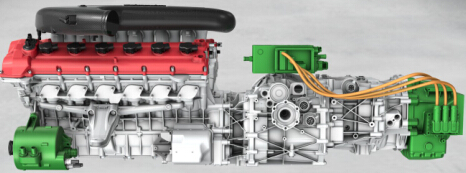
文:布 仁
摘 要:基于压铸成形技术,研制出汽车发动机下缸体压铸件。 针对铝合金下缸体压铸件存在的内部缩松、气孔缺陷等问题,提出了相应的解决措施,并给出了优化方案。 最终获得质量轻且内部组织致密的下缸体铝合金压铸件。
关键词:压铸成形 ;下缸体; 铝合金
目前,采用压铸成形技术来生产铝合金铸件已成为行业趋势。 传统的铸铁缸体生产成本低、刚性好、耐热性好、生产工艺简单;然而其质量较大,与汽车轻量化设计理念不相符。
为减轻汽车发动机质量,同时保留铸铁缸体性能优势;现将发动机缸体上部缸套部分与下部曲轴部分分离制造。 上部缸套仍采用铸铁制造,下部曲轴部分则采用铝合金制造。 分离出来的曲轴部分称为发动机下缸体。 发动机下缸体各部分壁厚差异较大,压铸成形难度高。 本课题基于压铸成形技术,成功将其用于制备汽车发动机下缸体;并获得了质量轻且内部组织致密的产品。
1 下缸体结构及其压铸难点
图 1 为汽车发动机下缸体铝合金铸件。 该铸件外部轮廓大小为 384 mm×256 mm×68 mm, 质量大小为 8.4 kg,平均壁厚大小为 7.2 mm;其压铸质量大小为 11.3 kg, 材料为 A380。 因下缸体与曲轴直连,于是需将 5 个铸铁轴承座(镶嵌件)布置于下缸体底部。
结合图 1 中发动机铝合金下缸体结构,发现其压铸难点在于:①铸件壁厚极不均匀,最大厚度为25 mm,最小厚度仅为 2 mm,压铸时极易形成缺陷;②下缸体底部需布置 5 个铸铁轴承座, 其要求定位精确且不能与铝合金分离; ③铸铁镶嵌件布置处两侧壁厚最大为 7 mm,最小仅为 2 mm。 这不利于合金液的平稳充型与凝固补缩; ④铸件形状不规则处较多,容易出现缩松、缩孔、裂纹和气孔等缺陷。
2 铝合金下缸体压铸成形技术
发动机铝合金下缸体压铸成形技术要点如下:(1) 设计合理的浇注系统。 如图 1 可知下缸体上下两端壁厚较大,中间镶嵌件布置部位壁厚较小,故选用单侧浇注系统。
(2) 采用真空压铸技术,选用齿形激冷排气块。真空机配合齿形激冷排气块, 既可解决排气集渣问题, 又可消除因镶嵌件两侧壁厚过小而降低合金液流动性问题。
(3) 预热铸铁镶嵌件。对铸铁镶嵌件的预热,可提高镶嵌件与合金液的润湿程度; 确保铸铁镶嵌件与铝合金在铸件成形后不发生分离。此外,镶嵌件的预热还可提高其附近合金液的流动性。
试验发现,当压铸主要工艺参数如表 1 时,所获得的铝合金下缸体具有致密的内部组织、 成品外形美观。各参数对下缸体品质的具体影响如下:预热镶嵌件至 125~145 ℃,可大幅改善下缸体溢流槽一侧的品质; 控制铝合金液温度处于 645℃~660℃区间, 控制模具喷涂后温度处于 170~210 ℃区间,可使压铸件品质稳定,避免出现铸造缺陷;当慢压射速度约 0.23 m/s,快压射速度约 4.1 m/s,压力 75 MPa时,可获得品质较好的压铸件。 此外,为了获得品质良好的压铸缸体;须保证铝合金液品质,对铝合金液精炼除气。
3 铸件缺陷与消除
3.1 铸件缺陷位置与特征
以上述工艺压铸所得下缸体铸件, 外观成形良好。 进一步采用 X 射线对铸件品质进行检测。 X 射线检测结果如图 2、3。图 2 所示两处位置为铸件缺陷最为严重的部位,这两部位的缺陷主要为缩松和缩孔。其对应的 X光图如图 3(a)和(b),可清晰地看见缩松和缩孔缺陷(图中圆圈内)。
3.2 消除缺陷的措施
针对上述铸件缺陷,结合下缸体结构特点,经过反复试验,现得到以下措施。
3.2.1 溢流槽结构优化
溢流槽在铝合金下缸体压铸过程中意义重大,其作用为:调节模具温度、型腔排气、存储冷污金属液和转移缺陷部位等。 因此改进溢流槽结构有助于提升铸件品质。
图 4(a、b)分别为溢流槽改进前后的照片。 图 4(a)中 a 处设有 1#、2#、3#和 4#溢流槽。 1#和 3#溢流槽共用一个排气槽,2#和 4#溢流槽共用另一个排气槽。合金液充型时,合金液先填充 2#和 4#溢流槽,通过溢流槽后于排气槽汇合。 1#和 3#溢流槽在 2#和4#溢流槽之后得到填充,填充好的 2#和 4#溢流槽将1#和 3#溢流槽的排气道堵塞,这使得位置 a 处易形成气孔缺陷。 现将 2#和 4#溢流槽延长加大,同时改道至排气槽;保证两排气槽在合金液填充完 1#和 3#溢流槽后汇流。 试验发现铸件位置 b 处缩孔缺陷比较严重。由铸件结构可知,位置 b 处附近有较大型芯结构,易形成涡流裹气。 为此,需在 b 处布置一个溢流槽。为消除铸件中部缩松缺陷,将溢流口布置于铸件大平面上。 同时为防止溢流口的布置减小填充压力,选用竖形溢流口。 以上优化措施,有效消除了铸件内部缩孔和气孔缺陷,提升了铸件品质。
3.2.2 模具冷却系统优化
压铸时,局部温度过高易形成缩孔缺陷。 试验发现,在下缸体压铸过程中,其两侧壁厚偏大部位温度较高,达 285~325 ℃,易形成缩孔缺陷。 在最初的设计中,点冷却管直径 准12 mm;无法对铸件局部温度偏高部位进行有效冷却。 为提高这些部位的冷却效果, 现采用高压冷却设备和内径为 准4 mm的超细不锈钢点冷却管。 选择合适的高压冷却水参数,可降低型芯温度至 175 ℃左右,从而减少铸件内部缩孔缺陷。
4 结论
(1) 优化溢流槽位置、结构和容积,改善排气和集渣效果, 可消除压铸所得铝合金下缸体内部缩松和卷气缺陷。
(2) 采用超细冷却管对铸件进行局部冷却,合理设置冷却参数;可改善铸件厚壁部位的冷却效果,消除缩孔缺陷。