文:蒋岩 合肥工业大学
本文根据ADC12材质的汽车油泵支架压铸件形状特点, 选择铸件侧面中部作为分型面结合浇注系统的设计要求, 选择偏心侧浇道浇注系统; 根据所选压铸机, 计算了成型零件尺寸,并完成了成型及结构零件的设计; 考虑到铸件侧壁有通孔,且不深, 采用斜销侧抽芯机构: 最后进行了模具的总装和过程模拟。
关健词: 压铸: 油泵支架; 模具
1引言
作为一种高效率,高质量, 高自动化程度的铸造方法,压力铸造在工业生产中的地位越来越重要。压铸模具的成本高, 设计复杂, 工作环境恶劣, 其质量直接影响到产品的质量和成本, 可谓是压铸生产的重中之重, 随着CAD/ CAM软件的广泛使用, 压铸模具的设计水平得到了进一步的提升, 不但使得模具的开发成本大大降低, 也让其结构更为合理, 性能更加稳定。
2 铸件工艺分析
2. 1 铸件工程图
零件为奇瑞汽车用的油泵支架,材料 ADC12,铸造精度 CT6,铸件四个角上有凸台,分别有直径为 9mm、7mm、13.5mm 以及 5mm 的小孔,铸件平均厚度为7.7mm,其工程图如下所示。
图1 铸件工程图
2.2 确定分型面
按制件脱模方向, 选取最大外轮廓线, 作为模具的分型线, 该线所形成的面就是模具的分型面。
2.3 计算锁模力
锁模力是选用压铸机时首先要确定的参数。锁模力的作用主要是锁紧模具以形成模具型腔,抵抗压铸时高压液流产生的胀型力。
计算主胀型力

,式中

—胀型力,
;P—压射比压,取 50MPa
;A—铸件各部分在分型面上的总投影面积之和,一般加 30%作为浇注系统与溢流排气系统的面积,为44.85cm
2;计算得
=2242.5 KN。压铸时金属液充满型腔后产生的反压力,作用于侧向活动型芯的成形端面上,会使型芯后退,此时楔紧块斜面上产生法向力。由于侧向活动型芯成形面积相对较小,因而可不加计算。
计算锁模力锁F的公式为:

K —安全系数,一般取 K =1.25;
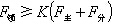
=1.25×2242.5=2803 KN为了防止金属液从模具分型面上喷溅和确保铸件的尺寸精度,压铸机的锁模力必须大于型腔填充时产生的胀型力。
3 浇注系统设计
3.1 内浇口设计
浇注系统三维图如图2所示,铸件尾部设置溢流槽,用于排渣排气,减少铸件内部缺陷。内浇口速度:铝合金铸件内浇口充填速度 Vg 的推荐值为 20~60m/s,选取为 20m/s;充填时间,经计算,压铸件的平均壁厚约为 7.7mm,利用充填时间计算公式 式中

充填时间,s; —快压射距离,cm; —压射速度选用值,cm/s。
图2 浇注系统3D图
快压射距离计算:

式中V—制件毛坯体积,cm
3;

—集渣包体积比例系数。d—浇口套内径,cm。可求出:

;内浇口截面积的确定:
式中
—内浇口截面积,cm2 ;
—通过内浇口的金属液质量,g;
—液态金属的密度,2.4g/cm
3 ;
—通过内浇口的金属液体积,约为 277cm
3;可求出:
。内浇口数量和位置的确定: 根据压铸件的形状尺寸、结构特征、壁厚、以及模具分型面的设置等各种因素的影响,采用三个分支浇口的形式。内浇口厚度、长度、宽度的确定: 由内浇口尺寸选择的经验数值表,选取此铝合金支架铸件三个内浇口厚度为 2.5mm,宽度分别为 10mm、10mm、20mm,长度为 2mm。
3.2 横浇道的设计
根据铸件及内浇口特点, 选用等宽横浇道, 截面为扁梯形, 见图3。
图3 横浇道工程图
横浇道截面的具体尺寸:
取
,因为横浇道分成三条,分别取
;取

;取

。
3.3 直浇道设计
压铸机选择宁波力劲400T卧式冷室压铸机,压室直径为60、选取60mm为浇口套内径, 其配合间隙选用正偏差60+0.03。
4 排溢系统设计
排溢系统工程图如图4所示, 选用梯形结构的排溢系统。根据单个溢流槽的经验数据可得: 溢流口宽度h=9mm, 溢流口长度L=3mm; 溢流口厚度b=0.5mm, 溢流槽半径R=5mm,溢流槽长度中心距H=24mm; 溢流槽脱模斜度取10°;溢流槽深度取20mm,共 3 个溢流槽。排气道相关尺寸选取为:排气槽深度 0.15mm;宽度 20mm;排气槽在离开型腔 20mm,将其深度增大至 0.3mm,以提高排气效果。
图4 溢流槽工程图
5 成型零件与结构零件的设计
本模具采用整体组合式结构, 型腔和型芯由整块材料制成, 然后装入模板的模套内, 再用台肩或螺栓固定。
5 .1 成型尺寸计算
在模具设计中,确定成型尺寸时,通常考虑成型收缩率的影响,并考虑压铸件的公称尺寸误差和成型零件在修研及受冲蚀时产生的损耗。
成型零件尺寸的计算公式如下:
式中

