)。
(3)压铸工艺参数
① 铝液温度的选择 : 由于车间使用定量炉与压室连接部位非完全封闭,因此选用浇注温度为(680±5)℃,能够确保铝液顺畅填充整个模腔; ②压铸速度的选择: 在保证填充顺畅的前提下,有效提高浇注速度能够减少内部气孔的产生。 但高速速度的提升,可使模具寿命严重降低,因此,利用数据模拟的方式,验证各个速度区间对产品品质的影响(图3),选出合适速度区间。
最终选定 , 低速速度 0.19-0.21 m/s, 高速速度为4.90~5.10 m/s;③ 模具 温度范围 : 由于模具整体型腔较大,因此各部位温度差异较大。 温度过高,
导致模具产生扒铝现象, 并对产品内部气孔的产生及各部位的缩松有严重的影响。因此,在模具较厚部位及易产生内部气孔部位添加点冷却或强冷装置, 确保模具整体温度平衡。
缸筒部位温度范围 120~150 ℃, 采用螺旋式水冷结构,有效对缸筒部位进行降温;易产生气孔部位温度范围 110~130 ℃,减少内部缩松的产生;其余部位温度范围约为 160~180 ℃。
高压水冷装置, 利用1.5 MPa 的高压冷却水对预铸销部位进行快速的降温冷却,确保该部位组织细密,减少疏松的产生,并能够有效提高预铸销的使用寿命。 图 4 为点冷却装置结构示意图。
#p#分页标题#e#
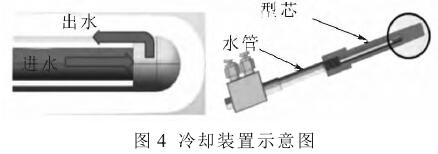
1.2 发动机缸体油路渗漏原因分析
对渗漏报废的发动机缸体进行解剖外观检查。通过图 5 外观检查发现发动机缸体油路孔与螺纹孔之间存在压铸缺陷,是导致发动机缸体漏油的原因。而该压铸缺陷呈现的主要形态为不规则形状孔洞,且气孔内壁较为粗糙,并掺杂少量规则圆形,内壁光滑的小孔洞。 根据气孔缺陷呈现形态及发动机缸体漏油位置结构分析,发动机缸体该位置壁厚差过大,导致
壁厚中心的铝液最后凝固, 是产生这类气孔缺陷的主要原因, 而这类壁厚处的气孔缺陷多是收缩气孔及析出气孔的混合体,不是一般措施能够防止的。
2 工艺改进
2.1 运用在模具设计上增加预铸销的方法 ,改变铝液的最后凝固位置
改进模具设计,图6 为发动机缸体模具改进后示意图,新设计的模具通过增加预铸销的办法,改变发动机缸体最后凝固位置及该位置的冷却速度,减小因渗漏位置壁厚差过大导致产生此类气孔缺陷的几率。
2.2 压铸过程增设抽真空工序 ,降低气孔缺陷产生几率
在压铸过程中,增设抽真空工序,在模具上添加真空阀系统,利用真空泵,促使模具型腔内部形成真空状态,减少压射过程的卷气及型腔内部残留涂料蒸发后气体的混入,从而降低气孔的产生。 真空阀设计部位为远离浇口方向、 排气通道最末端,取代原排气板设计,
具体位置如图 7 所示。
2.3 降低浇注温度,优化工艺参数
因为在一定温度范围内,浇注温度越低,产生收缩气孔缺陷的倾向性越低,所以在保证发动机缸体品质的前提下,将浇注温度由(680±5)℃降低到(665±5)℃,从而降低发动机缸体整体气孔缺陷产生的几率。
通过以上工艺改进,发动机缸体渗漏位置的气孔缺陷得到了明显的改善如图 8, 产品品质得到了大幅度提升。 原该部位渗漏数量占投产数的比例约为 3%,经过工艺改
进之后,该部位渗漏数量占投产数的比例小于 1%。
3 结语
经过对发动机缸体原压铸工艺进行改进后,发动机缸体在满足其他技术要求的同时,
因为油路渗漏问题导致发动机缸体产生废品的几率明显降低,发动机缸体品质得到了大幅度提升。 连续生产 200件,产生油路渗漏废品 3 件,改善部位废品为 0 件。从公司成本、产品品质等方面考虑,取得了令人满意的效果。