文:吉泽升 孙海波 赵 密
哈尔滨理工大学 材料科学与工程学院
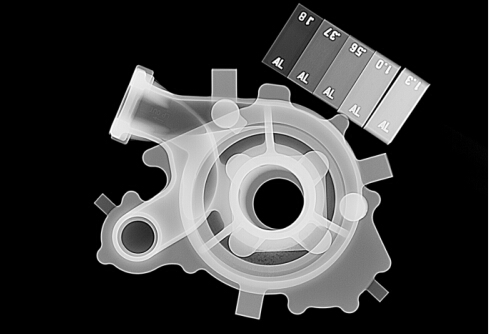
摘 要:针对快速准确检测铝合金压铸零件内部质量的问题,采用 X 射线实时成像系统对铝合金压铸件凸轮轴盖进行内部质量检测试验. 依据 X 射线实时成像的工作原理,利用图像呈现的灰度对零件内部缺陷进行评价. 采用线切割方法获取零件内部缺陷截面,验证图像缺陷和实际缺陷的对应关系. 通过试验发现不同类型的实际缺陷对应实时成像图像不同的缺陷形貌. 缩松在影像中呈羽毛状或海绵状,缩孔在影像中呈树枝状较大的影像,气孔在影像中呈现清晰的圆形或椭圆形轮廓. X 射线实时成像探伤能够准确反映铝合金压铸件内部缺陷特征,精确控制产品质量.
关键词: X射线实时成像; 凸轮轴盖; 铝合金压铸件; 内部缺陷
0 引 言
传统的射线检测是基于胶片成像的,但是胶片成像存在着很多缺点,如不能满足实时成像,成本过高,图像管理不便等,随着电子技术的飞速发展和无损检测技术的发展,特别是计算机信息技术应用的普及,20 世纪 80 年代新兴的一种无损检测技术——X 射线实时成像检测技术应运而生。 X射线实时成像技术改进了照相探伤方法的不足,可以直观地看到投影图像,显示缺陷的大小和形状,从而判断缺陷的性质,射线实时成像技术无论在检测效率、经济效益、表现力、远程传送、方便实用等方面都比照相底片更胜一筹,在无损检测领域中有良好的应用前景。 由于计算机图像处理技术的发展和微小焦点 X 射线机的出现,X 射线实时探伤机已能够用于金属材料的无损检测。 铝合金压铸件在生产过程中易产生孔洞类缺陷,影响压铸件的整体强度及气密性. 目前,压铸件内部质量越来越受到重视,为生产出内部质量好的铝合金压铸件,经常要求对产品进行全数探伤检验。
1 X 射线实时成像探伤原理
X 射线实时成像探伤原理可用两个“转换”来概述: 射线发生器中加速的电子撞击阳极靶产生 X射线,X 射线穿透金属材料后被图像增强器所接收,图像增强器把不可见的 X 射线检测信号转换为光学图像,称为“光电转换”; 用高清晰度电视摄像机摄取光学图像,输入计算机进行 A/D 转换,转换为数字图像,经计算机处理后,还原在显示器屏幕上显示出材料内部的缺陷性质、大小、位置等信息,再根据图像的灰度对检测结果进行缺陷等级评定,从而达到检测的目的,
当强度均匀的 X 射线束 I0透照试件时,由于 X射线穿透不同密度的工件时会有不同的衰减效果,我们可以借助衰减的程度不同判断缺陷的位置和大小. 由于现实中缺陷体积远小于工件体积,我们可以假设 T≤L 来分析 X 射线检测基本原理,如图 1所示.
依据宽束射线衰减规律可知:
式中

为缺陷处透射的一次射线强度;

为无缺陷处透射的一次射线强度;

为缺陷处透射的散射线强度;

为无缺陷处透射的散射线强度;

为缺陷处透射射线强度;

为无缺陷处透射射线强度.由于

,因此可以认为
所以缺陷处与无缺陷处的能量差为
这就是实时成像探伤产生物体相对对比度的射线检测的基本原理。
2 试验仪器与试验方法
选用两个 ADC12 为原材料生产的凸轮轴右后盖进行 X 射线探伤试验,零件示意图如图 2 所示,零件实物图如图 3 所示.
探伤时使用的实时成像探伤机为丹东奥龙射线责任有限公司生产的 XYD - 1504 型实时成像系统探伤机. 试件在探伤的过程中,工艺参数的选择对探伤影像的影响十分重要,本实验所使用的 X 射线实时成像检测仪所涉及到的参数见表 1。
把需要进行探伤的工件放入 X 射线实时成像探伤机中,调整好工件的位置,使需要投射的部位与阳极靶面相平行,零件摆放方式如图 3 所示. X 射线控制器控制高压发生器产生高压,由 X 射线管发射的 X射线透照测试工件,透照后射线发生衰减,透照后的X 射线被图像增强器接收,在监控器上形成含有工件结构、状态及内部缺陷分布、大小等信息的图像。
设定好参数值,然后开高压开始进行射线透照。把工件需检验的部分调整好电压使射线能把工件完全穿透,获得比较清晰的缺陷影像,投射后得到的影像图片拍摄下来保存。 使用电子尺对缺陷尺寸进行测量。
将工件存在缺陷的区域标定好,在线切割机上把零件按照射线透照的位置放平,每 2mm 的厚度切割一次,将零件进行分解,直到得到最大的缺陷尺寸为止.
3 试验结果及分析
探伤检验结果如图 4 所示,图中两张图片分别是 1#零件和 2#零件两个零件的探伤照
1#零件探伤检验结果为: 在 A 处存在 V 形缺陷,缺陷尺寸约为 6 mm × 3 mm,B 处存在不规则形状的缺陷,缺陷尺寸约为 2 mm × 3 mm,C 处存在 2处缺陷,缺陷尺寸分别约为 1. 5 mm ×2 mm、3 mm ×2 mm,D 处存在直径为 1 mm 左右的圆形缺陷。
2#零件探伤检验结果为: 在 A 处存在尺寸约为5 mm × 6 mm的缺陷,B 处存在约为 3 mm×4 mm 的缺陷,C 处存在零散分布的缺陷,D 处存在2 处缺陷,缺陷尺寸分别约为3 mm ×3 mm、2 mm ×1. 5 mm。
对 1#零件进行线切割,切割图如图 5 所示,对探伤照片及线切割照片中的缺陷部位进行局部放大,局部放大图如图 6 所示,通过线切割在切割面可以观察到在剖切面可观察到 a、b、c 三处缺陷为缩孔,d 处缺陷为气孔,缺陷的尺寸与探伤结果中的缺陷尺寸相同。
对 2#零件进行线切割,切割图如图 7 所示,对探伤照片及线切割照片中的缺陷部位进行局部放大,局部放大图如图 8 所示. 通过线切割在切割面可观察到 a、b、d 三处缺陷为缩孔,c 处缺陷为缩松,缺陷的尺寸与探伤结果中的缺陷尺寸相同。