文:浙江大学宁波理工学院贾志欣
摘要 形状复杂、壁厚不均匀的压铸件由于结构原因,在成形过程无法及时补缩,易出现缩孔缺陷。实施局部挤压辅助技术是提高这类压铸件质量的有效方法。给出了压铸成形过程中局部挤压的原理和结构,分析了挤压深度、挤压压力、挤压延迟时间和挤压持续时间对压铸件质量的影响,并通过实例说明了局部挤压的应用效果。
关键词 压铸;局部挤压;缩孔;气孔
高压压铸(High Pressure Die Casting,HPDC)因其具有效益高、少无切削等优点已在汽车、电子、仪器仪表、航空等行业广泛应用。其高效性、高品质,且能生产结构复杂的产品,非常适用于产品的大批量生产。随着汽车行业的迅猛发展,对汽车零部件也有了更高的要求,高性能、轻量、低成本是发展的趋势。近年来急剧增长的汽车轻量化需求,带动了汽车铝合金精密压铸件产业的高速发展,发动机缸体、变速器壳体、离合器壳体等引擎、底盘相关零件都普遍采用铝合金压铸件。形状复杂、壁厚不均匀的罩盖类薄壁压铸件需求日趋增多,而且要求通过高压下的渗漏测试,给压铸工艺和模具设计带来了挑战。气孔、缩孔、冷隔等是压铸件的常见缺陷,局部挤压是在铸件厚壁热节处设置增压通道实施局部增压,解决厚壁处易产生的渗漏、缩孔问题,从而提高铸件品质,减少废品率。本课题在分析压铸成形中气、缩孔形成机理的基础上,给出了压铸成形过程中局部挤压的原理和结构,分析了挤压深度、挤压压力、挤压延迟时间和挤压持续时间对压铸件质量的影响,并通过实例说明了局部挤压的应用效果。
1、压铸件气孔、缩孔产生原因
在压铸生产中,由于受到产品结构、工艺参数、模具结构、压铸工艺等多种因素的影响,压铸件常会存在一些缺陷,如气孔、浇不足、缩孔、冷隔、氧化夹渣等。这些缺陷影响着产品的外形尺寸、力学性能、疲劳强度、高压下的渗透性等。缩孔、气孔是影响压铸件高压渗透性的主要因素。
壁厚不均匀的压铸件易在厚大的热节部位产生缩孔,缩孔产生的原因是凝固时体积收缩造成的。 以ADC12合金为例,其在高温液态时的密度为2.6g/cm3,而凝固后为2.7g/cm3,约有4%的密度差,因此,在没有外来补缩情况下将会造成4%左右的缩孔,缩孔截面往往呈现无规则的形态。
气孔是在金属液压射过程中卷入了料筒、型腔内的空气以及冲头润滑油、脱模剂产生的气体并无法排出,从而被充填至模具内部形成气孔,气孔一般为圆形。
在多数情况下,在铸件出现气孔、缩孔时,可以通过修改浇口位置、增添渣包、修改工艺参数(如铝液温度,低速和高速点切换位置,压铸压力等)来有效提高产品合格率。但是对于一些局部结构复杂、壁厚不均、壁厚悬殊处离浇口较远,最远端位置不在分型面上而无法设置渣包和排气槽的零件,仅通过调节压铸工艺参数,无法使缺陷得到改善。采用局部挤压是减少关键部位气、缩孔的重要方法。
2、局部挤压原理和结构
局部加压是在模具内直接安装油缸,对产生缩孔的部位直接进行加压,抑制缩孔,以获得高质量的压铸件。局部加压结构示意图见图1。在金属液充型完成之后,经过一定时间,亦即在铸件凝固过程中,金属液在型腔中处于半固态时,在最后凝固的厚壁处通过挤压杆施加压力以强制补缩来减少或消除该处的缩孔、气孔缺陷,提高压铸件加压渗漏检测的通过率。
局部挤压结构主要由挤压油缸、挤压销、挤压衬套及相关连接装置组成,其用于挤压的结构装置可根据设计要求安装在模框、模芯上,见图2。
