文:重庆大江美利信压铸有限责任公司 万 恒
摘 要:某款曲轴箱件采用1600吨压铸机生产,该产品在生产过程中内部气孔的缺陷较多。本文对产生的原因进行了分析,采取针对性的措施,使产品质量得到稳定提高。
1 主要问题
曲轴箱机油盘结合面加工后出现大量气孔,气孔规格在0.8-1.5mm,数量在5-15个不等,腔体泄漏率比率在20%时左右。
详见气孔分布区域分布(图 1)
2 产品及模具结构分析
2.1 产品结构分析
为了更加清楚的了解产品结构,我们首先使用软件对产品壁厚进行检测,产品上最大壁厚为8mm,一般壁厚在4mm。
2.2 模具结构分析
该产品现有模具方案主要采用两股主浇道从产品两侧进行进浇,进而对产品整个部位进行充填。(详见图2)
3 原因分析
3.1 产生气孔的原因分析
首先我们从人机料法环进行产生气孔的原因分析。(图3)
3.1.1 壁厚过厚
经过查看毛坯及产品3D,曲轴箱件机油盘结合面处(红色区域)壁厚达到了8mm,毛坯加工余量为1.2mm,壁厚过厚及加工余量过多是产生气孔的原因之一。(图4)
3.1.2 模具设计不合理
因该模具采用的是在产品两侧进行进浇,铝液经过两股主浇道后在机油盘结合面相遇,形成对冲,造成紫色区域区域形成卷气,在模具设计时,该区域无设置排气槽,导致气体无法排出。此方面也是形成气孔的原因之一。(图5)
图 5
3.1.3 工艺参数设置不合理
该产品生产时设置的压铸工艺参数如下:1)一速启动速度为0.3m/s。一速启动位置太快导致压室内气体无法排出也是导致产品形成气孔的原因之一。(图6)
3.1.4 模具的喷雾和吹气时间设置不合理
在机油盘结合面喷雾时间为3s,吹气时间为1s。喷雾时间过长和吹气时间过短,导致模具上残留着水分也是导致产品形成气孔的原因之一。
4 解决方案
4.1 壁厚过厚解决方案
4.1.1 针对产品机油盘结合面壁厚过厚的问题,我们通过对该处模具结构的优化进行改善。即模具上该处做成网格结构,将该面的加工余量由1.2mm 减少至0.7mm(图 7)
4.2 模具设计不合理的解决方案
4.2.1 根据模具结构分析,现将一处主浇道(下图左侧方框区域)进行封堵,同时将机油盘结合区域制作成多个网格镶块配合装配的方式,一方面网格镶块可以减缓铝液在该处相遇的冲击。另一方面镶块之间的间隙形成通道进行排气。(图8)
4.3 工艺参数设置不合理的解决方案
4.3.1 对一速速度进行重新设置,将之前的一速速度 0.3m/s 改为 0.2m/s。从而使压室内的气孔有更多的时间从压室内排出,不带进模具型腔内。(图9)
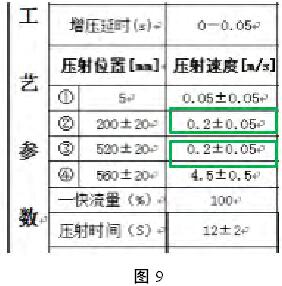
#p#分页标题#e#
4.4 模具的喷雾和吹气时间设置不合理的解决方案
4.4.1 对模具的喷雾和吹气时间进行重新设置,
将原有的喷雾时间3s,吹气时间 1s 改为喷雾时间1s,吹气时间2s.使得模具上水分被吹干。
5 改进效果
5.1 经过上述措施的实施,产品质量状况如图所示,在客户处机加后曲轴箱机油盘结合面气孔不合格率由 20%降为 0.5%。
5.2 产品改进前后对比
6 总结
压铸件气孔质量问题在铸造行业中普遍存在,需要从产品、模具、工艺参数等方面逐一进行分析,找出解决方案,进而提高产品的良品率。