文:文 韬
重庆隆鑫压铸有限公司
摘 要:压铸功能工艺是把压铸合金、压铸模和压铸机这三个生产要素有机组合和运用的过程。压力铸造工艺的诸多特点,使其在提高有色金属合金铸件的精度水平、生产效率、表面质量的那个方面显示出了巨大优势。而盖类产品就是表面质量要求相对较高的产品一种,本文就针对压铸铝合金盖类产品表面气泡问题做出一些简要的分析。
关键词:压铸铝合金盖;气泡;工艺
1 概述
铝的导热性好,是制作热交换器、制冷设备、散热器的好材料。铝在低温环境中仍然保持良好的强度和机械性能有时甚至有所提高,因此它是低温防寒的好材料。此外铝还具有吸声性、耐蚀性,而且铝是轻量化的首选材料。所以铝在各行各业中都发挥着不可忽视的作用。铸造铝合金在摩托车、汽车上主要用于发动机、传动机构、转向机构、制动器、行走系及各种附件。在工业发达的国家,摩托车、汽车用铝铸件占到各类铝铸件的大半。例如日本,铝铸件的 76%,压铸件的77%为摩托车、汽车铸件。机械制造业广泛用铝和铝合金制造车轮、滑轮、通风机、起重机及泵的零部件,活塞和发动机等。这是因为铝及其合金不但密度轻,而且能达到要求的强度,从而能降低在运转中的能量消耗或者在使用相同能量的条件下大大地提高运转速度,同时也能延长机件的使用寿命。
铝合金压铸件表面经常出现大小不一的气泡,尤其是在壁薄的盖类产品上,其中的原因是什么呢?又该如何来预防和解决,下面就来进行简要的分析。
压铸件表面的气泡经常出现在产品的离内浇口较远的一端,有时铸件热处理后面上也有气泡,有的气泡锯开后里面有黑色杂质,有的为气体。
气泡的特征是:铸件表面有米粒大小的隆起,表皮下形成空洞,经过抛丸或喷砂处理后将会出现疏松或凹陷。如图 1 所示:
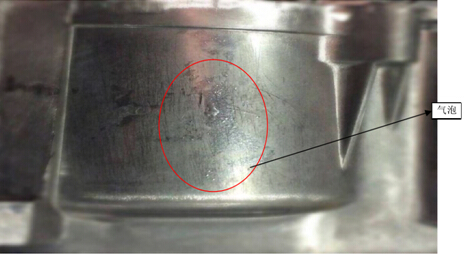
图 1 气泡
2 产品缺陷原因分析
为了解决产品缺陷,我进行了如下分析:
2.1 人的因素
① 脱模剂是否喷得太多,因脱模剂发气量大,用量过多时,浇注前未燃尽,使挥发气体被包在铸件表层,所以在同一条件下,某些工人操作时会产生较多的气孔的原因之一,选用发气量小的脱模剂,用量薄而均匀,燃净后合模;②未经常清理溢流槽和排气道;③开模是否过早;④是否对模具进行了预热,各部位是否慢慢均匀升温,使型腔和型芯表面温度为 180℃~260℃;⑤如果无预热装置时是否使用铝合金料慢速推入型腔预热或用其它方法加热;⑥是否取干净的铝液,有无将氧化层注入压室;⑦金属液一倒入压室,是否即进行压射,温度有无降低了;⑧冷却与开模,是否根据不同的产品选择开模时间;⑨操作员有无严格遵守压铸工艺;⑩有无采用定量浇注,如何确定浇注量。
2.2 机(设备、模具、工装)的因素
主要是压铸模具方面的因素:①浇口位置的选择和导流形状是否不当,导致金属液进入型腔产生正面撞击和产生旋涡(降低压射速度,避免涡流包气);②浇道形状有无设计不良;③内浇口速度有无太高,产生湍流;④排气是否不畅;⑤冲头润滑剂是否太多,或被烧焦,这也是产生气体的来源之一;⑥排气道位置不对,造成排气条件不良;⑦溢气道面积是否够大,是否被阻塞,位置是否位于最后充填的地方,模具排气部位是否经常清理,避免因脱模剂堵塞而失去排气作用;⑧模温是否太低;⑨有无因压铸设计不合理,形成有难以排气的部位;⑩溢流口截面积总和有无小于内浇口截面积总和的 60%,排渣效果差。
2.3 方法的因素
主要指压铸参数、操作工艺:① 有无根据不同的产品选择工艺参数(铸铝液温度 630-670ºC),合理选择压铸工艺参数,特别是压射速度,调整高速切换起点;②有无减少脱模剂含水量,有无采用发气量小的脱模剂;③合金熔炼温度是否过高;④铝液温度如何测定,温度计准确与否;⑤有无根据产品及时调整压射速度和慢压射速度快压射速度的转换点;⑥有无大机器压铸小零件,压室的充满度过小。经过生产实践及总结认为气泡形成的原因大致有如下几类原因:① 金属液在压室充满度过低,易产生卷气,慢压射速度过高;②模具排气不良;③熔液未除气,熔炼温度过高;④模温过高,金属凝固时间不够、强度不够而过早开模顶出铸件,受压气体膨胀起来;⑤脱模剂、冲头油用量过多;⑥内浇道开设不良,充填方向交接,形成涡流,导致卷气;⑦喷涂后吹气时间过短,模具表面水未吹干。
3 解决产生气泡的方案
基于以上原因,可以通过:①改小压室直径,提高金属液充满度;②延长压射时间,降低第一阶段压射速度,改变低速与高速压射切换点;③降低模温,保持热平衡;④增设排气槽、溢流槽,充分排气,及时清除排气槽上的油污、废料;⑤调整熔炼工艺,进行除气处理;⑥留模时间适当延长;⑦减少脱模剂用量,来进行消除。
4 结束语
对于压铸产品,从生产准备到批量生产,牵涉的环节很多,影响因素也很多,包括材质、模具、设备状况,生产工艺等各方面;任一环节出了问题,就不能生产出合格的压铸件。上述问题,都是在生产实际过程中要涉及的,希望能对实际生产有一定帮助,最终目的是生产出合格压铸件,满足企业实际生产的需求。