局部挤压成形方式主要分为以下两种,见图3。一种是在铸件成形表面进行加压作用,铸件被加压的部位比实际高度高出一定距离,以免把铸件表面层冷料挤入铸件内部,高出部分则直接通过后续机加工去除,同时侧壁单边留2 mm以上,避开硬质层,见图 3a;另一种是在铸件的厚壁部位设置局部挤压设备,直接压铸铸件底孔,见图3b。
3、局部挤压工艺的主要工艺参数
在局部加压工艺中,挤压深度、挤压压力、挤压开始时间、挤压结束时间是影响加压工艺效果的主要参数。
3.1 挤压深度
挤压深度,即增压压入量,决定了被压入铝液的量。其大小与压铸件厚大部位的组织有直接关系。挤压深度太小,补入厚大部位的金属液不够,补缩不足,达不到局部减少或消除气孔、缩孔和缩松等铸造缺陷的目的;挤压深度太大,不仅需要较大压力的挤压油缸设备,挤压销由于温度过高也容易损坏,而且挤压销容易弯曲。因此需要确定合理的挤压深度。
图4是局部挤压深度示意图。方块体积为V,材料的体积收缩率为S,则理想的体积收缩量为V•S,就是金属液补充量,如采用挤压杆的直径为d,则可以计算理想的挤压深度l为:
分析挤压深度的主要目的是为了判断挤压延迟时间的合理性,并为挤压持续时间的设置提供基础。
3.2 挤压压力
挤压压力的大小取决于油缸直径 D。油缸直径 D过小,局部挤压压力不足,会造成补 缩不足;油缸直径D 过大,会使油缸体积大,造成浪费。
分析挤出销受力(见图5),p为铸造压力,d为挤压杆直径,p′为挤压油缸压强,D为油缸缸径。根据帕斯卡原理有:
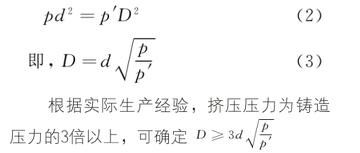
3.3 挤压延迟时间(挤压挤入时机)
挤压延迟时间为金属液充填结束至局部挤压工艺开始实施的时间间隔。当金属液处于半固态状态时开始施加挤压压力可获得最佳的挤压效果。挤压延迟时间太短时,金属液还处于流动状态,厚大部位并没有增加凝固结晶压力,导致挤压销变为型芯,无挤压效果;挤压延迟时间太长时,金属液凝固,在模具壁上形成坚硬的硬壳,导致挤压销受阻,无法补缩而不能实现增压效果。挤压销插入的最佳时机与被挤压部位的凝固状态和浇口补缩通道有关。通常挤压延迟时间需要在试模时通过试验来确定有效参数范围,也可以借助 CAE 分析,根据挤压部位的温度场处于固液共存范围时,确定挤压延迟时间。
3.4挤压持续时间
挤压持续时间是指挤压销开始挤压直到回退时所持续的时间。挤压销过早回退,由于与挤压销接触部位还未完全凝固,挤压持续时间短,会造成局部挤压成形的孔底部破裂;挤压持续时间长,不仅会影响效率,而且挤压销会因包紧力过大而容易拉断。挤压销回退的时刻要确保其周边铸件表面温度处于固相线以下。影响气缩孔大小的因素主要是挤压压力及挤压持续时间。
4、局部挤压压铸生产实例
图6为某泵体零件,材质为 A380 铝合金,零件质量为1.42kg,压铸质量(进料、渣包、排气)为2.1kg,其中圆圈部分在 X 射线探伤仪下显示气孔较多,铸件致密度也偏低,在气密性检查中不合格率高达 60%。采用局部挤压,由于压铸件结构复杂,将挤压销安装在滑块中,见图7。采用CAE 分析和实际压铸相结合,确定挤压深度为10 mm,挤压延迟时间为4s,挤压持续时间为8s,压射比压为90MPa,生产出的零件经检测,气缩孔达到了要求。
图8为某壳体压铸件,其中圆圈的部分在 X 射线探伤仪下显示气孔较多。通过局部加压工艺,在 A、B处增设两个挤压孔,提高了相应部位的压铸质量。
5、结 语
分析了压铸过程中局部挤压工艺的主要控制参数及其对压铸件质量的影响。
实践表明,合理确定挤压深度、挤压压力、挤压延迟时间和挤压持续时间,可大幅度减少厚壁处气缩孔,提高压铸件的质量和合格率。