—计算后的成型尺寸,mm;A —铸件的基本尺寸,mm;

—压铸件的计算收缩率,%;n—补偿和磨损系数。
模框尺寸: 由于对型芯的外轮廓无特殊的要求, 根据抽芯机构和浇注系统, 选择动、定模芯的外轮廓的长宽高尺寸均为290x260 x 100。
中心距位置尺寸计算: 为了简化中心距离,位置尺寸的计算公式,铸件中心距离,位置尺寸的偏差规定为双向等值。公式为:

拔模斜度:铝合金材料的熔点相较锌合金等低熔点金属高,粘模比较严重,充型时对型腔的冲刷和侵蚀也较严重,为了降低拔模难度,延长模具使用寿命,设计型腔时尤其要注意增加拔模的角度、加大过渡圆角半径和提高型腔的表面粗糙度值,一般拔模角度为 1°~1.5°;过渡圆角半径为 R1-R3;表面粗糙度为 Ra0.8~0.4μm,并经表面抛光。
5.2 模框尺寸的计算
模框基本尺寸计算是在模芯确定尺寸的基础上加上周边和底部需增加的尺寸,再加上有侧抽芯时局部需增加的尺寸。根据模框尺寸选取表可得:定模框尺寸:长 600mm,宽 500mm,高 170mm;动模框尺寸:长 500mm,宽 480mm,高 190mm;模框压板槽 40mm。
6 侧抽芯机构的设计
当压铸件上带有与开模方向不同的侧孔或者侧凹结构时,压铸模具的开合模和取出铸件等动作将无法完成,因此必须将压铸模上设置活动型芯以便在形成侧孔或者侧凹的同时不影响模具的正常动作。若侧向型芯设置在定模上,为了能够首先打开压铸模,要求必须在开模之前抽出型芯。若型芯设置在动模上,也要在开模行程中将活动型芯抽出,才能保证将压铸件从压铸模中取出。另外,合模时抽芯机构必须复位到压铸起始位置,以便进行下一次压铸循环。完成以上侧向型芯抽如及复位功能的机构称为抽芯机构。
侧抽芯机构一般由下列几部分组成。成型元件、运动元件、传动元件、锁紧元件、限位元件等。侧抽芯机构有多种形式,但应用较多的是斜销机构和斜滑块机构。斜销机构结构简单,用于抽出接近分型面、抽芯力不太大的型芯;斜滑块适合抽出侧面成型深度较浅、面积较大的表面。本文选择了斜销侧抽芯机构。
6.1抽芯力计算
6.2抽芯距离确定
根据抽芯距离的公式:

;式中

—抽芯距离,mm;

—侧孔、侧凹或侧凸形状的深度或长度,mm 取
=23.5;K-安全值,斜销机构一般取 3~5mm。本课题铸件的 h
=23.5mm, 取
=3.5mm,因此,S=27mm。斜销斜角α是的大小决定斜销所承受的弯曲应力,斜销的有效工作尺寸以及侧抽芯动作所需要的有效开模距离,是决定斜销抽芯机构工作效果的重要参数,一般情况下,斜销斜角α应在 10°~25°之间选取。取α=15°。侧滑块的定位装置:由于滑块的尺寸较小,不宜采用沿水平方向侧抽芯,所以采用侧抽芯方向向上的定位装置的形式。
6.3 侧滑块的楔紧装置
楔紧块的结构和装固形式应满足以下几点要点:1、在较长的周期内,保证楔紧功能的可靠性,2、便于制造和研发。3、便于维修和更换。采用整体式结构,楔紧力大,弹性变形量小,安装可靠。
7、模具总装图及过程模拟
利用 UG 软件,对铸件的开合模过程进行了模拟,模具的运动过程流畅,零件之间无干涉现象。压铸模开模抽芯动作,压铸模合模动作,如图5所示。
图5 模具开合模拟
8 结论
通过对铸件的工艺性分析,设置了分型面,金属液从铸件一侧进入。横浇道采用等宽横浇道形式,溢流槽设置在铸件末端,动模芯上。根据铸件的通孔结构特点,采用了斜销抽芯机构,,抽芯距离为 27mm,导向角 15°,确定的动模框尺寸长×宽为 500×480,厚度为 190mm;定模框尺寸长×宽为600×500,厚度为 170mm;模框的导柱直径 38mm、长度 170mm。